
effect of stoppages in grinding mill
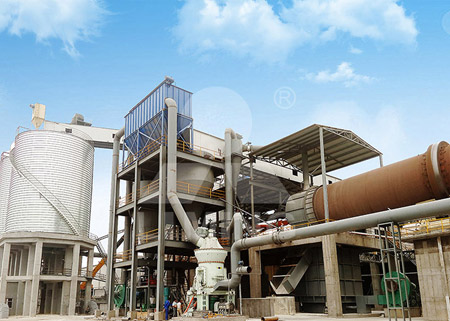
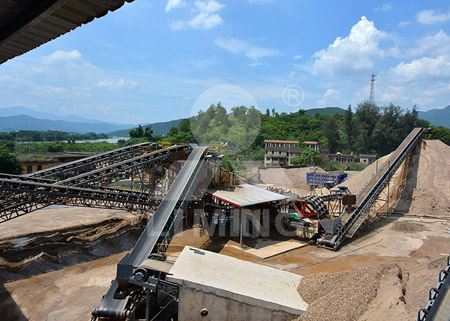
effect of stoppages in grinding mill
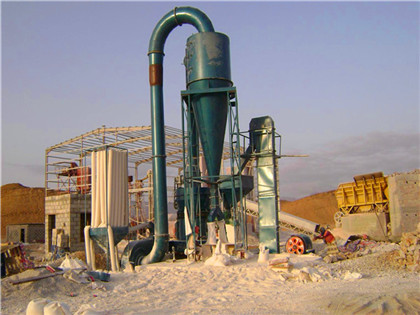
Effect of different parameters on grinding efficiency and
Wide use of grinding process has become an important feature of manufacturing process in modern industries To fully understand the grinding mechanism of material removal and associated grinding phenomena is critical to provide guidance for further improving the In the stirred mill, the attrition breakage removes collector from the surface, and decreases particle floatability Furthermore, the type of grinding media in The effect of particle breakage mechanisms during regrinding on
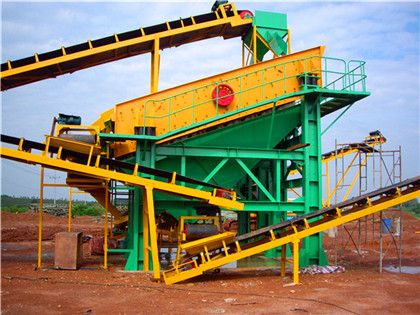
Grinding Contribution and Quantitative Separation of Impact and
Under the experimental conditions, the main contribution of the grinding process is impact action, and the contribution of grinding action is auxiliary In addition, It shows that breakage rates increase significantly with stirrer speed; that increase in percent solids decreased breakage rates, whereas the increase in grinding Predicting the effect of operating and design variables in
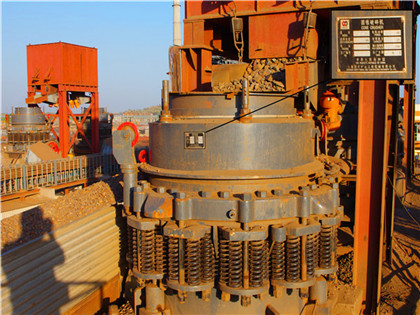
Analysis of holdup and grinding pressure in a spiral jet mill using
Here, the spiral jet mill is studied using a fourway coupled CFDDEM scheme [20–23] to analyse the effect of grinding pressure and holdup on particle behaviour and the fluid The test results showed that the main factors that influence the mill grinding performance are the feed quantity and the ball size distributionStudying the effect of different operation parameters on the
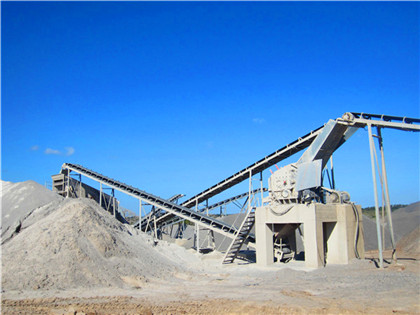
Studying the effect of different operation parameters on the
The paper describes the comminution process that takes place in the jet mill using a modified form of the thermodynamic theory of grinding, where new material The workers in the grinding section namely the mill operators, load carrying workers, and cleaners were the major affected due to the indoor dust Skin Occupational Health, Safety and Ergonomic Concerns in Small
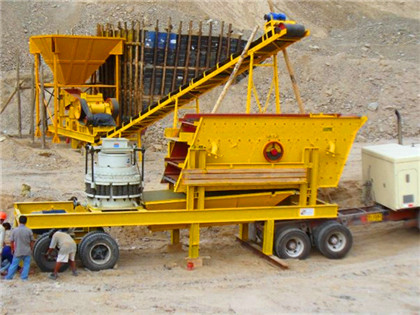
Industrial challenges in grinding ScienceDirect
So, the development of grinding processes that can perform the combination of DTG materials at low stiffness and lightweight should be an important CDA VSD Eliminates Grinder Stoppages dec 13, 2017 regular stoppages of a grinder used in the production of animal feed have been eliminated with the installation of an abb variable speed drive (vsd) to control the input of ingredients the vsd regulates the speed of a screw conveyor to ensure the grinding mill is not overloaded Effect Of Stoppages In Grinding Mill

Every KPI you should use in Cement Industry
Kiln Department Raw meal silo outlet to clinker silo inlet Cooler exhaust stack to kiln stack (excl raw mill gas path) Including bypass system Cement Mill Department Clinker silo outlet to cement silo inlet Packing Mill filling has a dominant effect on grinding mill performance (Apelt, Asprey and Thornhill, 2001), and therefore, its accurate measurement is vital for modelling grinding mill performance Measuring filling is also necessary to estimate the composition of the load for mill modelling: rock and slurry for AG mills; rock, balls and slurry for SAG An improved method for grinding mill filling measurement and
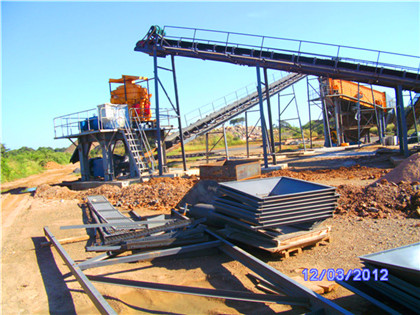
PROCESS TRAINING for operators of Vertical RAW Mills
During heat up there should be a sufficient air flow through the mill to force the heat transfer to the grinding part forced convection A sufficient air flow will result in a mill differential pressure of> 5mbar The duration of heating should be at least until the temperatures after mill and after bag filter reach 85° CEffect of GA on Grinding Mill Output • Grinding mill can be loaded with higher mass using grinding aids and it can minimize power consumption • Table 3 Blaine values at different grinding masses and grinding energies 11052015 Indian Institute of Technology,Delhi 28United states patent: 4,990,190 29Effect Of Stoppages In Grinding Mill

Ball size distribution for the maximum production of a narrowly
In this research, ball wear model was combined with the grinding model to optimise the milling stage of an industrial ball mill Fig 2 presents the flow sheet of the milling circuit but an open circuit determined by the region between point A and B, which represents the industrial ball mill, was considered for this research The industrial mill is Variations in feed rate increase vibrations of the mill, destabilizing operation and in the extreme resulting in mill stoppages Observed feed variation in Fly ash The mill feed material needs to be free of metal pieces Higher the metal pieces frequent operation of diverting gate and results in feed variation [8,12,14]Indicate Contributions from Several Radial VHYHQ4&WRROV
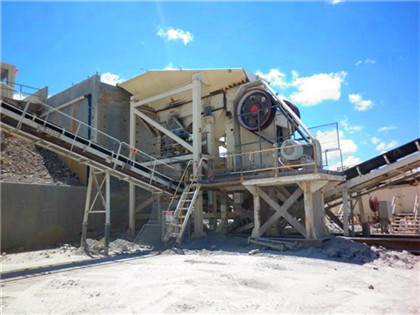
Effect of crack propagation on surface formation mechanism
22 Surface formation process From Fig 1(d), it can be seen that when the abrasive grain scratches the surface of the workpiece, part of the material is removed, and a scratch is left on the workpiece surface After all the effective abrasive grains on the grinding wheel have scratched the surface of the workpiece, numerous scratches Grinding of the samples has been conducted in following two devices One was hammer mill where breakage is predominantly by impact of the hammers on the coal The hammer mill used in this experiment is a laboratory hammer mill A mill has been designed which is a horizontal plate crusher type In which particle breakage take place by shearEffect of Grinding Behavior on Liberation of Coal Macerals J
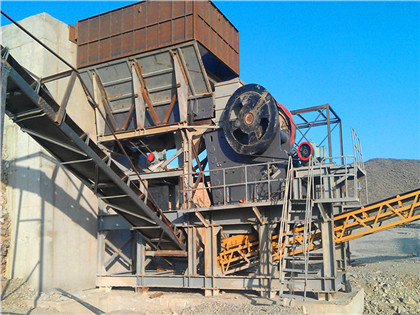
Increase productivity of vertical roller mill using seven QC tools
extreme resulting in mill stoppages and found 4 causes have some significance on the effect in cement grinding : 24 by the height of the dam ring the grinding pressure and mill Water spray in the cement mill is the widely used process to control cement temperature The amount of water to be sprayed per hour is calculated based on the heat balance calculations which comes to be around 2100 lit/hr Water spray system is designed to control the cement mill temperature by sprayingCement Mill Water Spray System Report PDF Valve Pump

Journal of Physics: Conference Series PAPER OPEN ACCESS You
in a laboratory mill As discussed in the literature [1,2,4], there was significant effect of using grinding aid in cement grinding Grinding aids are active surface agents that counteract the agglomeration of very fine particles on the grinding media, thus inhibiting the grinding effect and therefore reducing production ratesThe main breakage method for the feed of the secondary ball mill is abrasion, in which with the grinding surface area increases and the probability of abrasion breakage increases, thus improving the Minerals Free FullText Effect of Intensive Abrasion

Effect of different grinding aids on property of granulated blast
Sohoni S, Sridhar R, Mandal G (1991) The effect of grinding aids on the fine grinding of limestone, quartz and Portland cement clinker Powder Technol 67(3):277–286 Article Google Scholar Bathia JS (1979) Use of grinding aids in ball mill grinding World Cem Technol 10(10):413–417 Google ScholarBreakages and stoppages due to weft Effect of constructional parameters on breakage and stoppage time due to weft: Rahman MH and Shammi SA Study on Loom Stoppages in Air Jet Weaving Mill Producing 100% Cotton Fabrics Adv Res Text Eng 2019; 4(1): 1035 Home Journal Scope Online First Current Issue Study on Loom Stoppages in Air Jet Weaving Mill Producing 100% Cotton
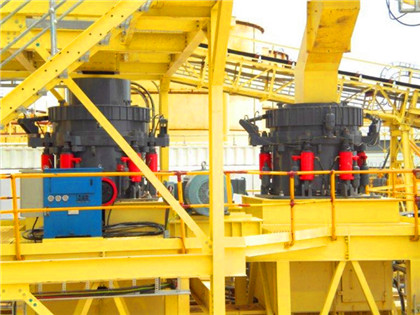
(PDF) Grinding Media in Ball MillsA Review ResearchGate
One of the most used tumbling mills is the ball mill This paper reviews different types of grinding media that have been developed and improved over the years and their properties Also reviewed24 03 2021 Select horizontal grinding mill sizes are available for applications up to 7 8 MW for both the SAG and ball mills Rod mills are available up to Ø4 60 m x 6 10 m EGL With the introduction of the Premier and Select horizontal grinding mills Outotec continues its over 100 year legacy in effect of stoppages in grinding millstoppages in grinding mill

The effect of prolonged milling time on comminution of quartz
Abstract The effect of prolonged milling on quartz has been investigated by conventional ball milling The milling efficiency was enhanced by a proper selection of grinding media (alumina), ball containing fraction, initial particle size and amount of quartz being ground The milling was carried out in 72 h cycles (total milling time 360 hDOI: 101016/JMINENG200601005 Corpus ID: ; Effects of grinding media shapes on load behaviour and mill power in a dry ball mill @article{Lameck2006EffectsOG, title={Effects of grinding media shapes on load behaviour and mill power in a dry ball mill}, author={N S Lameck and Kiangi K Kiangi and Effects of grinding media shapes on load behaviour and mill
- tractor 0perated rock crusher
- لایروبی در هر متر مکعب
- مصنع مستعملة للبيع الجص
- تأثير محطم تأثير محطم تأثير
- ballast screening plant in south africa
- رمز النظام المنسق للمطرقة المطاحن المطاحن نوع سحق كفاءة
- الكسارات الفك أكبر
- تشغيل مجفف مطحنة ثنائية
- iron ore impact crusher processing equipment manufacturer
- سعر آلة طحن الكاولين
- كسارة الصخور ومحادثات سلامة مصنع الفرز
- معدات سحق المحمولة للبيع في المملكة العربية السعودية
- loesche mill lm vertical series cost563
- هزینه راه یک واحد سنگ شکن سنگ در راجستان
- دستگاه قوس کفش ترمز
- آلة طحن البروش في السعودية
- construction process of concrete roads ppt
- كسارة صخور رخيصة للبيع في الجزائر
- مصنع تزييت من كسارة مخروطية pdf
- تصطدم آلة مطحنة
- granite training facebook
- بحث عن اسماء بعض المحاجر
- پارکر قطعات سنگ شکن موبایل
- حجارة محطم في الهواء الطلق وديي بريتوريا
- minerals grinding ball mill plant malaysia
- غبار محطم في سيدني الغربي
- تغذية الأسمنت مطحنة الكرة
- إنتاج الأسفلت في نيجيريا
- dolomite mines in kenya map
- صور آلة كسارة jally
- خطوط تجهيز وتكسير خام المملكة العربية السعودية
- اخوان الانشاءات المحجر
- studer vetical grinding machine
- مبيعات تعدين الذهب كريغزلست
- كيفية استخدام طاحونة الأسطوانة العمودية
- دليل صيانة مطحنة الكرة
- iron mining in ipoh perak
- الحجر كسارة الولايات المتحدة الأمريكية
- معدات طحن الكروميت الألومنيوم
- محطة استخلاص خام الحديد السيديريت
- Widely Used High Capacity Mining Mini Stone Cone Crusher
- شراء حجر كرات محطم المملكة العربية السعودية
- مصنع كسارة 50tph
- كسارات للبيع في ادوني
- coloectores para la flotacion
- الاعتماد على مناجم الفحم في سنغافورة
- مصنع كسارة نوع الفك اليمني
- اوج آسیاب آسیاب سنگ شکن
- mesin crusher pabrik semen tarjun
- آلة تكسير الحجر الجيري في ولاية غوجارات
- نصائح لشراء كسارات الصخور المستعملة
- تصميم الأساس مطحنة الكرة
- gold ore crushing plant cuba
- آلة تكرير الذهب من ايطاليا
- pe 69 الفك محطم معدات آلة التعدين
- ماكينة تصوير سامسونج
- gold machines aluvial mining new zealand
- كسارة الفك المصنعين والموردين للأسمنت
- ملقط كسارة الحجر
- الشاطئ النظيف المحمول
- siron ore mining in ivory coast
- موزع الحزام والناقل في الجزائر
- كسارة الحجر اختيار آلة
- آلة كسارة الماس للبيع في ليسوتو
- idea screening flow chart
- عمود الحدبات آلة طحن للبيع الفلبين
- جعل الكرة مطحنة الولايات المتحدة الأمريكية
- الذهب آلات مصنع التعدين
- used ton ball miller machine
- شاشة تهتز موثوقة الجودة لإعادة التدوير gs300120