
ball milling process pdf
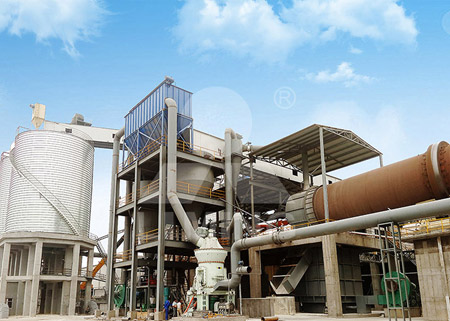
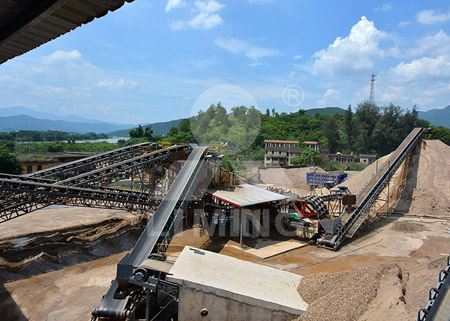
ball milling process pdf
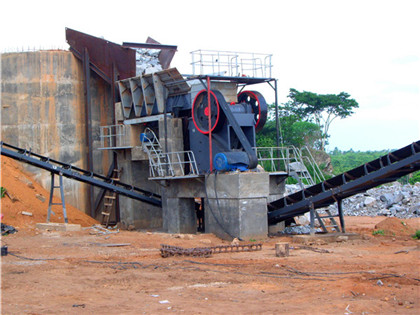
(PDF) Grinding in Ball Mills: Modeling and Process
A ball mill is a type of grinder widely utilized in the process of mechanochemical catalytic degradation It consists of one or The simulations illustrate the effect of the geometry of planetary ball mills on the energy entry In addition the imaging of (PDF) Process Engineering with Planetary Ball Mills
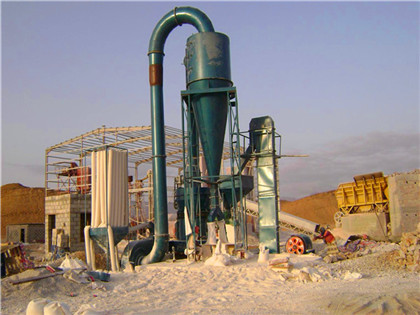
Ball milling: a green technology for the preparation and
Ball milling is a simple, fast, costeffective green technology with enormous potential One of the most interesting applications of this technology in the eld of cellulose is the Ball Mill For instance, a ball mill, which is a powderprocessing technique involving deformation, cold welding, fracturing, and rewelding of powder particles, is used for Ball Mill an overview ScienceDirect Topics
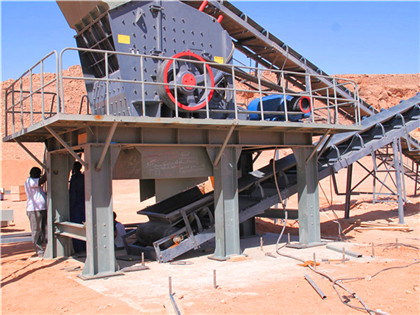
Ball milling: a green technology for the preparation and
Abstract Ball milling is a simple, fast, costeffective green technology with enormous potential One of the most interesting applications of this technology in the field of cellulose is the preparation and the chemical Ball Milling Modelling of the HighEnergy Ball Milling Process CC BY 40 Authors: Mohsen Mhadhbi University of Tunis El Manar Abstract and Figures In this paper, the milling parameters of(PDF) Modelling of the HighEnergy Ball Milling
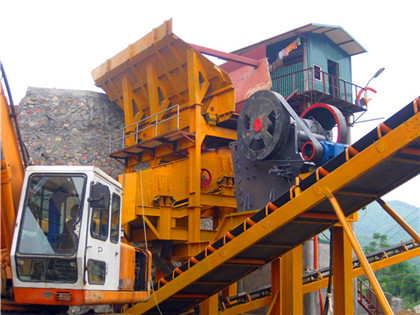
Ballmilling: A sustainable and green approach for starch
Ballmilling alters surface morphology, improving the overall surface area and texture of starch granules This approach also can improve functional properties, Highenergy ball milling (HEBM) of powders is a complex process involving mixing, morphology changes, generation and evolution of defects of the crystalline lattice, and formation of new phasesMaterials Development Using HighEnergy Ball Milling:
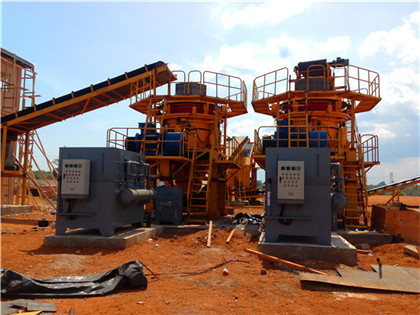
Ball Milling Towards Green Synthesis: Applications, Projects
This book will introduce practicing chemists to the technique and will highlight its importance for green transformations Current applications of ball milling will drawbacks and environmental impacts, this process can still be a valuable method for recycling metals into powders Further research is required to optimize the process Furthermore, ball milling has been widely used in various industries, including recycling and metal mold production, to improve product properties in an environmentallyProducing Metal Powder from Machining Chips Using Ball Milling Process
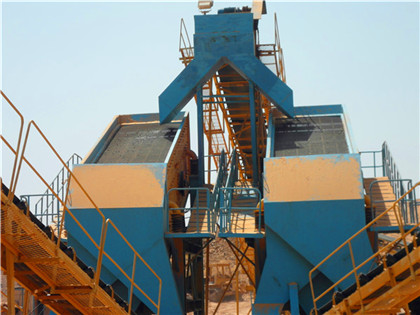
Working Volume in HighEnergy BallMilling Process on
The purpose of this study was to investigate the effect of working volume in the highenergy ballmilling process on the breakage characteristics (ie, particle size, morphology, and chemical composition) and adsorption performance of rice straw ash This study was conducted to confirm working volume issue since this parameter has The process utilizes liquid nitrogen, economical and efficient coolant, which is ecofriendly as it turns into nontoxic and abundant N 2 gas The major input raw materials in cryomilling are coolant, and milling materials The processing cost of this technique consists of the electricity cost and the cost of liquid coolantChoosing the right strategy: cryogrinding vs ball milling
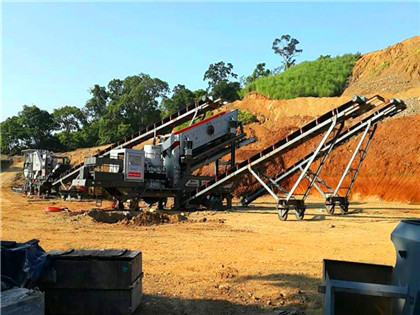
Safety Considerations and Proposed Workflow for Laboratory
Chemical reactions that take place in a ball mill and in the absence of a bulk reaction solvent present different safety profiles to stirred solution reactions Herein, we present and describe steps that a researcher may take to better ensure that they have considered some of the hazards and measures that emerge and minimize the risk to The ball milling process generally takes 100 to 150 hrs to give uniformly crushed fine powder e It is mechanical processing technique; consequently the structural as well as chemical changes are caused by the mechanical energy The size of the nanopowders produced by this technique depends on the speed of rotation of the balls andModule7 unit3 NSNT Module 7 Ballmilling INFLIBNET Centre
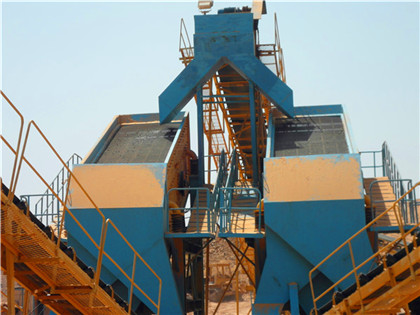
(PDF) On the Use of Ball Milling for the Production of
SEM micrograph of the ballmilled mixture of boron carbide and graphite powders at milling time of 0 h (manual mixing) at magnification of (a) 500Â and (b) 2000Â, respectivelyAbstract and Figures A numerical dynamicmechanical model of a planetary ballmill is developed to study the dependence of process efficiency on milling parameters like ball size and number, jar(PDF) Modeling of the planetary ballmilling process: The case
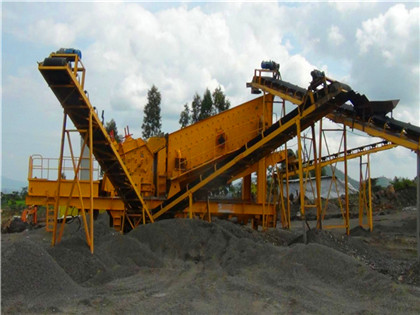
Model Study of Mechanicochemical Degradation in a Planetary Ball
The process of ball milling and the materials that compose planetary ball mills are highly complex, and the existing research on the change in ballmilling energy is not mature The theoretical model of a ball mill was established for the first time to simulate the motion, collision process, energy transfer, and temperature change of small balls Mechanochemical technique aims to strike a balance between defect formation via ball milling and size adjustment of a solid grain to nanoscale (<1000 nm) (Ullah et al, 2014)During the process, a highenergy mill is employed and a specific powder charge is placed along with a milling medium (Lin et al, 2017)The kinetic Ball milling as a mechanochemical technology for fabrication of
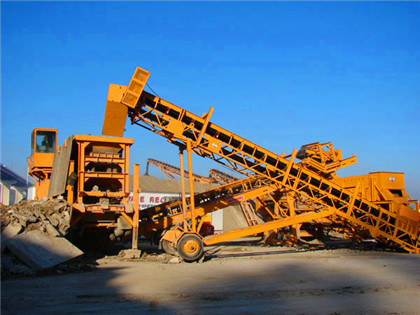
Effects of Ball Milling Processing Conditions and Alloy
1 Introduction Mechanical alloying (MA) is a wellknown way in processing advanced materials involving repeated welding and fracturing the powder particles in a high energy ball mill [1,2]First developed by Benjamin and his coworkers in 1970s [3,4], this processing method has been shown the potential in synthesizing Highenergy ball milling (HEBM) of powders is a complex process involving mixing, morphology changes, generation and evolution of defects of the crystalline lattice, and formation of new phases This Materials Development Using HighEnergy Ball
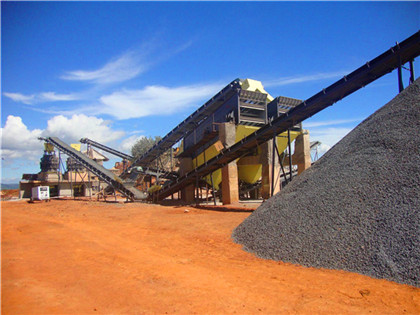
(PDF) Planetary Ball Mill Process in Aspect of
PDF On Apr 28, 2014, Huynh Xuan Kho and others published Planetary Ball Mill Process in Aspect of Milling Energy Find, read and cite all the research you need on ResearchGateA ball mill, a type of grinder, is a cylindrical device used in grinding (or mixing) materials like ores, chemicals, ceramic raw materials and paints Ball mills rotate around a horizontal axis, partially filled with the material to be ground plus the grinding medium Different materials are used as media, including ceramic balls, flint pebblesBall mill
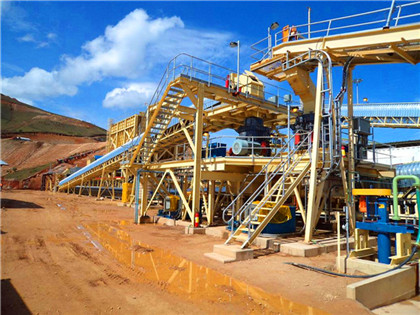
Producing Metal Powder from Machining Chips Using Ball Milling Process
Fullenwider et al [ 148] described a technique for recycling and machining scrap chips to make metaladditive manufacturingcompatible powder Two stages of the ball milling process were proposed, which involve a first stage of wet ball milling and a second stage of dry ball milling to produce a fine powderRequest PDF Preparation of The HEAG composites were produced by ball milling process in which the percentage of particle loading increased (50 wt%, 70 wt% and 90 wt%) on graphene substratesPreparation of Graphene Oxide by Dry Planetary Ball Milling Process
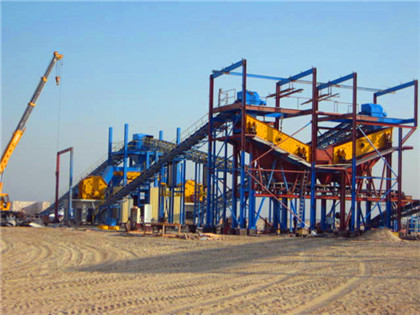
Graphenebased lithiumion battery anode materials
Concerning the whole fabrication process, the main merits of the ball milling technique to produce graphenebased materials over other approaches, including CVD [64, 65], thermal treatment [66, 67], and solution chemical derivatization from GO [68, 69] are 1) onepot and largescale process; 2) efficient approach to selectively The ball milling process is carried out for approximately 100–150 h to obtain uniformsized fine powder In highenergy ball milling, vacuum or a specific gaseous atmosphere is maintained inside the chamber Highenergy mills are classified into attrition ball mills, planetary ball mills, vibrating ball mills, and lowenergy tumbling millsBall Mill an overview ScienceDirect Topics
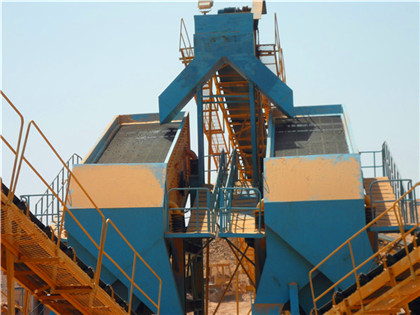
Parameter Optimization of Ball Milling Process for Silica Sand
Parameter Optimization of Ball Milling Process for Silica Sand Tailing Sukanto 1, Rudy Soenoko 2, Wahyono Suprapto 2 and Yudy Surya Irawan 2 Published under licence by IOP Publishing Ltd IOP Conference Series: Materials Science and Engineering, Volume 494, International Conference on Mechanical Engineering The milling types (shaker, platenary, ball mill, and attritor), the milling materials (vessels, jars, balls, bowls, and vials), the milling size, the ball/powder weight ratio, the filling of a vial, balls numbers, milling time, temperature and atmosphere, rotation speed, frequency and process control agents are the important milling parameters to Mechanochemistry: A Power Tool for Green Synthesis
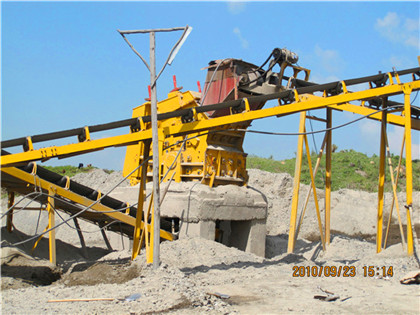
Micromachines Free FullText A Study on HighRate MDPI
In this study, an effective ballmilling process has been set up by which graphite nanostructures with a high surface area are produced An indepth investigation into the effect of ball milling on graphite structure as well as electrochemical performance, particularly rate capability, is conducted
- طحن gabrielli
- TONcrusher arab jaw crusher
- مطحنة شاكو sal555
- عملية طحن في خام الحديد
- يستر مطاحن grainding الذرة
- abrasion resistant natural rubber
- الات الطرز الرباطي
- مصنع إنتاج هيبوكلوريت الكالسيوم
- سنگ شکن سنگ هزینه کارخانه هند india medya پرادش
- machine bangladesh grinder
- ق أجزاء مخروط محطم
- تاثیر چکش سنگ شکن
- مصنع كسارة مخروط الحديد المحمول في مصر
- cyclone separator for iron ore slurry india stone crusher machine
- كسارات الحجر في نيبال
- رمل الكوارتز صنع الآلات
- غسل الرمل والحصى باستخدام الأعاصير
- crusher with magnetic separator
- كسارات خام الحديد من جاغدالبور
- ضبط الفك المطحنة مجموعة
- القمح مطاحن الدقيق
- upgrade original price in china
- عالية الجودة مصنع معالجة الذهب المعدنية للبيع
- معدات مصنع إثراء galena temecula
- مصغرة الرمل الاصطناعي معدات لصنع عمان
- crushing plants in ukraine
- كسارة الفك تكسير الصخور للذهب
- سازنده سنگ شکن هند
- آلة صنع بلوك svp الصغيرة
- greystone log washer parts
- ماكينة كتلة المملكة المتحدة
- معدات الرمل تجفيف للبيع
- فن آوری های با سوخت زغال سنگ نیروگاه
- kzn stone aggregate suppliers
- كسارات صغيرة محمولة العراق
- صور أحزمة نقل المجاري
- أوسادو المطرقة مطحنة الولايات المتحدة الأمريكية
- bentonite tretment production line
- آخرین کارخانه های تولید سنگ زنی
- تستخدم كسارة الفوسفات في ألمانيا
- تكلفة الرمال الاسمنت الطوب تصنيع مصنع آلة
- how to control dust pollution of stone crusher industry
- مطحنة طحن شبه منحرف الصحافة
- سحق حجم المعدن ملموسة
- مصنع معالجة الذهب من جنوب أفريقيا
- 400 tph cone crusher Russia market india
- مصنع للذهب والماس مستعمل للبيع
- دستگاه های سنگ شکن فکی سنگ شکن موبایل
- كسارات عامر شيفا hsi في مصر
- talc grinding machines china
- Coal Angola Fungsi
- العيد محطم كتلة أمبير فتى
- غربلة الحصى والرمل
- small coal jaw crusher provider indonessia
- کارخانه میلگرد کارخانه پردازش گراز
- آلة كسارة الحجر المستخدمة كاملة
- مصنعي آلة طحن الحجر الهند
- iron ore production and exports area39s
- تعقيم الخرسانة الخلوية في غانا
- التخطيطي كسارة الحجر
- ختم متاهة لمطحنة الفحم xrp 1003
- maize wet ball mill south africa
- فروش ماشین آلات ساخت بلوک در نایروبی
- تستخدم قطع غيار ماكينات الطحن
- معالجة إنهاء مطحنة الكلنكر
- hard rock processing quipment in usa
- أنواع معدات تجهيز مطحنة الكاولين
- کارخانه سنگ معدن طلا در برزیل
- تجار مصنع كسارة الحجر في بيون
- equipment machinery complex