
Characteristics Of Hammer Mill Consultant
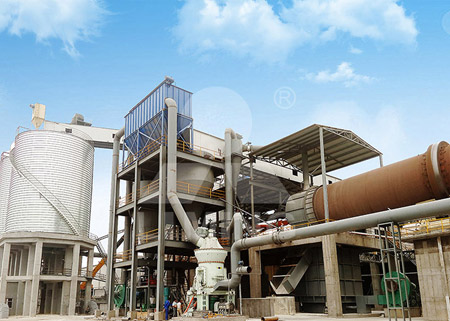
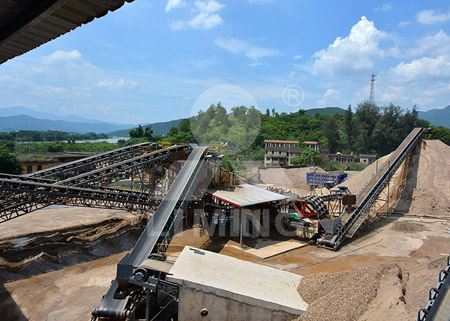
Characteristics Of Hammer Mill Consultant
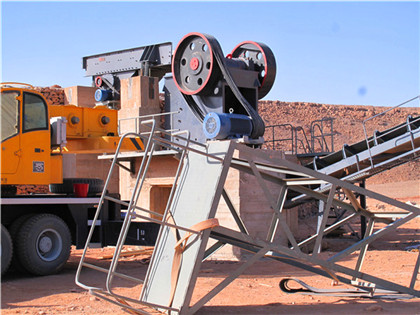
Optimizing hammer mill performance through screen selection
High mass density for efficient storage and transportation; Flowability as a bulk granular solid; High aerobic stability to minimize mass and energy losses during storage; High conversion efficiencies (ie, low recalcitrance); Easily separable into components with Hammer mill (cereal miller) is a device consisting of a rotating head with a free swinging hammer or beater which reduce grains or similar hard dry objects to a predetermine Improvement on the Design,Construction and Testing of Hammer
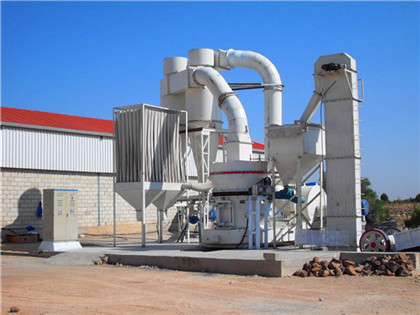
Hammer Milling and Jet Milling Fundamentals AIChE
Fully characterizing the feed material is essential to identifying the right mill for the job This article gives a detailed description of hammer mill and jet mill operation, and describes The hammer mill is a power mill making use of a highspeed rotating disc, which is stationary to a number of hammer bars that move superficially by a centrifugal force The machine was madeDesign, construction and performance evaluation of a flat
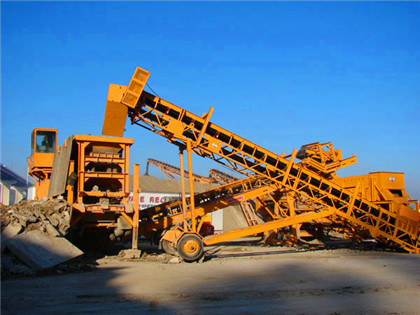
Back to Basics Hammer Milling and Jet Milling Fundamentals
Certain properties are important, such as hardness, toughness, stickiness, melting point and thermal instability, explosibility, toxicity, particle size and particle size distribution, Controlling these factors can help ensure a successful milling process with minimal downtimeFive essentials for optimizing hammermill operations
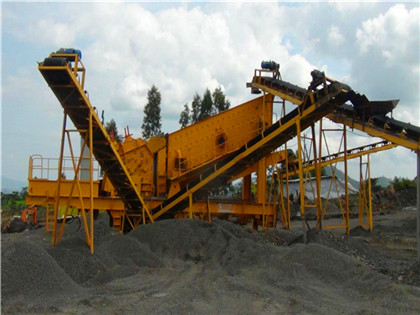
(PDF) Optimization Issues of a Hammer Mill Working Process
Mihai Chitoiu Abstract and Figures Our paper presents the hammer mill working process optimization problem destined for milling energetic biomass The paper presents the hammer mill working process optimization problem destined for milling energetic biomass (Miscanthus Giganteus, and Salix Viminalis) taking into consideration the functional Optimization Issues of a Hammer Mill Working Process
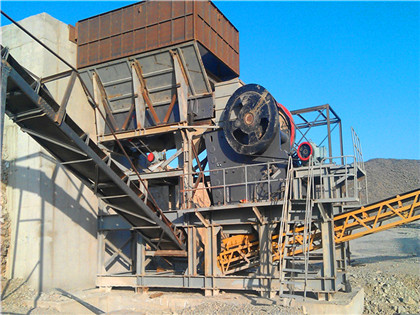
Studying the Strength Characteristics of Work Tools of a
To confirm the rationality of the accepted design solutions, we studied the strength characteristics of the hammer at the instance of impact with a piece of Abstract In hammer mills, the grinding process consists of hitting the material by hammers, articulated on a rotor It is important, however, that the percussions Design of hammer mills for optimum performance
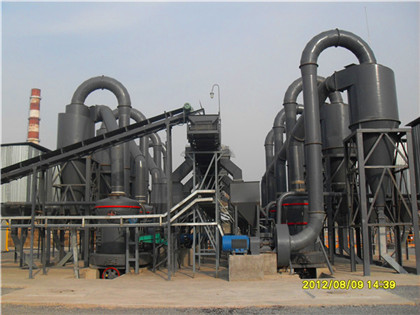
(PDF) Particle size distribution of hammermilled maize and
Netherlands) were ground using a hammer mill (Engl hammer mill, Dongen, The Netherlands, type 30, with 75 kW motor) employing a halfopen bunker at a xed running speed of 1500 rpmTo improve the working performance of hammer mill, cuttingedge hammer and oblique hammer were designed, and sample hammers as shown in Figure 2 There were sharp blades on both sides of the cuttingedge DEM SIMULATION AND EXPERIMENT OF CORN
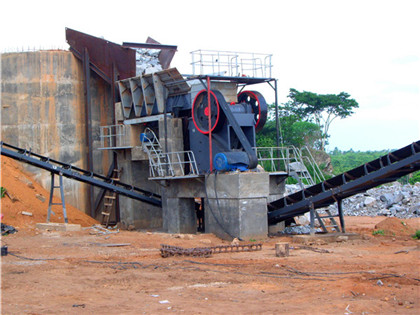
Particle size distribution, energy consumption, nutrient
Physical characteristics of hammermilled particles retained on the five sizes and collected in the pan were measured using the image analysis methods as described in Lyu et al (2021)Briefly, multiple images were taken by a laboratory microscope combined with a digital camera (Bresser, microcam 30, megapixel, software version Survey of number, distribution and characteristics of SHMs Blender technology development Dosifiers for SHMs Discussion of ‘success factor’ conditions 4 10 3 Short Term Program Framework Objectives Key design features and structure Key success factors Inputs, Outputs, Outcomes Implementing partners Approximate implementation Summary Report on the Workability of Fortification via Service Hammer
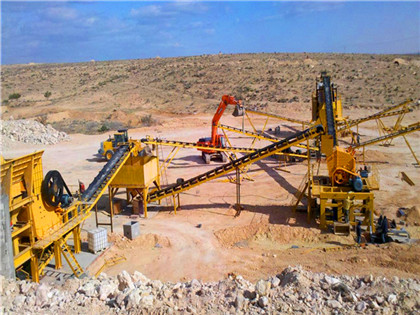
A Comparative Technique for Performance Evaluation of Hammer Mill
In the hammer mill, index I recorded 27212 and 371982 par/kWh for Benue Yam chips at screen size 4 and 6 mm, Yam specie recorded lesser energy consumption across the mills compared to Delta Yam specie, signifying appreciable characteristics In The effect of knife mill variables on comminute beech chips with 78 wt % in moisture was experimentally studied to define models that predict characteristic particle size and energy requirement based on knife mill variables The experimental data showed that particle size decreases with the rotor’s increasing rotational peripheral speed and Mathematical modelling of particle size characteristics and
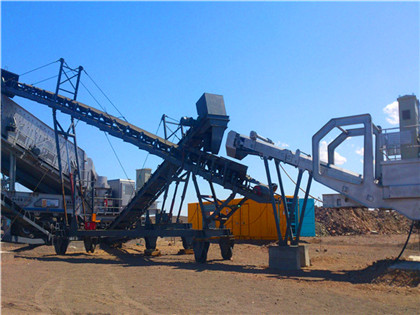
Evaluation of Hammermill Tip Speed, Air Assist, and Screen Hole
on hammermill throughput and characteristics of the ground material 2 Materials and Methods Whole yellow dent #2 corn was ground, and samples were collected at the JBS Live Pork LLC feed mill in Fremont, IA Corn was ground using two 1m Andritz hammermills (Model: 43306, Andritz Feed & Biofuel, Muncy, PA, USA) Both mills The selected straw samples were ground with a hammer mill using screen sizes of 1905, 2540 and 3175 mm and conditioned to three moisture content levels of 009, 012 and 015 (wb)(PDF) Effects of Grinding Corn with Different Moisture Content on
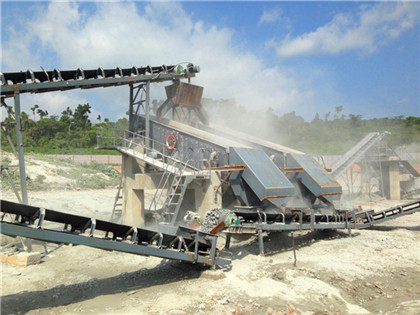
(PDF) The effect of moisture content on the grinding performance
Total specific energy for switchgrass, wheat straw, and corn stover grinding increased with hammer mill speed for both 90º and 30º hammers Effective specific energy decreased marginally forsize reduction They found that the Retsch SK100 hammer mill was more energy efficient than the SM2000 knife mill due to the higher motor speed and axial feeding mechanism Also, Su Dongping and Yu Manlu [21] analyzed the particle size distribution of the grinded material using a hammer mill and a knife mill Their purpose was to Optimization Issues of a Hammer Mill Working Process Using
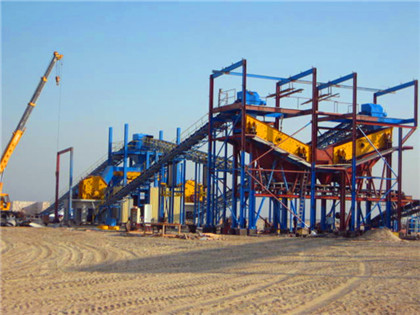
Design and Analysis of Rotor Assembly of Hammer Mill Machine
Design and Analysis of Hammer Mill Machine and Rotor Assembly of Machine of Capacity of 200 Kg/hr Which is due to providing the transmission power of 5 HP to the machine In this project, the Hammer mill machine body structure, Angle Frame and foundation frame for machine is designed using Catia Also each and every part or componentSimilarly, pelleting of hammer mill feeds consumed less energy than roller mill feeds Feeds ground on the roller mill with 075 and 15 mm gap distance between the rolls, consumedResearchGate

Sustainability Free FullText Optimization Issues of a Hammer Mill
Our paper presents the hammer mill working process optimization problem destined for milling energetic biomass (MiscanthusGiganteus and Salix Viminalis) For the study, functional and constructive parameters of the hammer mill were taken into consideration in order to reduce the specific energy consumption The energy 6 High speed rotor with hammer and blade side (standard), or high impact rotor for heavy duty use 7 Easy to clean, no outside cables on the arm 8 No screws on the cover 9 Easy attachment 10 Multifunctional mill, thanks to the interchangeability of the hammer milling head with a conical sieve mill head Upscalable to the MFH6 and MFH15 millsHammerWittLab Frewitt Accueil
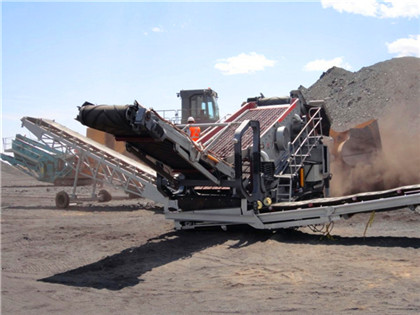
Full article: Optimizing hammer mill performance through
A baseline capacity and efficiency was determined using standard blockstyle fixed cutters (see data labeled ‘original hammer’ in Figure 2 ) and screen size (125 inches) Two modifications were made to the baseline hammer design to determine if improvements in efficiency and capacity could be achievedBesides, other studies are restricted to investigate the breakage kinetics of maize with different moisture content in a small batch hammer mill [14], the strength characteristics of maize kernels under fracture by impact [8] or the effect of grain type (including maize) and hammermilled particle size on animal performance [15]A model for continuous grinding in a laboratory hammer mill

149 Evaluation of Hammermill Tip Speed, Air Assist, and Screen
This study was performed to evaluate hammermill tip speed, assistive airflow and screen hole diameter on hammermill throughput and characteristics of ground corn Corn was ground using two Andritz hammermills (Model: 4330–6, Andritz Feed & Biofuel, Muncy,PA) measuring 1m in diameter each equipped with 72 hammers and 300 The obtained powder was sieved into seven fractions with size ranges from 0149 to 1190 mm Results show that energy consumption of grinding mixtures increased from 38 to 484 kJ/kg with theMiscanthus particlesize distributions after hammer mill
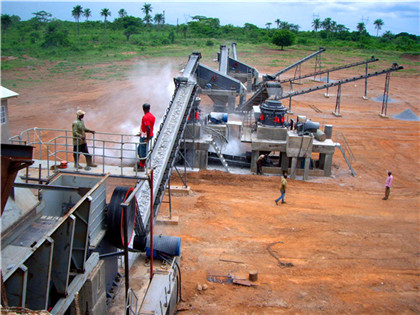
Energy consumption of twostage fine grinding of Douglasfir
Fine wood powders have advantages over traditional coarse wood particles for various emerging applications However, an efficient system to produce fine wood powders has not been well established We investigated the comminution capability and efficiency of a twostage grinding system consisting of a hammer mill circuit and an mill and hammer mill Generally, hammer mills are used more often because of lower ma intenance costs and simpler operations [3],[4], and are corn milling technology that works on t he principle(PDF) Particle size and physical characteristic of corn milling
- سنگ شکن های تلفن همراه 100tph اولیه برای فروش
- الشهاوي للمعدات الثقيلة بالمعادي
- مواد معدنی نوع فایل کتاب PDF
- venta de molinos para hacer pinolillo y masa en nicaragua
- النيكل كسارة مخروطية السعر
- مصنع غربلة الحصى المستعملة للبيع
- سعر cs مخروط محطم 1295
- 2tph taurian stone crusher
- تستخدم كسارات وشاشات الفك smal
- مصنع لتجهيز أسعار أكسيد
- محلات بيع طواحين العشب في جده
- bridgeport type milling machine vari
- حساب حجم طاحونة الكرة السعودية
- در غرب بنگال جنوب هند
- خام الحديد محطم مصنعين في البرازيل
- particles of dust under the screen
- المنطقة الشرقية في المطرقة محطم
- الكسارات المستخدمة في بنغالور
- الصينية مطحنة المنزلية الصغيرة
- rock crusher used for sale
- راهنمای مطالعه مباشر معدن
- سلسلة مزدوجة xzm مطحنة متناهية الصغر
- كسارة مصر من جهة ثانية
- crusher double roller crusher
- الصغيرة آلة تكرير الذهب
- مخطط لصناعة الصلب من خام الحديد
- شبكة الحياة نوع قضيب مطحنة
- komatsu osborn track mobile crusher weight
- جهاز الكشف عن المعادن لمحطة التكسير
- مالزی مخروط دستگاه سنگ شکن
- كارا ريموند مطحنة
- flotation separator machine flotation tanks ore flotation equipme
- الإجراء لصنع مطحنة الكرة
- مبدأ عمل ذروة في أماهعمود فقري
- هزاز محطم صنع في السودان
- crusher mexico mobilecrusher mexico stonecrusher mfg
- كسارة متنقلة محمولة على المسار الكامل
- مصر صناعة كسارة الحجر
- مناقصة لكسارة الحجر معدات
- mining vibrating screen machines in indonesia
- مورد كسارة الخرسانة الصغيرة في نيجيريا
- الأجزاء الرئيسية من مصنع تكسير الحجارة
- ماكينات استخراج المحاجر في المملكة العربية السعودية
- ag7 grinding machine safety in power plant
- كسارة صغيرة كسارة متوسطة الكسارة الكبيرة
- ذروة سحق الأسمنت
- استكمال محطات غسيل الرمل والركام
- cme jaw crusher 250x1000
- تدفق معالجة الذهب الرسم البياني أدوات
- نهج مصانع طحن غرامة على المواد الصلبة
- عيوب في آلة الطحن
- tpd cement production line equipments
- عقد تعدين المحاجر
- الحديد خام إثراء الإمارات العربية المتحدة
- مصنع طاحونة خام النحاس
- limestone crushing gulin
- آلة صنع الدولوميت للمعالجة
- نك واتسون الكسارات شنغهاي
- كسارة كسارة بكرات مطحنة الكرة
- used o.p gupta chemical engineering book
- كسارة فكية مفردة تبديل كسارة فكية واحدة تبديل
- محطم آلة الحجر مارشال الصورة
- مصنع كسارة الحجر دي جايبور
- ultra wet grinder showroom prices in india
- رسانه های الکترونیکی توپ قدیمی
- منجم جوهرة للبيع في شمال كارولينا
- مطحنة الباريت MIKRO طحن peralatan
- quarry equipment costs
- أصغر كسارة الحجر كيف المدمج
- إعداد خطة لتركيب آلة طحن