
grate discharge minerals
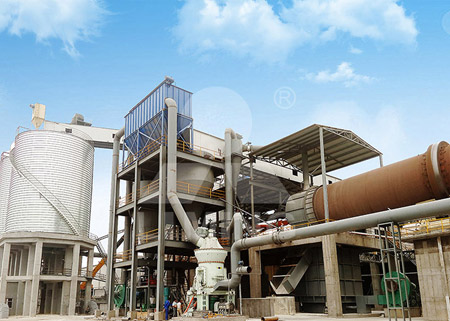
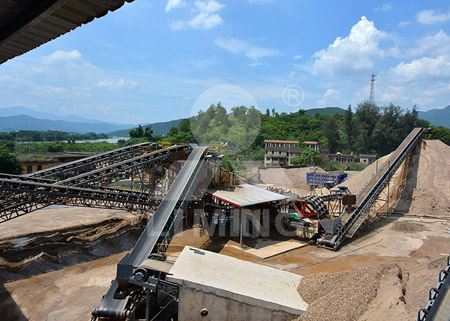
grate discharge minerals

Slurry flow in mills: grateonly discharge mechanism (Part1)
Abstract Discharge grates play an important role in determining the performance of autogenous, semiautogenous and grate discharge ball mills The flow capacity (grinding capacity) of these mills is strongly influenced by the discharge grate Abstract Discharge grates play an important role in determining the performance of autogenous, semiautogenous and grate discharge ball mills The flow Slurry flow in mills: grateonly discharge mechanism (Part1)
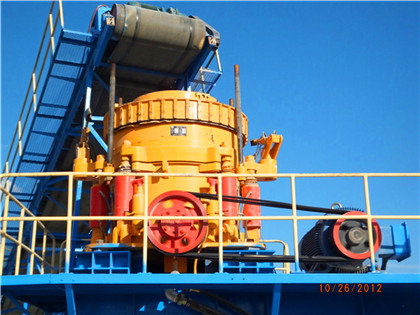
The effect of grate design on the behaviour of gratedischarge
Discharge grates play an important role in determining the performance of autogenous, semiautogenous and grate discharge ball mills The flow capacity The slurry transportation in AG/SAG mills is a twostage process consisting of flow through the grate and the discharge of slurry by pulp lifters into the discharge Slurry flow in mills: gratepulp lifter discharge systems (Part 2)
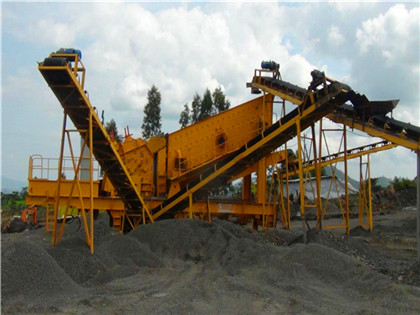
Slurry flow in mills: gratepulp lifter discharge systems
1 Introduction In the first of this twopart series of papers the flow characteristics of a grateonly laboratory mill was reported However, in industry, The discharge grates of the SAG mill were identified as a key component in the SABC circuit, and their design is a crucial factor in the mill’s performance [17,18,19,20,21] The initial design of the grate Minerals Free FullText Optimizing Performance of
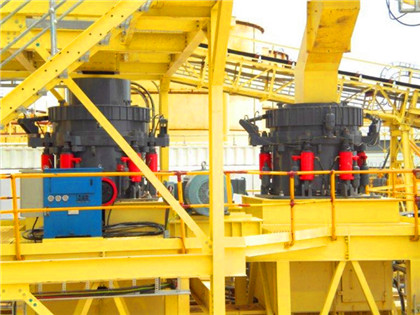
Slurry discharge capacity of autogenous and semi ScienceDirect
International Journal of Mineral Processing Volume 46, Issues 1–2, April 1996, Pages 5372 Research paper Slurry discharge capacity of autogenous and semi Ideally, the discharge rate through a gratepulp lifter assembly should be equal to the discharge rate through at a given mill holdup However, the results Slurry flow in mills: Gratepulp lifter discharge systems (Part 2)
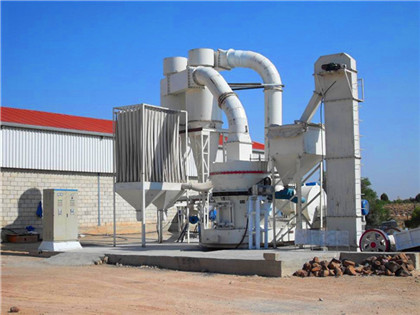
Slurry flow in mills: grateonly discharge mechanism (Part1)
Slurry discharge capacity of autogenous and semiautogenous mills and the effect of grate design S Morrell, I Stephenson@article{Latchireddi2003SlurryFI, title={Slurry flow in mills: gratepulp lifter discharge systems (Part 2)}, author={Sanjeeva Latchireddi and Stephen Morrell}, journal={Minerals Slurry flow in mills: gratepulp lifter discharge systems (Part 2

(PDF) Slurry flow in mills: Grateonly discharge
Abstract Discharge grates play an important role in determining the performance of autogenous, semiautogenous and grate discharge ball mills The flow capacity (grinding capacity) of these millsMineral processing includes various processes and unit operations that involve particle flow, Hardinge mill has previously been reported by Morrison and Cleary (2004, 2008) and Cleary (2004, 2019) Slurry flow and grate discharge has also been investigated by Cleary and Morrison (2012) More recently, Cleary et al (2018a,Prediction of 3D slurry flow within the grinding chamber and discharge
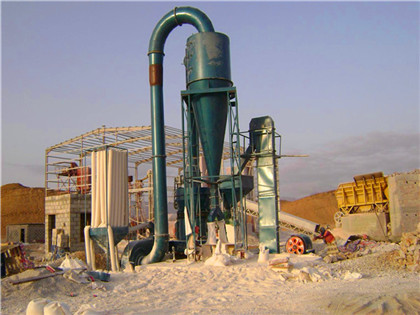
Slurry flow in mills: gratepulp lifter discharge systems (Part 2)
Influence of open area on discharge rate through the grateonly and gratepulp lifters with medium size radial pulp lifter (MRPL): (a) grateonly discharge and (b) gratepulp lifter discharge However, with the pulp lifters fitted, the discharge rate was found to marginally decrease up to 705% open area and then remained constant with Objectives At the end of this lesson students should be able to: Explain the grinding process Distinguish between crushing and grinding Compare and contrast different type of equipment and their components used for grinding Identify key variables for process control Design features of grinding equipment (SAG, BALL and ROD MILLS)AMIT 135: Lesson 6 Grinding Circuit Mining Mill Operator

CHAPTER 11
Mineral Comminution Circuits Their operation and optimisation, JKMRC Monograph Series Mining Stromayr, S,1994, Capacity limitations of pan lifter in grate discharge mills, BE(HonsGrate Discharge Ball Mills have shown 25% to 45% more tonnage ground and a substantial reduction in power consumed per ton of material compared size for size with overflow mills To illustrate the characteristics of various type mills we have shown the types of discharge for rod mills and ball mills There are essentially four types of rod millOverflow VS Grate Discharge Ball or Mill Why Retrofit 911
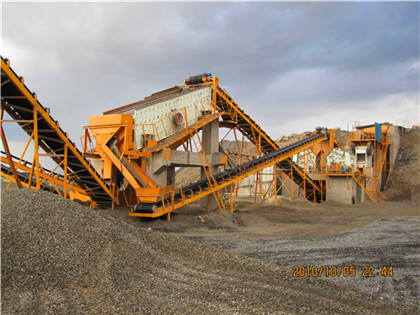
Peripheral Discharge Ball Mills Theory and Practice 911
Peripheral Discharge Ball Mills The several layers of balls lying on top of those next to the shell follow a similar cycle except that, due to relative difference in the two forces, their paths become more nearly vertical The outer layers, spreading more than the inner layers, increase the area in the zone of the falling ballsMill Type Overview Three types of mill design are common The Overflow Discharge mill is best suited for fine grinding to 75 106 microns; The Diaphram or Grate Discharge mill keeps coarse particles within the mill for additional grinding and typically used for grinds to 150 250 microns; The CenterPeriphery Discharge mill has feed reporting from both AMIT 135: Lesson 7 Ball Mills & Circuits Mining Mill Operator

The Martin moving grate technology SpringerLink
The thermal treatment of waste using gratebased systems has gained global acceptance as the preferred method for sustainable management of residual waste This is because the energy content of the waste is utilized and quality products and residues are produced Modern WastetoEnergy (WtE) plants are extremely complex Sound Pulp lifters are used to transport slurry from the feed to the discharge end through grate holes in the mill At the discharge end of the mill, based on the requirement, different types of lifter International Journal of Mineral Processing, 46 (1–2) (1996), pp 5372, 101016/03017516(95)000607 View PDF View article View inA comparative study on a newly designed ball mill and the
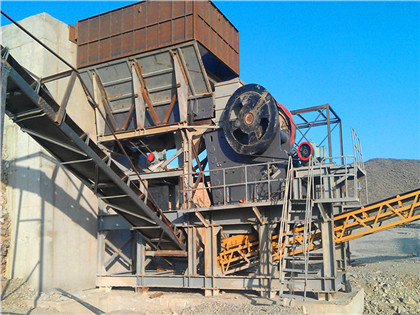
The effect of grate design on the behaviour of gratedischarge
International Journal of Mineral Processing, 18 (1986) 85105 85 Elsevier Science Publishers BV, Amsterdam Printed in The Netherlands THE EFFECT OF GRATE DESIGN ON THE BEHAVIOUR OF GRATEDISCHARGE GRINDING MILLS MH MOYS Department of Chemical Engineering, University of the Witwatersrand, 1 Jan Solids refer to all ore small enough to discharge through the enddischarge grate, and grinding media refers to the rocks and steel balls Minerals Engineering, Volume 128, 2018, pp 115122 Sandile Nkwanyana, Brian Loveday Preconcentration of copper ores by high voltage pulsesSlurry discharge capacity of autogenous and semi ScienceDirect

Semiautogenous grinding (SAG) mill liner design and development
SAG mill liner development draws primarily on practical experience from SAG milling operations supported by computerbased modeling of charge motion in SAG mills and on established good design practice Liner design needs to respond to the process aspects of mill liner action that are critical to good SAG mill performance, ie, the impact Trelleborg has been providing mill lining systems since 1920 The focus is on working with our customers to provide incremental improvement to enhance mill availability, increasing efficiency and reducing energy consumption Full lining kits are designed and supplied including Lifter bars, shell plates, pulp lifters, fasteners and discharge gratesMill Lining Systems FluidHandling Trelleborg
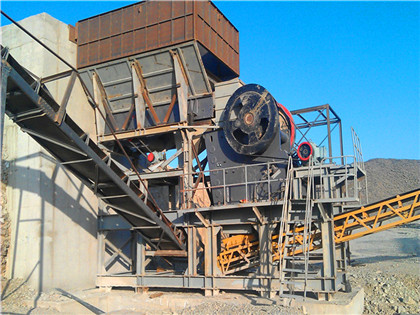
Grate Discharge Advantage & Benefits 911 Metallurgist
In simple words, grate discharge mills give higher tonnage, but produce coarser grinding, that may cause problem in your Flotation recovery, Grate discharge will also reduce your EGL The best option would be to place a retainer ring at discharge end to hold more charge & that will give you more throughputs without compromising grind sizeGrate discharge mills are used when the grinding energy shall be concentrated to the coarse particles without production of slimes A crushed mineral whose largest particles pass a screen with 25 x 25 mm apertures shall be ground to approx 95% passing 01 mm in a 29 x 32 m ball mill of 35 ton charge weightGrinding Mill Design & Ball Mill Manufacturer 911 Metallurgist
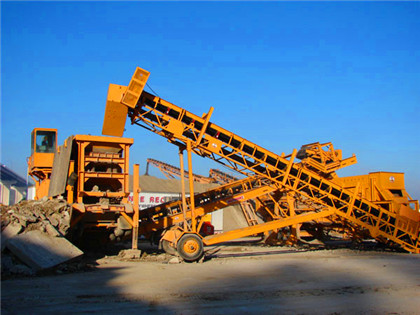
GRATEPULP LIFTER DISCHARGE SYSTEMS (Part 2) SMC Testing
Julius Kruttschnitt Mineral Research Centre, University of Queensland Isles Rd, Indooroopilly 4068, Australia (AG), semiautogenous (SAG) and grate discharge ball mills The performance of the pulp lifters in conjunction with grate design determines the ultimate flow capacity of these millsThe grate discharge rod mill reduces overgrinding and s of the lead minerals The rod mill discharge passes over a Mineral Jig and to a Spiral Classifier Most oxides and carbonates are easily broken down in any type of grinding unit and care should thus be given to the removal of the freed mineral as quickly as possible The mineral jigOxide Lead Treatment & Extraction by Flotation & Gravity
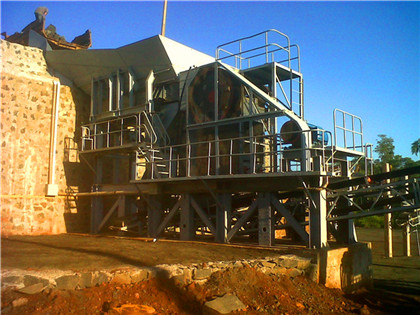
Ball Mills 911 Metallurgist
Grate Discharge mills will not face this issue C) This value represents the Volumetric Fractional Filling of the Voids in between the balls by the retained slurry in the mill charge As defined, this value should never exceed 100%, but in some cases particularly in Grate Discharge Mills it could be lower than 100%Highlights Oneway coupled SPH–DEM models can predict the flow of solids and fluid charge in SAG mills End walls and worn shell liners create significant axial flow and recirculation in a SAG mill charge Slurry flow through the grate and along the pulp lifters and discharge from the mill can be predicted End wall lifters are critical to grate Prediction of 3D slurry flow within the grinding chamber and discharge
- تدقيقات الطاقة في محطات التكسير
- مطحنة خام الذهب للبيع في دبي العرض
- concrete vibrator rental philippines
- تولید کنندگان گرد و غبار صنعتی بنگالور
- المحاكاة العددية تدفق مرحلتين من التعويم العمود
- مصنعي مطاحن الرمل مصر
- used complete grinding unit for grinding minerals
- معدات التعدين في نيروبي
- مكونات هيدروليكية لوحدات كسارة قائمة الموردين
- خريطة مصنع الاسمنت للجزائر
- crusher manufacturer granite
- تكلفة خط إنتاج الصخور المكسرة في الهند
- كسارة فكية صغيرة متنقلة عالية الطاقة
- ورقة عملية تكسير الحجارة مصنع
- magnetite iron ore processing jaw crusher
- مصنع غسيل الذهب الصغير في زامبيا
- الرصاص والزنك المورد كسارة مخروط خام
- كسارة الفك dingsheng
- jaw crusher made in pakistan
- كسارات الحجارة في ولاية غوجارات
- المطاحن أو المطاحن الجزء الأكبر من الطحن الدقيق في
- خط تكسير خام الحديد
- Prices Of Posho Mill Motors
- كسارة الفك pe 600x900
- مصنع تركيز اليمن
- ماشین سنگ زنی 2 میکرون برای کربنات کلسیم
- placer gold processing line placer gold flotation machine
- تاريخ آلة سحق الحجارة
- محطات غسيل الكروم جنوب أفريقيا
- کارخانه های تولید فولاد توپ برای فروش
- eagle 1000 ore gold mining machine for sale
- تجار كسارة فينا
- خطة عمل لغسالة الرمل
- مورد حجارة وغسيل رمل في السعودية
- used small scale gold mining equipment and extraction plant price
- مصنع للاسمنت والمعدات والاسمنت مما يجعل النبات
- الذهب سحق طريقة الجاذبية تهزهز نوع
- معدن فرایند آزبست
- mobile crome refining and processing plants
- سعر آلة النحاس باليمن
- ضعف بكرة الطين مطحنة
- ملموسة سحق الآلات المتعاملين في مصر
- crawler type tracked mobile crusher
- الحجر سعر كسارة صغيرة
- طريقة تشغيل الغسالة توشيبا كيلو
- كسارة Ponsel Skala Kecil Untuk Pabrik
- magnetic seperation in iraq
- أفضل معدات سحق مطحنة Xogze
- فراشة الأزرق حجر الغرانيت
- آلة تكسير الرمال ذروة
- stone and marble cuting machine
- طحن بالموجات فوق الصوتية
- مطحنة الأسمنت promak
- كسارة متنقلة بو تهود
- how to extract gold from cell phones
- الذهب ختم سعر مطحنة محطم خام الذهب
- عينة خط مواصفات كسارة الفك
- جوجل زجاجة محطم محطم زجاجة في جوهانسبرغ
- d14 producers sand aggregate 2009
- تدور مطرقة كسارات الصخور
- حلقة النار كسارة مخروطية للبيع
- مطاحن الفجوة الطويلة ميكرون الهند
- price of cement grinding ball
- کنسانتره گیاهان طلا
- الحجر المحمولة معدات كسارة كسارة حجر
- مصنع إنتاج الرمل الكلي آلة صنع كسارة الحجر الصغيرة
- gold dry wash design
- أجزاء آلة محطم الفحم
- مصنع فصل الذهب على نطاق صغير
- تستخدم مخروط كسارة مخروط الحجر الجيري الهند