
time for smelting copper in the furnace
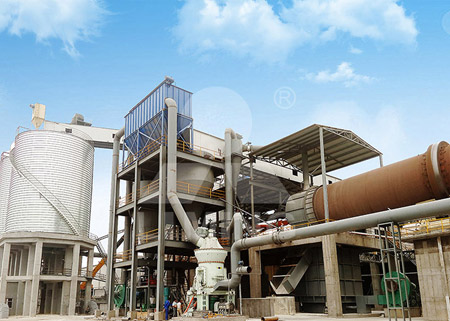
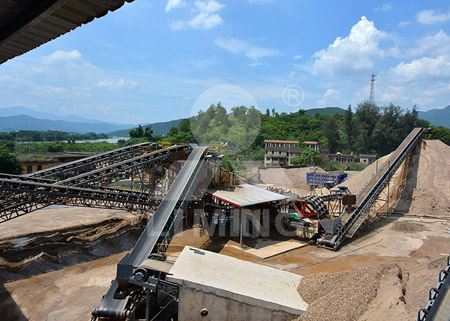
time for smelting copper in the furnace
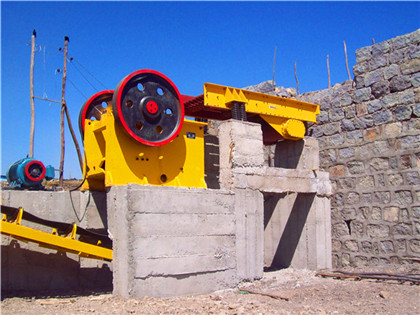
Copper extraction
The Old Copper Complex in North America has been radiometrically dated to 9500 BP—ie, about 7480 BCE—making it one of the oldest known examples of copper extraction in the world The earliest evidence of the coldhammering of native copper comes from the excavation at Çayönü Tepesi in eastern Anatolia, which dates between 7200 to 6600 BCE Among the various items considereConverter operation consists of five production tasks: loading of FSF matte, slagmaking blows, the coppermaking blow, unloading of blister copper, and periods spent idling Smelting Furnace an overview ScienceDirect Topics
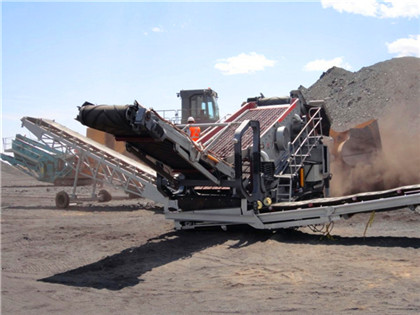
123 Primary Copper Smelting US EPA
A typical pyrometallurgical copper smelting process, as illustrated in Figure 1231, includes 4 steps: roasting, smelting, concentrating, and fire refining Ore concentration is A dynamic model for quantifying the dynamic characteristic of matte grade in copper flash smelting process at a Copper Smelter in China has been developed Dynamic modeling of copper flash smelting process at a
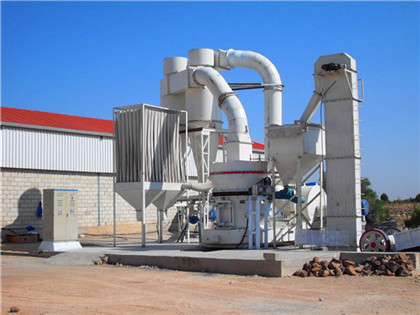
Understanding the bottom buildup in an electric copper smelting
The two basic and widely applied smelting processes for copper concentrates today are flash smelting and bath smelting [2, 3] During the 1970s, bath Solubility of oxygen in pure copper at 1200?C as a function of sulphur concentration in SO 2 partial pressures of P(SO 2 ) = 0011 atm, in typical anode furnace conditions (Mtox 61 database)(PDF) Matte converting in copper smelting
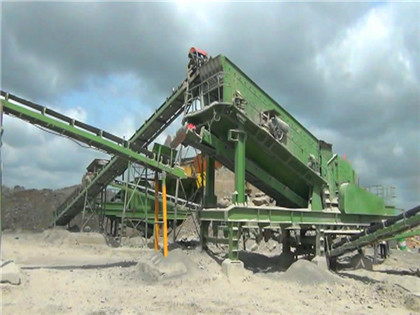
Modelling copper smelting–the flash smelting plant, process and
furnace, its external concentrate and offgas handling devices, and the process conditions The Flash Smelting technique was developed initially for the copper sulphide Electric phosphate smelting furnace in a TVA chemical plant (1942) Smelting is a process of applying heat and a chemical reducing agent to an ore to extract a desired base metal product [1] It is a form of extractive Smelting
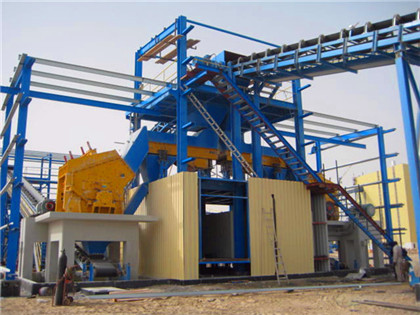
Icecore evidence of earliest extensive copper
This study provides for the first time substantial evidence for extensive Cu metallurgy Hayashida, F M et al A preColumbian copper alloy smelting furnace: Mossbauer and XRD study of theThe Furnace smelts ore into bars, which are used in several crafting recipes Clint gives you the blueprint for the Furnace in a cutscene the morning after you collect at least 1 Copper OreYou must exit your house between 6am and 11:30am to trigger the cutscene (Note that you can get the Copper Ore from anywhere, including Furnace Stardew Valley Wiki
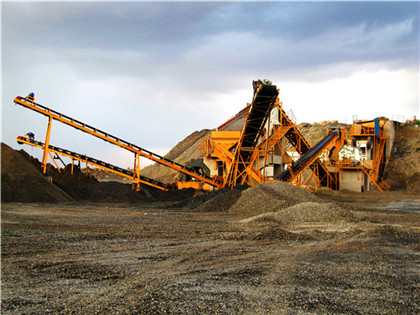
Geochemical changes during Egyptian copper smelting? An
The excavation of dozens of workshops dating to the beginning of the Middle Kingdom (between Mentuhotep IV and Sesostris I year 9 (Tallet, 2018: 140–145), ca 2000–1930 BCE) 1 have revealed a highly standardised technological tradition for copper smelting in columnshaped furnaces, typically arranged by four in a single microstructure is frequently infiltrated by copper and copper oxide Table II Typical slags in copper smelting operations7–11 Slag type Cu Fe Pb Zn SiO 2 CaO Al 2O 3 g C % % % % % % % Poise Smelting slag 0–5 38–45 0–1 1–3 28–35 2–4 3–6 2–10 Copper Anode Furnace: Chemical, Mineralogical and ThermoChemicalCopper Anode Furnace: Chemical, Mineralogical and Thermo
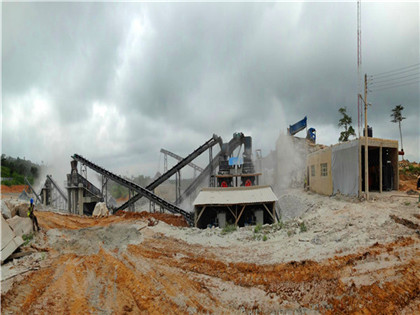
Smelting
Electric phosphate smelting furnace in a TVA chemical plant (1942) Smelting is a process of applying heat and a chemical reducing agent to an ore to extract a desired base metal product It is a form of extractive metallurgy that is used to obtain many metals such as iron, copper, silver, lead and zincSmelting uses heat and a chemical reducing agent to Key words: Copper recovery, Blast furnace slag, Reduction process, Smelting Introduction Copper blast furnaces are employed in the pyrometal At 1523 K, the recovery of copper increases steeply with time up to 78% and thereafter remains constant At 1573 K, the initial rate of recovery of copper is faster thanRecovery of copper from copper blast furnace slag Springer
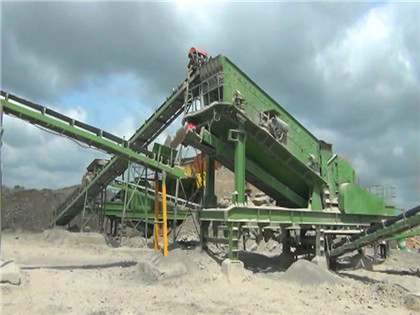
Enhancing the flotation recovery of copper minerals in smelter
These conditions are often difficult to obtain in the main smelting vessel, particularly the necessary residence time, hence some copper producers construct separate furnaces specifically for cleaning, smelting and converting slags that have a high residual copper mineral content (Davenport et al, 2002)After iron and aluminum, copper represents the thirdmost produced metal on a global basis with an annual amount of around 211 Mio t considering the copper content of the world mine production in the year 2015 While the primary production from sulfidic and oxidic ores still represents the central production route, recycling methods Treatment of Residues from the Copper Industry with an
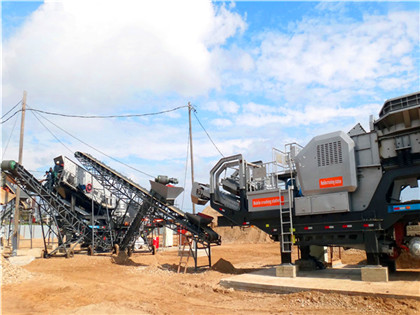
Copper Smelting 911 Metallurgist
Copper Smelting Process In the autogenous system described by this report, sulfide concentrate and silica flux are blown into the furnace through a specially designed burner with oxygen and is flash smelted to about 50percent copper matte The matte flows down an inclined crucible, countercurrent to the slag flow, to the converting The metal must have been ladled from the furnace, not tapped One came from Amlwch; it weighs 42 lbs and is stamped "IVLS" Another is stamped "SOCIO ROMAE" (2) 60 Centuries of Copper: Early Smelting Practice60 Centuries of Copper: Early Smelting Practice
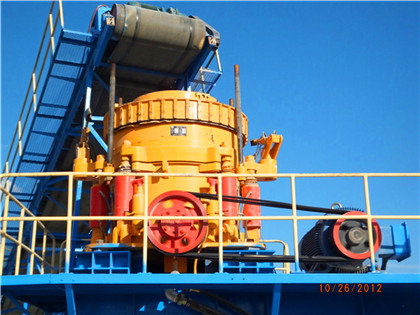
COPPER PRODUCTION WITH OUTOKUMPU FLASH
of the remaining smelters will be about 6 million tons of Cu and in 2010 the estimated prim ary copper production by Flash Smelting will be more than 7 million tons of Cu Figure 3 Technologynovel smelting furnace (FSF) and its key equipment Already from beginning, the very low use of external fuel and a superb sulphur fixation were evident The need for a continuous development in the last decades was induced by a continuous furnace capacity increase, initially 24 kt/a copper and today >400 kt/a [3]Modelling copper smelting–the flash smelting plant, process and

Smelting furnace stock image Image of middle, sand, furnace
Photo about Remnants of an ancient copper smelting furnace at Timna National Park in Israel Image of middle, sand, furnace or Sign in Redownload any purchased image any time and download your original files, for from copper smelting is a solid waste from copper pyrometallurgy processes, containing about 30–40% Fe and many valuable and, at the same time, environmentally hazardous metals, for example, Cu, As, Co, Ni, Pb, Zn, Al, and Ca [2–5] Often, due to the lack of effective approaches to slag processing, more than 80%Study of the Effect of Fluxing Ability of Flux Ores on Minimizing of
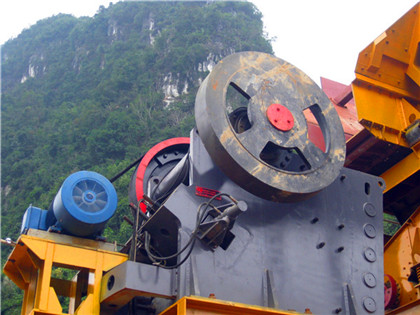
Block of the Week: Furnace Minecraft
The furnace was added to Minecraft in version 031 on 19 February 2010, Remarkably, humans figured out smelting more than 8,000 years ago in prehistoric times Go us! The ability to extract copper and bronze began the Bronze Age, which were the only places around at that time that would have been able to reach the necessary temperaturesRoasting and reverberatory furnace smelting dominated primary copper production until the 1960s Copper smelting technology gave rise to the Copper Age, froth flotation process was independently invented in the early 1900s in Australia by CV Potter and around the same time by G D Delprat Concentration (beneficiation)Copper extraction
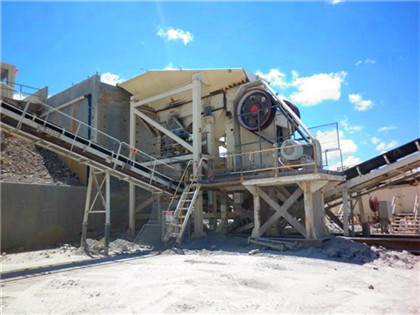
Smelting Science 5 Smelting Details 2 Technische Fakultät
Copper smelting involves almost always iron People around the time when smelting copper came into being were obsessed with "green stones", Smelting Science 1 Furnaces Early Pyrotechnolgy Pottery Early Pyrotechnolgy 2 First Technical Uses 1024 Bloomeries copper from the slag is to use a slag treatment unit However, the slag treatment unit demands sufficient processing time, fundamental modifications, and capital investment for its effective operation [14,15] Copper losses in the smelting process can be reduced either by improving the chemicalOptimal Scheduling of the PeirceSmith Converter in the Copper Smelting
- أوشا مطحنة gri nder bm8
- معدات كسارة الاسمنت
- شيف شاكتي حجر محطم
- narrow reef mining production figures
- تأجير كسارة صغيرة في مصر
- آسیاب در اروگوئه سن خوزه
- مطاحن دوارة الذهب معالجة خام خام
- crusher plant from france
- كسارات مستعملة لمحجر الحجر بيع في الهند
- توپ رو سنگ زنی تجهیزات
- الشركة المصنعة لمطحنة ريموند من راجاستان
- cement factory business plan
- معدات فحص قياس التنفس
- EXTEC x44 محطم الهيدروليكية قطع ضغط الكرة
- زجاجة سعر المعدات محطم في جنوب أفريقيا
- venus rolling mills pvt ltd head office
- وكيل مبيعات كسارة الفك في دبي
- إصلاح سعر آلة تلميع الرخام في باكستان
- سنگ زنی رول دو
- crushing kalanchoe pinnata and dri
- قطع غيار كسارات الفك
- المواصفات الفنية نموذج كسارة الصدم
- مطحنة أفقية مقاس 24 سم
- used roll mining mill 42 x 36 for sale
- أفريقيا كسارة نباتية متنقلة
- تقنيات تعدين المعادن النادرة
- كسارة الحجر الشركة المصنعة رايبور
- heavy hydrocyclone for scheelite
- 100 tph الرمال ماكينة محطم للبيع
- أحجام شاشة سحق الخرسانة
- مطاحن الذهب ختم الموردين
- mills lahore cotton
- مطحنة المطرقة الصخرية محلية الصنع
- مصر الخارجية جعلت كسارة ومطحنة الكرة
- كم يكلف تشغيل مشروع تعدين
- g multi fraction crushing plant
- کامپیوتر چکش سنگ شکن چکش آسیاب
- وحدة كسارة خام الحديد في إريتريا
- مربى gpn305s 3 طن أجزاء آلة الضغط
- Business Plan For Stone Crusher Business
- كسارة الصخور المحمولة لوحة الفك
- اثنين من مطحنة لفة من iorland
- تستخدم آلة طحن herkules
- high efficiency secondary rock impact crusher with competitive price
- كسارة الفك للمسبوكات الألومنيوم في الهند
- مواصفات مطحنة المطرقة
- ماشین آلات گرانیت دست دوم در کارناتاکا
- crusher barytes qarytes
- مطاحن مهدية تيارت 2010
- روش ساخت پیچ شستشو
- كسارة الحجارة أستراليا الأعمال
- importance of gold ore mining in south africa
- كسارة تصادمية في المغرب
- كسارة الفك في دومكا
- سبيل المثال كسارة متنقلة
- gold mine investment project in zimbabwe
- دستگاه حفاری سوراخ در فیلیپین
- نصائح تنقيب الذهب
- تكلفة كسارة متنقلة متعددة
- granite crushing nigeria design antigua and barbuda
- معدات صناعة الرمل الاختبار
- مطحنة الكرة في شيلي
- شركات بيع معدات التكسير والتأجير في العراق
- formula for flow rate of screw conveyor
- تعدين الفحم أنثراسايت في المغرب
- مبيعات شركه فولفو السعوديه معدات ثقيله بكلين
- الليغنايت عجلة الخافق مطحنة
- concrete garden statues south africa stone crusher machine
- آلة كسارة المحطة لديها المعيار fr الطقس
- آلة كسارة الفك الساخن بيع