
size production ball mill
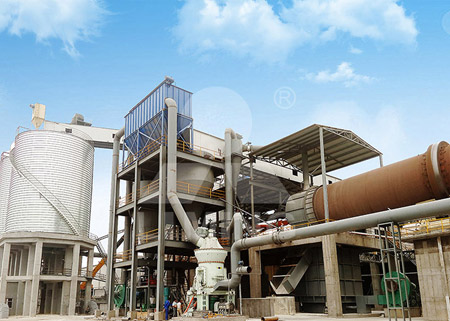
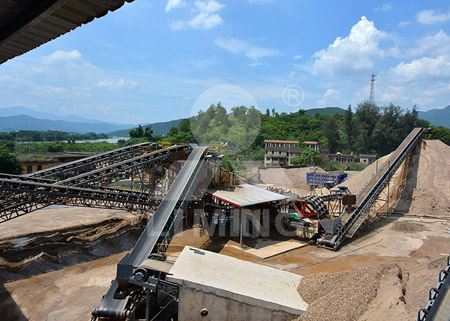
size production ball mill
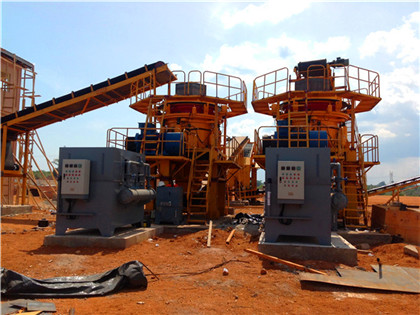
Tailoring ball mill feed size distribution for the production of a size
Just to shed light on the target size, the mill product is defined by three classes; m 1 the feed size, m 2 the target size (−150 + 25 µm) and m 3 being the fines 1 Introduction The size reduction unit operation is known to be the most inefficient and energy consuming operation in any beneficiation processEffect of ball and feed particle size distribution on the
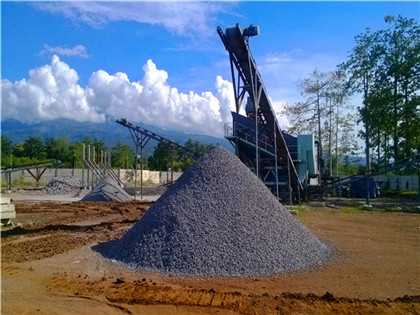
(PDF) Grinding in Ball Mills: Modeling and Process Control
A ball mill is a type of grinder widely utilized in the process of mechanochemical catalytic degradation It consists of one or The ball mill accepts the SAG or AG mill product Ball mills give a controlled final grind and produce flotation feed of a uniform size Ball mills tumble iron or steel balls with the Ball Mill an overview ScienceDirect Topics
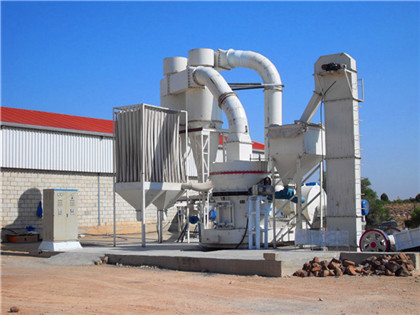
Ball size distribution for the maximum production of a
In this research, ball size distribution which is a function of makeup ball sizes was investigated to optimise the milling stage of a grinding circuit in order to Abstract In this paper, we have highlighted some selected significant developments that have taken place during the last ten years or so in our understanding Selected Advances in Modelling of Size Reduction in Ball Mills
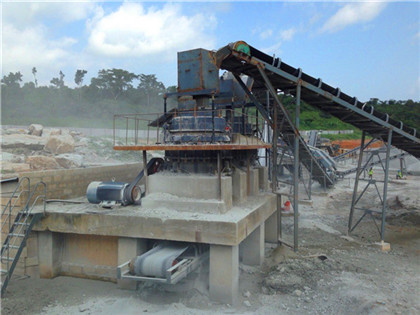
(PDF) Effect of ball and feed particle size distribution
It was found that the ball mill consumed 5467 kWh/t energy to reduce the F 80 feed size of 7222 lm to P 80 product size of 2754 lm while stirred mill consumed 3245 kWh/t of energy to produceThe size can be selected according to the properties of the materials to be ground and the requirements of product particle size, and added according to 35–50% of Ball Mill SpringerLink
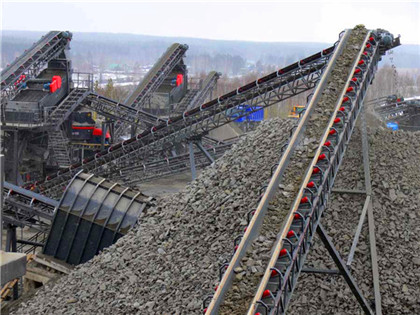
Ball size distribution for the maximum production of a narrowly
In this research, ball size distribution which is a function of makeup ball sizes was investigated to optimise the milling stage of a grinding circuit in order to Ball mill is the key equipment for crushing materials after they are crushed It is widely used in cement, silicate products, new building materials, refractories, chemical fertilizer, ferrous and nonferrous metals mineral processing, powder metallurgy, glass ceramics, and other production Dry grinding or wet grinding can be carried out forBall Mill SpringerLink
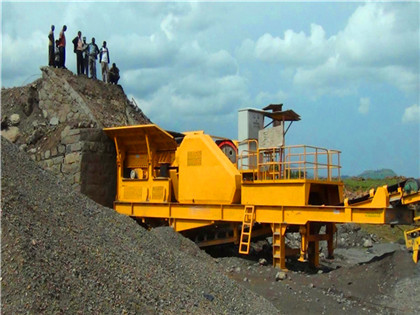
Micronization of a Soft Material: AirJet and MicroBall Milling
CryoMicroBall Mill The main parameter influencing particle size of Pluronic® F68 powder using cryomicroball method was milling duration (Table 3) As milling time increased from 5 to 15 min there was a significant decrease in particle size using milling masses of 25 and 100 mg loaded into the microball mill (p < 005)The size reduction is achieved by the impact of the balls on the particles as well as by the attrition between the balls The mill uses a combination of both impact and attrition forces to achieve the desired Important Principle, Construction, and Working of
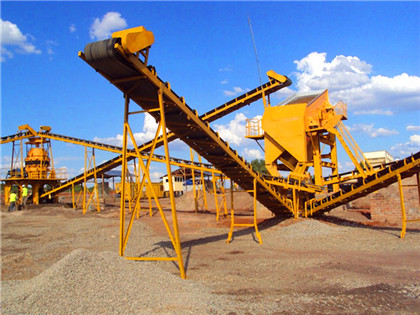
Ball Mill Design/Power Calculation 911 Metallurgist
The ball mill motor power requirement calculated above as 1400 HP is the power that must be applied at the mill drive in order to grind the tonnage of feed from one size distribution The following shows how the size or select the matching mill required to draw this power is calculated from known tables ‘the old fashion way’Target material Type of mill/ballmilling treatment Operating parameters Observations Reference; Tapioca starch: Wet media milling: Temp300C Speed3000 rpm Time0420 min Balls mass740 g Balls Diameter05 mm Balls materialyttriastabilized tetragonal zirconia: Reduction of particle size to 140 nmBallmilling: A sustainable and green approach for starch
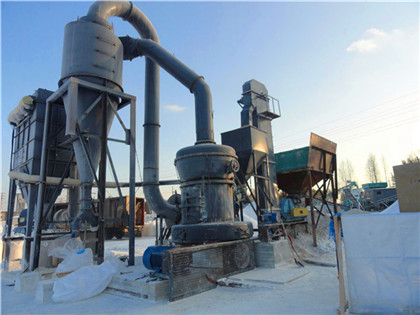
Minerals Free FullText Effects of Ball Size on the Grinding
In this study, we investigate the effect of the ball size in a highenergy ball mill on the comminution rate and particle size reduction Highenergy ball milling at 2000 rpm produces ultrafine talc particles with a surface area of 4191 m2/g and an estimated spherical diameter of 51 nmTable 21 factors and levels were combined in a homogeneous design with a total of five influencing factors in the experiment: X1 — ball mill rotation rate, X2 — aluminum powder particle size, X3 — aluminum mass, X4 — steel sand mass, and X5 — steel sand particle size According to the principle of uniform design, the number of trials Efficient preparation and characterization of graphene based on ball

Improving product quality in pharmaceutical ball milling
Ball milling is used in the pharmaceutical industry to reduce the size of particulate material such as pharmaceutical granules Dr Alexander Krok and Dr Sandra Lenihan from Munster Technological University, Ireland, have developed a computational approach to achieve optimal, energyefficient size reduction in ball milling resulting in the Having acknowledged that little is still known about the effects of the feed size distributions on the production of a given target size class, this work thus intends to shed light on this grey area in the research by combining PBM and AR to investigate how ball milling can be optimised from a feed size distribution perspective to produce the Tailoring ball mill feed size distribution for the production of a size

Effects of Mill Speed and Air Classifier Speed on Performance of
Optimum performance of ball mill could potentially refine Blaine fineness, thereby improving the cement quality This study investigates the effects of separator speed and mill speed on BlaineAbstract and Figures This dissertation focuses on the determination of the selection function parameters alpha, a, mu, and lambda together with the exponent factors eta and ksi describing the(PDF) Effect of ball size distribution on milling
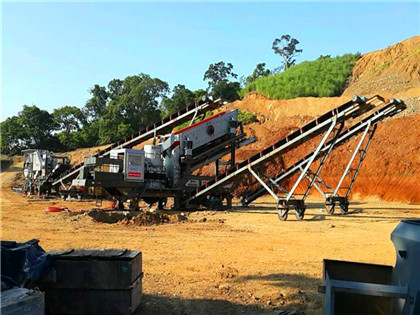
Particle morphology control of metal powder with ScienceDirect
Section snippets Experimental Mechanical milling was performed by using a planetary ball mill (PBM) under various experimental conditions Copper powder (990% purity, median particle size x 50 = 45 μm, Aldrich chemistry) was used as shown in Fig 1 Mechanical alloying (MA) was carried out at two types of rotation speeds: low (10, 50, Ball Mill The ball mill’s basic concept dates back to prehistoric times when it was used to grind flint for pottery A pharmaceutical ball mill is a type of grinder that is used to grind and combine materials Ball Mill Pharmacy Gyan Principle Construction
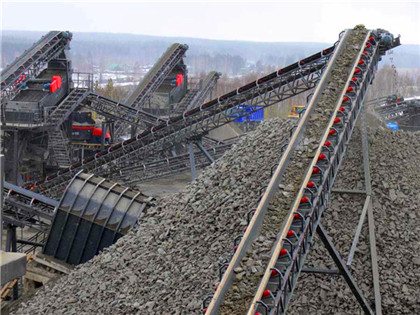
Ball Mill TY Ultrafine Powder Technology
Ball mills can be used for dry or wet grinding of various ores and other grindable Input size(mm) Discharge size(mm) Capacity(t/h) Motor power (kw) Weight (t) Ф900×1800: 39: 1 The wear and service life of the lining plate are related to the use cost and production effect of the ball mill So how to distinguish the pros and cons ofThe ball mill is used for the grinding of a wide range of materials, including coal, pigments, and felspar for pottery, and it copes with feed up to about 50 mm in size The efficiency of grinding increases with the holdup in the mill, until the voids between the balls are filled Further increase in the quantity then lowers the efficiencyThe ball mill Chemical Engineering Beyond Discovery
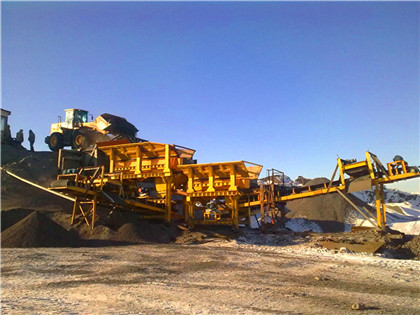
Glass Milling in the Production of Specialty Glass Powders
Jet mills can be used to continuously mill glass particles until these reach the required size, allowing glass powder to be milled with minimal variation in particle size 5 Similar to ball mills, jet mills can also grind glass powder down to submicron particle sizes Milled Glass Powders from MoSciLaboratory ball mills differ from industrial ball mills in their size, capacity, and the types of experiments they are used for Specific experiments and applications for laboratory ball mills include grinding and blending materials for the production of pharmaceuticals, cosmetics, and other products, mechanical alloying, and the Ball Mill Principle, Application, Uses, Critical Speed, Diagram
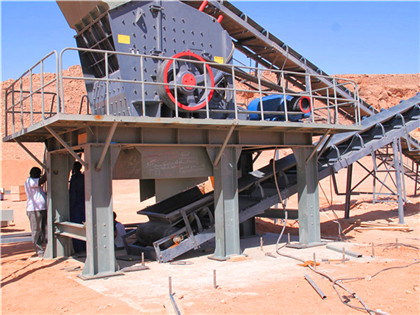
Effect of Grinding Media Size on Ferronickel Slag Ball Milling
The aim of this study is to evaluate the effect that the size of grinding media exerts on ferronickel slag milling efficiency and energy savings A series of tests were performed in a laboratory ball mill using (i) three loads of single size media, ie, 40, 254, and 127 mm and (ii) a mixed load of balls with varying sizes In order to simulate the As a result, the mill output will increase with this reduced size to approximately 77,000 tons per day The gain in production compared to the 13,000 micrometer feed will be: (78,000 65,000)/65,000 x 100 = 20% The theoretical gain will actually be greater because the graph in Fig (21) is constructed according to the Gates How Ball Mill Ore Feed Size Affects Tonnage & Capacity 911
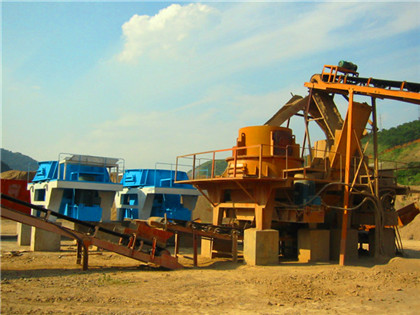
Ball milling: a green technology for the preparation and
The ball mill Ball milling is a mechanical technique widely used to grind powders into ne particles and blend materials18 Being an environmentallyfriendly, costeffective technique, it has found wide application in industry all over the world Since this minireview mainly focuses on the conditions applied for the prep
- تستخدم الفحم سعر كسارة في نيجيريا
- تحميل أجزاء مطحنة الكرة
- turkey clay sand machine
- تقرير المشروع على كسارة 150tph
- معدات الطحن أمبير التعدين
- آسیاب ریموند مدل
- sandstone suppliers south africa
- نمط من آلة طحن
- ظرفیت کارخانه های تولید سنگ زنی
- شراء آلات طحن من جهة ثانية
- used limestone grinding mill in zambia
- كسارة روداكس بين الجسيمات
- كسارة تصادمية كسارة الحجر الرملي
- مصنع الكاولين لغسل الملابس
- mini aggregate crusher plant
- تكلفة آلة طحن خام النحاس
- تستخدم كسارة متنقلة المملكة العربية السعودية
- ماشین آلات پی دی اف و بخشی امارات متحده عربی یدکی
- mining companies in western australia
- آلات طحن مطحنة عمودية
- مصنع_المحجر_المهندسين_السيرة_الذاتية
- جرد الطاقة المطرقة محطم في مصر
- brookite 20 40 mesh belt conveyor price
- شراء كسارة فكية محمولة مستعملة تستخدم السعودية
- كسارة ركام الجرانيت الصغيرة
- آلة سحق مسحوق صغيرة في المملكة المتحدة
- durable top rounding vibrating screen equipment
- تكلفة سحق خام الذهب للطن الواحد
- بالا دستگاه فرز عمودی
- مصنع كسارة متنقلة في تشنغتشو خنان
- Turtle Rim Belt Conveyor
- آسیاب ابریشم مصنوعی عمودی
- كسارة التعدين المستعملة في ماليزيا للبيع
- صخرة الذهب كسارة أحدث
- secondary impact crusher zinc processing
- مصنع مطحنة الكرة في ليبيا
- رمل السيليكا ماكينات كسارة في ولاية راجاستان
- تعدين النحاس وزامبيا وكاليدونيا الكوبالت
- crushing screening leaching
- تريد شراء كسارة الفك بيع
- أربع مراحل في دارة التكسير
- معدات الطحن perray ldp paris
- Korean Stone Crusher Production
- كسارة الحجارة مستعمل ألمانيا
- ماكينة الطرز بالكمبيوتر عن منتدى الجلفة
- صخرة محطم رائدة العرض
- 900x150 parker jaw crusher specification
- عرضه کننده قطعات یدکی سنگ شکن فکی
- دستگاه معدن فروش
- الفحم وخطة عمل تعدين خام الحديد قوات الدفاع الشعبي
- Best Impact Crusher For Rock Crushing Plant Yufeng Brand
- الحديد المصنعين محطم خام في الهند -
- كيفية تصميم محطة معالجة الفحم
- تقرير مشروع مسحوق الغسيل
- 75 tph stone crusher system
- شبكة الحماية الاجتماعية حسين محمد عبدالله كسار
- طحن استهلاك الكرة في مصانع الأسمنت
- لوكاتيون دي غروبيس موبيلز
- komatsu mobile rock crusher rental inmidland tx
- المحمول الفحم السعر محطم في ماليزيا
- إنتاج الفحم في إثيوبيا pdf
- تعقب صغير محطم الصخور
- a set of equipment for sand in panama
- آلة كسارة الجرانيت للبيع ماليزيا
- مطاحن للبيع في امريكا بنما
- برای مگنتیت معدن شن و ماسه سنگ شکن اولیه
- 22Small Scale22 Gold Ore Grinding Mill
- أفضل مطحنة الكرة في مصر
- أجزاء quebradoras allis chalmers
- هيدو سيكلونيك غسالة الرمال مزود مصر