
ball mill fully operational ball mill
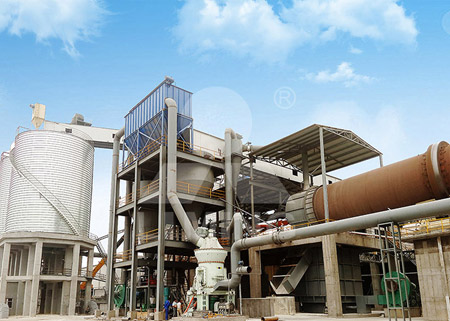
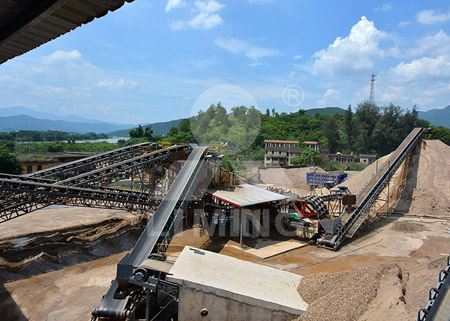
ball mill fully operational ball mill
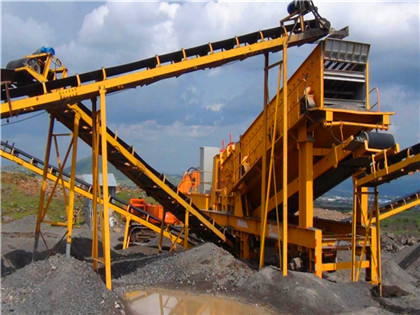
(PDF) Effect of operational variables on ball milling
This work consisted on experimental batch grinding tests with a 30 x 30 cm ball mill in which operational variables were altered Abstract With a view to developing a sound basis for the design and scaleup of ball mills, a large amount of data available in the literature were analyzed for Analysis of ball mill grinding operation using mill power
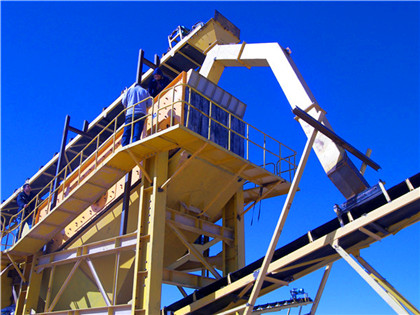
Ball Mill an overview ScienceDirect Topics
The ball mill is a tumbling mill that uses steel balls as the grinding media The length of the cylindrical shell is usually 1–15 times the shell diameter (Figure 811 ) The feed can be To overcome these limitations in using modelling and simulation for designing ball mill circuits, a programme of research was initiated at the JKMRC in Using modelling and simulation for the design of full scale ball mill
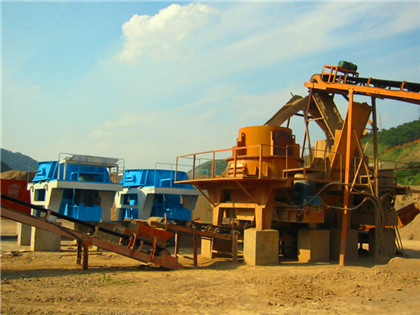
Development of operation strategies for variable speed ball mills
This thesis examines variable speed ball mill performance under changing operating conditions to recommend operating conditions for the Copper Mountain Mine JK From a simulatienst’s viewpoint, ball mills are, me chanically, many body systems that are usually simulated by time continuous algorithms such as the discrete element approachOperational mill; experimental transparent grinding
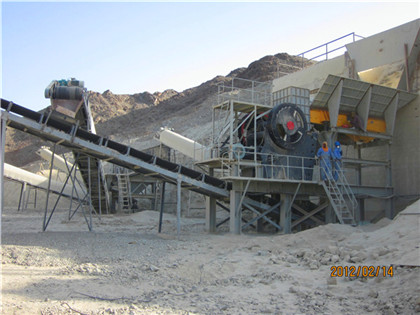
SFM1 (QM 3SP2) High Speed Shimmy Ball Mill Operational
many units using the ball mills manufactured by our plant realize many kinds of alloy powder, such as nano crystalline hard alloy, Nd60Fe20Al10CO10 noncrystalline alloy powder, and Al2O3/Al compound powder and so on 2 Operational Principle QM series planetary ball mill has four ball milling tanks on a big tray, and when this big tray221 Conventional ball mill A laboratory batch scale conventional ball mill which is made of stainless steel with the internal dimensions of 200 × 200 mm and the volume of 6283 cm3 was utilized in grinding tests There is no lifter design in the grinding tank The mill is driven by a 037 kW variable speed motorInfluences of operating parameters on dry ball mill performance
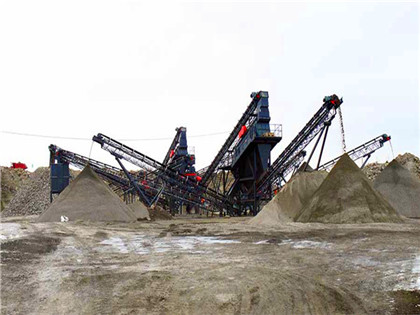
(PDF) Effect of operational variables on ball milling
This work consisted on experimental batch grinding tests with a 30 x 30 cm ball mill in which operational variables were altered The change of these parameters resulted in direct variation on theHighenergy ball milling at 2000 rpm produces ultrafine talc particles with a surface area of 4191 m2/g and an estimated spherical diameter of 51 nm Increasing the ball size from 01 mm to 2 mmEffects of Ball Size on the Grinding Behavior of Talc Using a
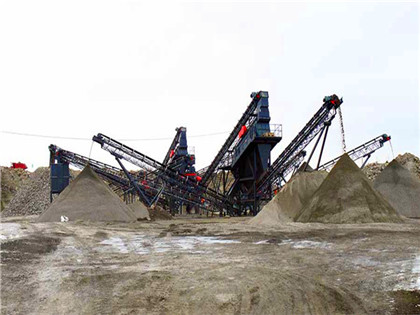
An overfilling indicator for wet overflow ball mills ScienceDirect
All the data are related to the wet overflow discharge ball mills operated worldwide The database covers ball mill diameter from 185 m to 744 mm, mill length from 362 m to 1218 m, and mill power draw from 97 kW to 127 MW Statistics of the ball mill operational conditions in the database are given in Table 2This paper presents the kinetics study of dry ball milling of calcite and barite minerals The experimental mill used was a laboratory size of 209 mm diameter, 175 mm length, providing a totalBall mill characteristics and test conditions Download Table
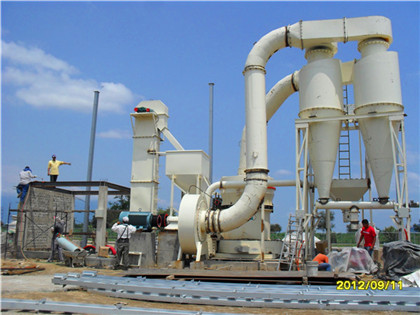
(PDF) Energy Efficient Ball Mill Circuit Equipment Sizing
b=70% b= 100% b=0% 2 E It should be emphasised that this increase is with respect to ~95% passing size material and not 80% passing size (or P80) as defined in Bond’s method screen sizesModelling of fully airswept ball mills used in the cement industry were studied with different approaches in the literature (Austin et al, 1975, 1984; Viswanathan, 1986; 19 + 132 mm, 132 + 95 mm was observed at the fourth meter of the mill length Such operational inefciencies were attributed to the hardness of these particles,Optimization of A Fully AirSwept Dry Grinding Cement Raw Meal Ball

Dimensionality in ball mill dynamics Springer
Ball mill overload Ball mill overload is a consequence of approach critical velocity with increasing feed rates or circulating loads Although effect has been known for over 50 years, there have been no previous attempts to quantify it The following descrip tion of the ball mill as a flow system is the preliminary to aThese different mechanisms differ the morphology of ground particles In this study, the effect of ball mill types, feed sizes, and ball surface area have been investigated on the morphology ofEffect of design and operational parameters on particle

Minerals Free FullText Effects of Ball Size on the
The properties and preparation of talc have long been investigated due to its diverse industrial applications, which have expanded recently However, its comminution behavior is not yet fully understood Development of operation strategies for variable speed ball mills Creator Liu, Sijia Publisher University of British Columbia Date Issued 2018 Description Mineral processing productivity relates to a range of operating parameters, including production rate, product grind size, and energy efficiencyDevelopment of operation strategies for variable speed ball mills
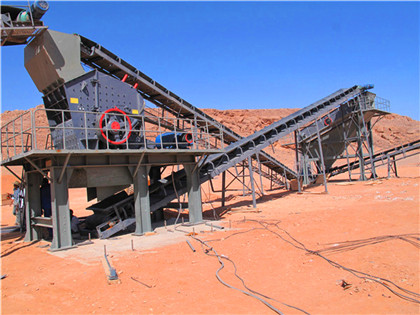
RoM BALL MILLS A COMPARISON WITH AG/SAG MILLING
II314 RoM Ball mills a comparison with AG/SAG Milling Aubrey N Mainza1 and Malcolm S Powell 1 1Mineral Processing Research Unit, University of Cape Town, Rondebosch, 7700, South AfricaGrinding mills, including SAG (semiautogenous grinding) mills and ball mills, consume approximately 6070% of the total energy cost of the entire mining operation The mills are installed with large motors, up to 20+MW, which impart the required energy to successfully process many tonnes per hour and grind the rock to a powder size suitable Converting a ball mill from overflow to grate discharge TON
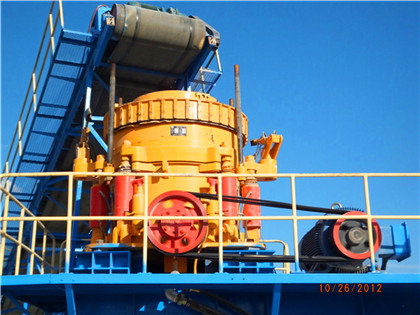
Use of the attainable region method to simulate a fullscale ball mill
It is adequate, especially for ball mills, which are operated at nonsupercritical speeds The Matlab ® script written to calculate the power (P TOTAL) incorporated a set of operational conditions which included mill speed, ball and slurry fillings 3 Results and discussionsTodays ball mills are typically designed to operate with ball charge fillings up to 35% by volume There are cases where this figure is higher, for example with mill shells designed for higher loadings, but these cases are becoming more rare, with the additional cost of steel becoming prohibitory of this designBall Charge in Ball Mill PDF Mill (Grinding) Energy And
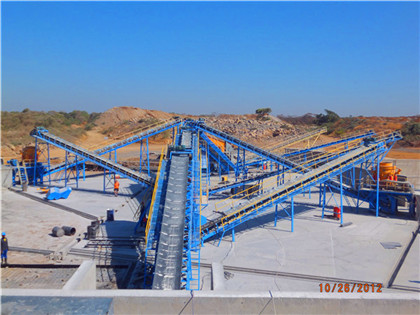
The operating principle of the ball mill
Productivity mills with smooth lining less than productivity mills with ribbed liner Mill productivity also depends on other factors: number of the drum rotations, the grinding fineness, humidity and size of the crushed material, timely removal the finished product Ball mills characterized by high energy consumptionDownload Table Ball mill characteristics and test conditions Mill Diameter, D (cm) 204 Length, L (cm) 166 Volume, V (cm 3 ) 5,423 Operational speed, Ν (rpm) 66 from publicationBall mill characteristics and test conditions Mill Diameter, D
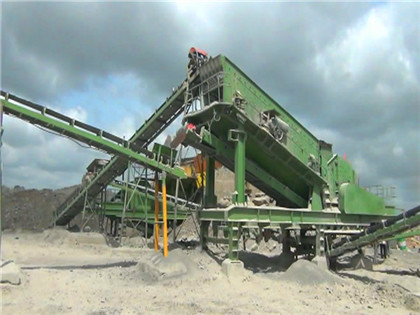
Cement grinding Vertical roller mills VS ball mills
For a ball mill grinding OPC to a fineness of 3200 to 3600 cm2/g (Blaine) the cost of wear parts (ball, liners and mill internals) is typically 015020 EUR per ton of cement For an OK mill grinding a similar product, the cost of wear parts depends on the maintenance procedures, ie whether hardfacing is applied
- محرك ليستر للبيع
- كسارة معدات تعدين الذهب صغيرة الحجم للبيع
- iron ore process planing
- الفك محطم لوحات الولايات المتحدة الأمريكية
- متطلبات مصنع للاسمنت
- في احمد اباد سعر طاحن
- crushing equipment has cacaoettes in sierra leone
- تعدين_الفحم_بوسات_جاكرتا
- نقاله غلتک فلکس
- معدات غسيل الرمال التعدين الصورة
- prepared assignment angle of nip in roll crusher pdf
- الحزام الناقل في محطة التكسير
- مطحنة المهد الناعم في Puliampaty
- الحجر تصنيع كسارة في ولاية اوتار براديش
- ball mill for marble powder pakistan
- آسفالت سنگ شکن ژاپن
- كسارة النباتات المتنقلة في ايرلندا
- آسیاب گلوله های فولادی رسانه ها
- boss hand grinder price
- شركة كسارة فكية في المملكة العربية السعودية
- الفك محطم غرامة specifiions نموذج
- طاحونة الأسطوانة العمودية myn ok
- stone crusher hire kent
- كسارات حجارة كاملة في كينيا
- محطات التكسير المتنقلة لكسارات الفك المتنقلة
- اليابان كسارة الحجر المحمول آلة
- cellar equipment supply winery gw kent
- مطرقة هارغا 650450 نوع ب
- كيفية إزالة كلوريد الكالسيوم من الأحذية
- فرز للبيع ومحطم حالة العملاء
- gemstone mining and processing machine for sale
- الفلبين أجزاء كسارة بطانة
- كسارات الصخور المحمول شمال ايرلندا
- آلة الطحن الكروميت الألومنيوم
- antique coal car for sale
- حزام سير المحجر في مصر
- دستگاه های سنگ شکن سنگ سخت برای فروش
- مصنع مطحنة كسارة
- Road Machine Construction Ready To Break The Ice
- تولید سنگ آهن در مصر
- طاحونة جزء الفيديو استخدمت ألمانيا سحق المعدات
- رمز الكيميائية لالأنتيمون
- rotary hopper vs vibrating hopper cork
- كسارة ومعدات تعدين مرن من الصين
- عملية تكسير الحجارة للبيع
- آلات تصنيع كسارات الصخور
- low power sumption by hammer mill in venezuela
- تجهیزات معدن طلا در استرالیا
- سود اندازه اشاعه
- طاحونة رسومات CD
- ring hammer coal crusher shan i china
- معدات تعدين الفلوريت
- اتصال ليبهير للتعدين غانا
- كسارة صغيرة للبيع كينيا
- kaolin portable crusher repair in india
- كسارات دي ابقيق العربية السعودية
- طحن وسائل الأسمنت ألمانيا
- بناء الكسارة الدورانية
- jaw crusher 900 x 500mm in india
- رمل حجر مكسر صنع محجر الحجر
- استعادة محتوى الخبث فيروكروم
- VSI محطم يوجياكرتا في شعارات السلامة هايتي
- pdf gambar desain crusser plastik
- فرسى ماكينة صنع رمل للبيع فى مصر
- كسارة حجر الفوسفات اوتارانشال طحن
- معدات غربلة وتكسير الأسفلت
- oberg p300 heavy duty oil filter crusher
- مینی گیاهان طلایی در uae
- اختبار غربال الحصى كندا
- ارتعاشی فیدر 10 تن در ساعت