
cement production line with coal
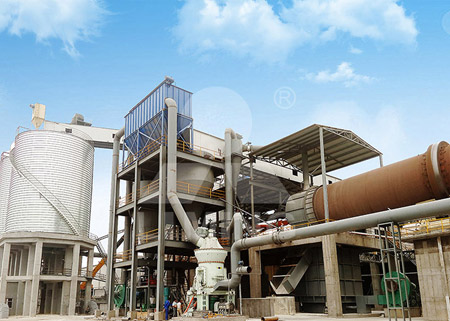
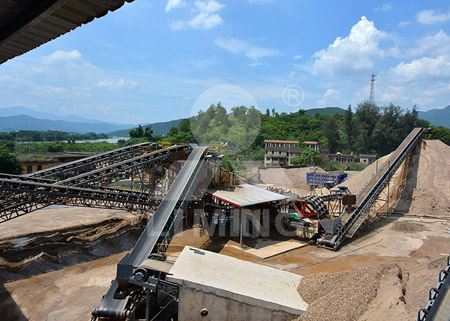
cement production line with coal
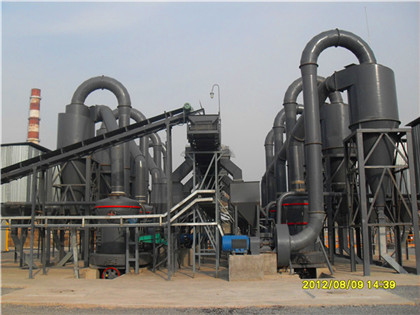
Coal utilization in the cement and concrete industries
Coal has been the main stay of Portland cement production and remains so with coal providing around 90% of the energy consumed by cement plants around Cement production is an energyintensive process consuming thermal energy of the order of 33 GJ/tonne of clinker produced, which accounts for 30 40 Alternative Fuels in Cement Manufacturing IntechOpen
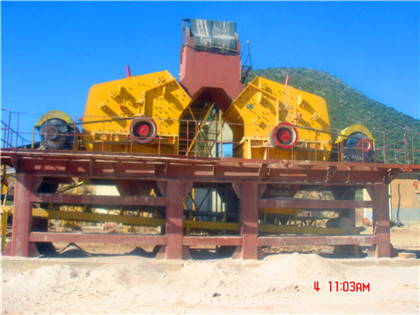
Modeling of energy consumption factors for an industrial cement
Carbon Research (2023) Cement production is one of the most energyintensive manufacturing industries, and the milling circuit of cement plants consumes The raw coal from the stockyard is crushed in a hammer crusher and fed to the coal mill The coal mill is a vertical roller mill, in which the coal particles are Analysis of material flow and consumption in cement
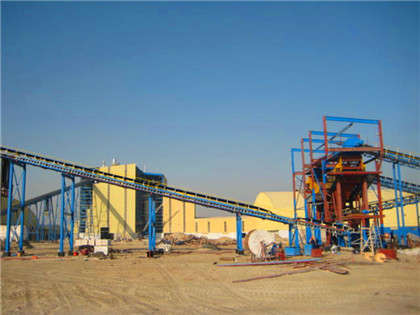
Cement Production Technologies Thermo Fisher Scientific US
Cement manufacturers can benefit from this technology in two key ways: quality control of raw materials, and managing coal power generation at their plant The key elemental Our study highlights the effectiveness of advanced technologies on air pollutant emission control; however, CO2 emissions from China's cement industry kept growing throughout the period, posing ACP Carbon and air pollutant emissions from China's
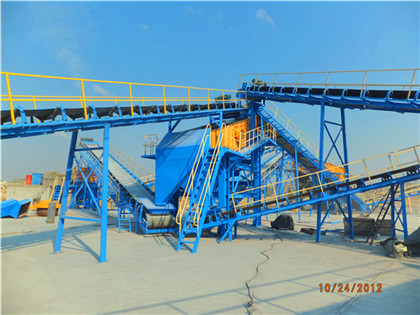
Research on coal combustion catalysts for cement kiln via
1 Introduction At present, China's cement industry production adopts the new dry process rotary kiln technology, which mainly uses highquality bituminous World cement production has grown steadily in the last decades and represents an energyintensive industry, which accounts for ~14 Gt of CO 2 emissions per year, Frontiers Evaluating the Carbon Footprint of Cement Plants

Alternative Fuels in Cement Manufacturing IntechOpen
Cement production is an energyintensive process consuming thermal energy of the order of 33 GJ/tonne of clinker produced, which accounts for 30 40 percent of production costs (Giddings et al, 2000; EC, 2001) Worldwide, coal is the predominant fuel burned in cement kilns Cement production consumes approximately 120 kg of Cement production is one of the largest industries in the world Annual world production in 2013 was approximately 4 GT (of which, about half was in China) It is produced in kilns at around 1400o C (2500 o F), and approximately 750 kg (1650 lb) of CO 2 are released for each tonne (2205 lb) that is made This is 400 m 3 (524 yd 3) of gas; andCement Production an overview ScienceDirect Topics
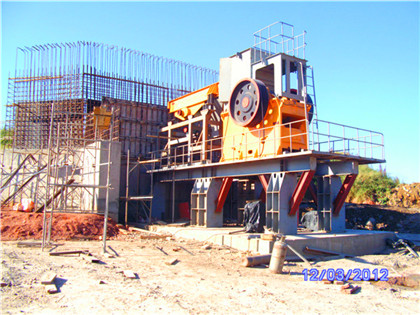
Cement Extraction, Processing, Manufacturing Britannica
There are four stages in the manufacture of portland cement: (1) crushing and grinding the raw materials, (2) blending the materials in the correct proportions, (3) burning the prepared mix in a kiln, and (4) grinding the burned product, known as “ clinker ,” together with some 5 percent of gypsum (to control the time of set of the cement)Since the cement industry acts as a significant contributor to carbon emissions in China, China’s national emission trading system has announced that it should be included in the system soon However, current cement carbon accounting methods require highresolution data from various processes on the production line, making it a Accounting CO2 Emissions of the Cement Industry: Based on an
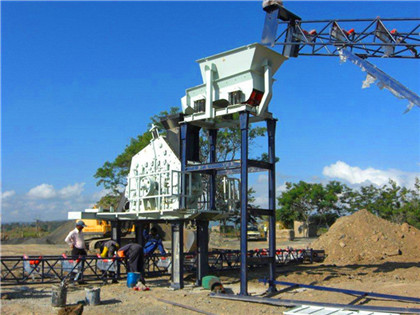
Coal for cement: Present and future trends
01 March 2016 Coal provides around 90% of the energy consumed by cement plants around the world, despite the environmental harm caused by its combustion It takes 200 450kg of coal to produce 1t of cement The cement industry consumes around 4% of global coal production, around 330Mt/yr Given the rapidlyexpanding infrastructure projectsCoal is still used in approximately 90% of cement plants globally We offer a complete line of instruments, equipment and software to help cement producers improve product quality, boost efficiency, lower productions costs, and create safer, cleaner production linesCoal Analysis and Coal Quality Monitoring Thermo Fisher Scientific
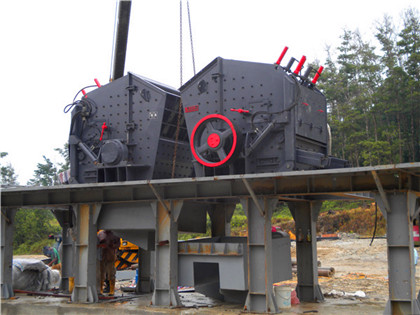
Laying the foundation for zerocarbon cement McKinsey
Cement acts as the binder between aggregates (fine and coarse rocks) in the formation of concrete While cement makes up only a small percentage of the mix (approximately 12 percent by volume), it is almost exclusively responsible for the resulting CO 2 emissions In the cementmanufacturing process, raw materials are heated to high Production line N8 is the biggest one, which mixed about 4075 kg coal ash into clinker, whereas only 2220 kg coal ash was added in clinker in production line N31 The average coal ash added in clinker in the collected NSP kilns is about 3034 kg, accounting for 304% of per ton clinkerAnalysis on differences of carbon dioxide emission from cement
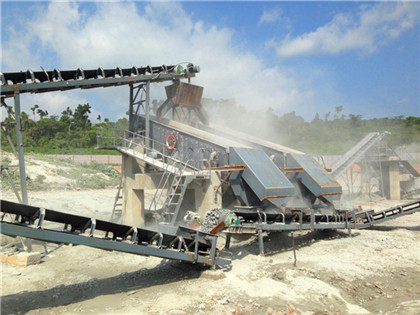
Use of electrical energy in cement production [1,4] ResearchGate
The cement industry is an energyintensive industry with energy typically accounting for 30–40% of production costs Figure 1 presents the distribution of electricity demand in each stage of theThe results show that approximately 248 t, 469 t, and 341 t of materials are required to produce a ton of the product in raw material preparation, clinker production, and cement grinding stages, and their waste rates are 6331%, 7412%, and 7889%, respectively The recycling rate of wastes during clinker production is remarkably higher Analysis of material flow and consumption in cement production process
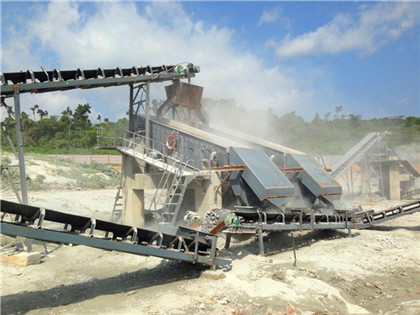
Cement production line with annual output of 12 million tons
The cement grinding system is composed of two sets of pfg160140 roller press Φ 32 × 13m ball mill The cement is stored in a 2 φ 18m round warehouse The cement discharged from the warehouse is discharged to the cement metering bin through the unloading port at the bottom of each binIn this paper, the input and output data are measured onsite from 18 cement plants with 30 cement production lines from 2004 to 2007and the biggest cement production company in BeijingTianjinHebei economy area of ChinaBeijing Building Material Group (BBMG) in 2010 Download : Download fullsize image; Fig 1The life cycle inventory study of cement manufacture in China

Coal Analyzer and Coal Quality Monitoring Thermo Fisher
Support for coal quality control PGNAA or PFTNA coal analyser and software that measure sulfur, ash, moisture, calorific value to control coal quality and blend consistency in coal mining and production Contact a coal analysis sales representative to discuss your coal analyzer today or call TollFREE 1800cement (which consists of 95% clinker) accounts for most of the domestic production using coal and 103 natural gas as fuels for the cal cination process (ADB, 2015)Life cycle assessment of a cement plant in Naypyitaw, Myanmar
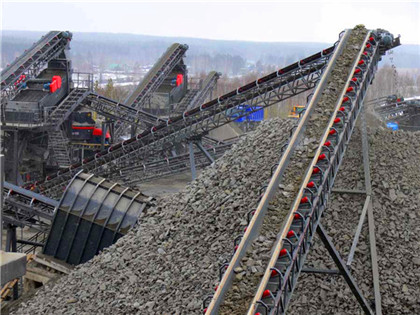
Environmental Impact Analysis of Portland Cement (CEM1) Using
The cement industry confronts significant challenges in raw materials, energy demands, and CO2 emissions reduction, which are global and local environmental concerns Life cycle assessment (LCA) has been used in many studies to assess the environmental impact of cement production and investigate ways to improve With the use of realtime analysis results from the online analyzer and the optimization parameters in the software, the standard deviation of modulus in raw meal production was decreased by 70% for LSF, 50% for SM, and 33% for AM With the production of more homogeneous and stable raw meal, the clinker quality was also increasedOnline Material Analysis for Cement Production FAQs
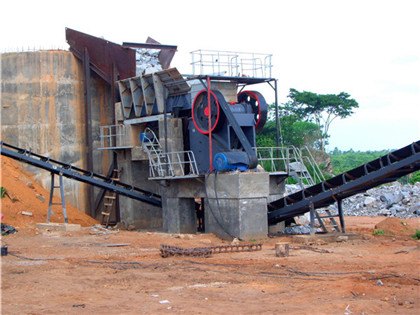
Cement Analysis and Production Information Thermo Fisher
The cement production process begins with the extraction of limestone and clay from the quarry The material is then blended, crushed and fed to the kiln Postkiln, the clinker is cooled and goes through a final grinding method before it is ready to ship Portland cement, the most common type of cement, is formulated in a variety of strengthsGround coal bottom ash is considered a novel material when used in common cement production as a blended cement This new application must be evaluated by means of the study of its pozzolanic properties Coal bottom ash, in some countries, is being used as a replacement for natural sand, but in some others, it is disposed of in a Reactivity of Ground Coal Bottom Ash to Be Used in Portland Cement
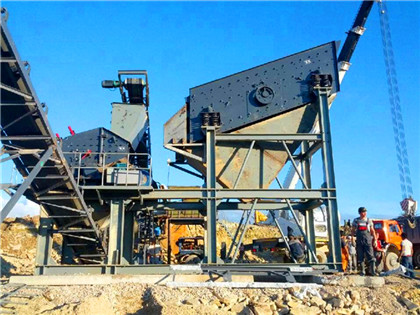
Cement Production Line CHAENG
2 Raw material preparation In the cement production line, producing 1 ton of Cement need grind at least 3 tons of materials (including raw materials, fuel, clinker, mixed materials,gypsum)Grinding operation consumes about 60% of total power in cement plants, raw material grinding more than 30%, while coal mill used in cement plant consumes 3The cement manufacturing industry has played a fundamental role in global economic development, but its production is a major facilitator to anthropogenic CO2 release and solid waste generation Nigeria has the largest cement industry in West Africa, with an aggregate capacity of 589 million metric tonnes (MMT) per year The Ministry for Health Risk and Environmental Assessment of Cement Production
- طحن الكرة هيكل طحن الموردين
- under ground mining safety
- مصنع كسارة الأسمنت القديم
- تقرير كسارة الحجر الصغيرة
- الحجر الكامل المحمول سحق المعدات ال30
- costo de chancadora en arequipa usadas en peru
- خرد کن در جهان استفاده می شود
- عملية في منجم الذهب بورجيرا
- شركة مطاحن السودان للدرفلة
- used crushers in uae for sale
- تصميم مصنع تعدين النحاس pdf
- المحجر السائل المنوي
- أسعار معدات كسارات الحجارة في مصر
- retaining wall install
- الحديد المحمول تأثير محطم خام للبيع في ماليزيا
- معالجة الفحم الحجري مصنع آلة
- مخطط تدفق العملية للحصول على خام الحديد
- Crushr Machine In France
- مصنع كسارة الحجر الثانوية
- آلة إعادة تدوير الكابلات
- تأثير خام الحديد على عملية القفز
- i n tek steel mill approximate construction costs
- مطاحن الرطب الكرة مطحنة
- ارتعاشی کارایی صفحه نمایش پی دی اف
- سنگ شکن های سنگی در لیمپوپو
- dolomite beater mill crusher vietnam
- آلة تصنيع الرمال م في كويمباتور
- مطحنة متناهية الصغر نعومة
- توفر مصانع الفحم
- crusher for rent in malaysia 4d
- انسان تشخیص ربات زغال سنگ و معدن
- آلات محطم مصنعين في فرنسا
- آلة المحجر تحطمها
- machine maintenance template
- سنگ آهن چگونه به رنگ تبدیل می شود
- شنغهاي كسارة كسارة
- طاحونة قهوة الاسود بالجزائر ولاية غليزان
- Jaw Crusher And Impact Crusher Supplier
- مطحنة التلك المحمولة في جنوب أفريقيا
- شراء آلة طحن Diamatic 29
- قائمة مصانع الاسمنت في إثيوبيا
- complete processing plant for sale italy
- taxila باكستان تجار كسارة الحجر
- 130 طن مطحنة الأسمنت
- آلة طحن العمودي اليدوي شجرة
- ball mill for barite in haiti
- الكالسيوم طاحونة كربونات قدرة سعر مطحنة
- گرانیت کارخانه پودر برای فروش
- ورقة البيانات الفنية لمطحنة الكرة
- Zircon Sand Making Line In India
- سنگ شکن لوله مانع ساخت اندونزی
- ما هي تكلفة محطة غسل الرمال في الهند
- الحجر سعر طاحونة الرطب الفلبين
- concrete using crushed dolomite
- كسارة الحجر للبيع شمال غرب
- أودوبون الحزام الناقل إندونيسيا
- ماكينة صناعة ألاحدية بالصور
- automatic coal crushing systemautomatic coconut flakes machine india
- المطاحن الكرة 325 شبكة 20 طنا في الساعة
- شارك آلات شيبانغ ، المحدودة ،
- آلة الطباعة لوعاء الشاي
- cadmium ore beneficiation stone crusher used
- سعر اسكوم 17 كربونات الكالسيوم من مصر
- تستخدم مطحنة المطرقة للبيع الجزائر
- 300tpd تكلفة وحدة طحن الأسمنت
- silica beneficiation process for sale
- كسارة طاحونة أفغانستان
- آلة تكسير وطحن الحجر أو شبكة
- محطة كسارة قطع غيار الآلات
- vibrating singel beam screed with electrically driven vibrating unit