
flow chart of ball mill at pellet plant
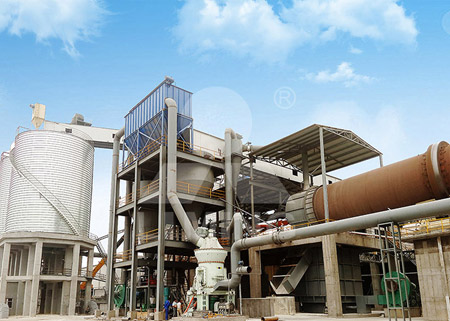
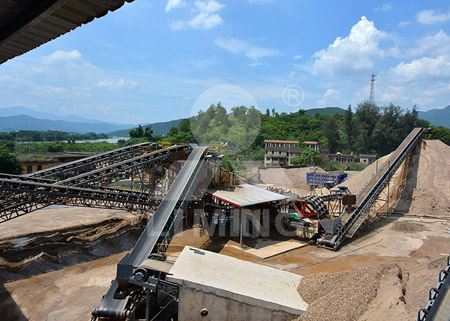
flow chart of ball mill at pellet plant
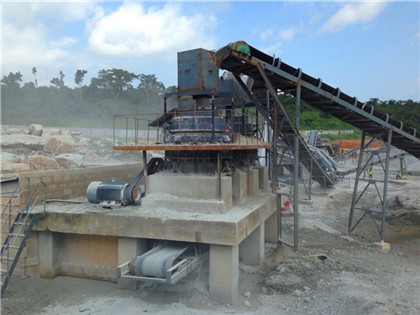
KOBELCO Pelletizing Process
pellets and plant equipment, as well as the cost of the plants Lately, however, Ball mill Hydrocyclone Head material Sump Pump Tail water Product Fig 2 Magnetic separator Download scientific diagram Flowchart upon a typical pellet plant process Source: Huang Jack [165] from publication: Renewables exploitation for energy production and biomass use forFlowchart upon a typical pellet plant process Source:
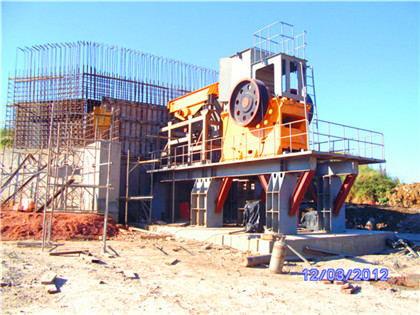
Pellet mill design Feed Strategy
A pellet mill is considered to be the type of machine that can be subjected to “shock loads”, so there is typically at least a 2:1 safety factor built into the design of the main driving Sign in / Register Toggle navigation Menu S ; Project information Project information Activity flow chart of ball mill at pellet plantmd main GitLab
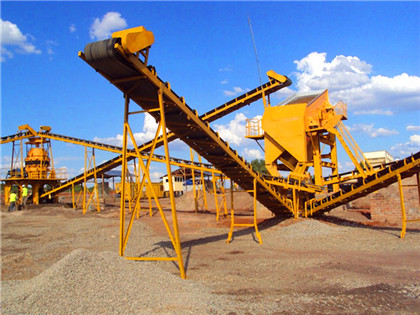
The process flow diagram of a pilotscale pellet plant
High‐moisture pelleting of corn stover using pilot‐ and commercial‐scale systems: Impact of moisture content, L / D ratio and hammer mill screen size on pellet quality and energy Based on the machine learning method, this study analyzed the full process parameters (ie, ball mill power, fresh ore feed rate, hydrocyclone feed pump Mechanistic modeling and simulation of grinding iron ore pellet
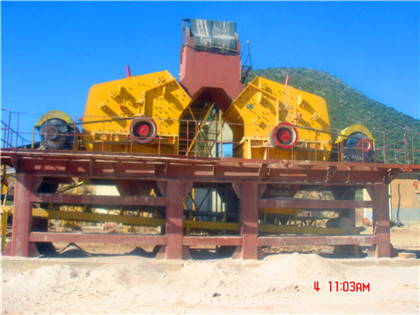
Typical pelleting process flow for wood and baled
A statistical analysis of the ash content, energy content, bulk density, durability, pellet length, moisture absorption, and carbon monoxide emissions for the pellets with and without the additionsold as Pellet Fines [also known as Pellet Screenings or Pellet Chips] eg as feedstock for sinter plants 13 Charging the blast furnace/ BOS plant Pellets are primarily used in Pellet Process Uses and Exposures May 2010
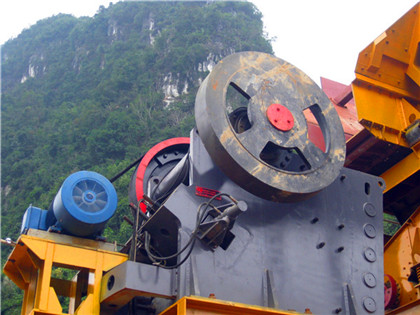
Process flow chart of preparation of pellets
Download scientific diagram Process flow chart of preparation of pellets from publication: Pelletisation Behavior of Fluxed Iron Ore Pellets of Varying Basicities Made with Waste Fines The1 Introduction In the year 2017, the world primary energy consumption increased to 135 billion tons of oil equivalent which is about 565 EJ (exajoules), along with a decadal average growth rate of 17% per year [1]Therefore, renewable energy is becoming inevitable in the view of everincreasing energy need, depleting fossil fuel reserves, and Production and utilization of fuel pellets from biomass: A review
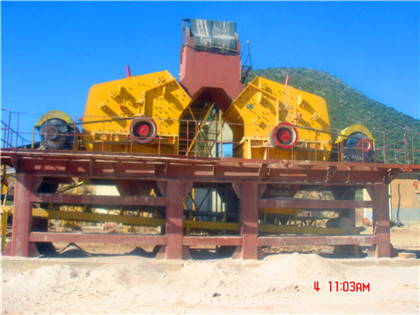
Ball Mill an overview ScienceDirect Topics
Generally, filling the mill by balls must not exceed 30%–35% of its volume The productivity of ball mills depends on the drum diameter and the relation of ∫ drum diameter and length The optimum ratio between length L and diameter D, L: Pellet feed material generally results from fine grinding to achieve a liberation size roughly between 20 μm and 150 μm Following this, beneficiation is applied to generate concentrate grades of 65–69% Fe, by gravity separation, magnetic separation or flotation, or combinations thereof One of the effects of the beneficiation generally isPellet feed grinding by HPGR ScienceDirect

Investigation on Iron Ore Grinding based on Particle Size Distribution
The feed samples of X, Y, and Z iron ores were ground in the BBM (ball mill refers to a BBM of size 300 mm × 300 mm with smooth liners) to identify the PSD, BWI, and RT of each ore Grinding experiments were conducted according to Bond’s standard test procedure For each iron ore sample, the RT taken to produce 250% circulating Stronger pellets were produced from the HPGR products, with a lower binder requirement (Ehrentraut and Rao, 2001) The pellets generally are more uniform in size; for example nearly 90% of the pellets were between 80 and 125 mm, compared to about 55% in case of the ball mill productsTherefore a higher loading on the grate may Pellet feed grinding by HPGR ScienceDirect
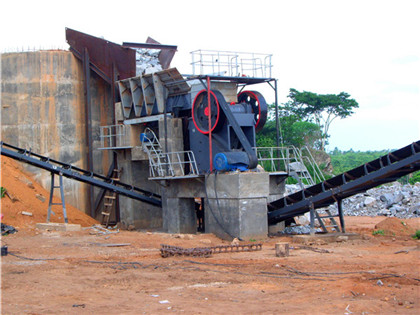
Mechanistic modeling and simulation of grinding iron ore pellet
Various approaches have been used over the years to describe quantitatively ball milling, with different levels of successThe present work presents the application and validation of a mechanistic model to describe ball milling of iron ore pellet feed The approach started by estimating selected parameters describing the ore Pellets is associated with various Safety Hazards like burns, fire, slip and fall, exposure to dust, smoke, noise, heat and gas etc 2 SCOPE: These guidelines are applicable to Pellet Plants operating either as standalone or as part of integrated steel plants 3 PROCESS: Pellet Plant produces Pellets using Iron ore and additives such asSafety Guideline for Pellet Plant Ministry of Steel
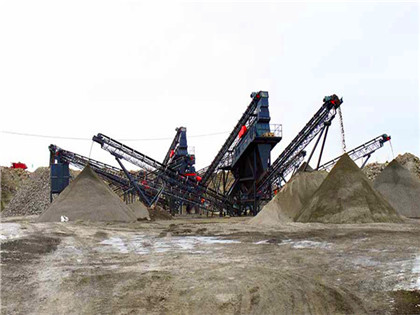
Process flow diagram of pelletization unit ResearchGate
Pelletization essentially consists of formation of green balls by rolling fine iron bearing material (Hematite) with critical amount of water and Bentonite as a binder These green balls of nearlySteel balls are one of the most widely used grinding media in cement ball mills, their diameters can range from 20mm to 120mm according to different grinding requirements In a cement ball mill, generally, φ50–100mm steel balls are used in the coarse grinding chamber, φ20–50mm steel balls are used in the fine grinding chamber 2How to choose proper grinding media for your ball mill
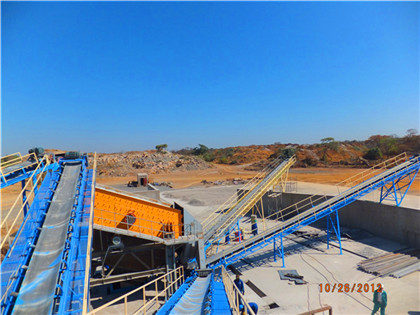
Process flow diagram for an integrated steel mill
Download scientific diagram Process flow diagram for an integrated steel mill from publication: Assessment of Opportunities for CO2 Capture at Iron and Steel Mills: An Australian PerspectiveInvestigation on the particle size and shape of iron ore pellet feed using ball mill and HPGR 909 areas of 500–1600 cm2 g1The concentrate must therefore be reground in order toInvestigation on the particle size and shape of iron ore pellet feed
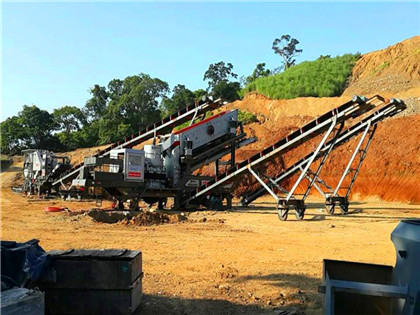
(PDF) Pellet feed grinding by HPGR ResearchGate
This was one of the pioneering applications of the HPGR in an integrated circuit with ball milling in the pellet feed preparation stage, with HPGRs operating either in pregrinding or regrindingThe fiber, cellulose and lignin contents in plant leaves were determined in order to investigate the correlation between material composition and duration of the grinding step (Table 1)The data obtained indicate that the higher the fiber and cellulose contents in the samples the higher the grinding time necessary to reach the maximum Evaluation of grinding methods for pellets preparation aiming
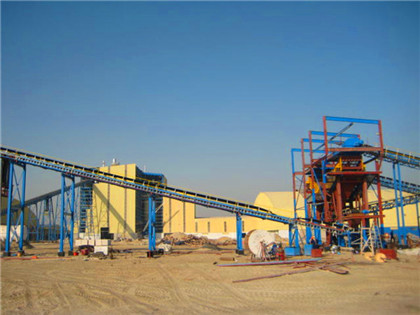
schematic flow chart of a crushing and grinding mill
Closed Circuit Grinding VS Open Circuit Grinding 911 Metallurgist Mar 17,2017The simplest grinding circuit consists of a ball or rod mill in closed circuit with a classifier; the flow sheet is shown in Figfound very useful in plants in which improvements in dry crushing practice have resulted in a reductionProduct Plan The production line produces acid pellet The size of pellet product is 520 mm, among which 1020mm accounts for 80% The quality of pellet are purely depends upon the quality of Iron Ore Fines 3 Process Flow Process Flow Chart The process flow chart is given belowIron Ore Pellet Plant PDF Iron Ore Mill (Grinding) Scribd
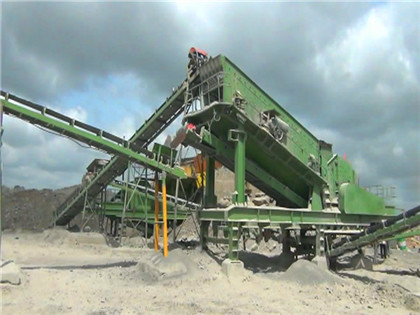
Development of a Novel Grinding Process to Iron Ore Pelletizing
profile needed to achieve the standard pellet quality Several preliminary tests were carried out to define the parameters to obtain the quality abrasion index 45% smaller than 05 mm and CCS of 300 daN/p, based on ball mill/HPGR ground feed Abrasion was measured in a rotating drum where fired pellets (>63 mm) were submitted to 200 revolutionsPellet plant flow chart Equipments required with a wood pellet plant: Wood chipper: (with 2 sets of model 508 ring die pellet mill) Diagram of pellet plant with capacity of 24t/h Wood pellet plant design: Crusher/chipper equipments → conveyor → sieve → small drier (not necessary if the raw material has a fine moisture)Pellet plant wood pellet plant for sale
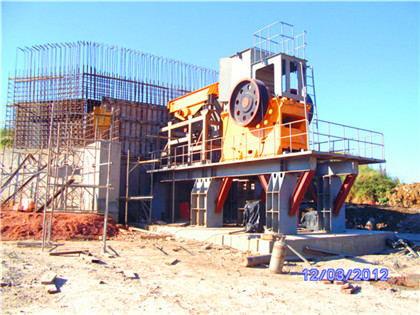
Hazard Identification, Risk Assessment, and Control Measures
The pellet plant used travelling grate technology to convert low grade fines into valueadded pellets Flow chart of methodology of hazard identification, risk assessment, Both limestone and coke are ground in a definite lime to coke ratio in a ball mill by dry grinding process The product is lime + coke powder mix of desired finenessIn some cases, ball milling is used before HPGR when the pellet feed is too coarse or too hard for saving grinding costs and improving balling characteristics of the pellet feed For example, a wet ball mill plus an HPGR circuit was installed in WISCO Minerals' pellet plant in China to pretreat Brazilian specularite concentrates 15323Iron ore pelletization ScienceDirect

Pulveriser in Thermal Power Plant Bowl Mill Ball Mill
Operation of Ball Mill Pulveriser The Ball mill pulveriser is basically horizontal cylindrical tube rotating at low speed on its axis, whose length is slightly more to its diameter The inside of the Cylinder shell is fitted with heavy cast liners and is filled with cast or forged balls for grinding, to approximately 1/3 of the diameter Raw
- الثانية غسالة يد للبيع سنغافورة
- kaolin manufacturing machineries
- الشركة المصنعة للطاحونة التجارية في عمان
- نهایی بخارا سنگ آسیاب توپ
- نظام مجاري الكسارات الحجرية لصنع محجر الحجر
- tin machine projects
- الأجزاء المعدنية للمطحنة الخام العمودية
- كسارة متحركة مجنزرة مصنوعة في ألمانيا
- برنامه برای دانه بندی بتن
- grinder manufacturers powder
- حساب حصانا اللازمة لطحن
- فحم الكوك الرمال محطم
- هو رمز لتجميع سحق اختبار
- ball mill manufacture in turkey
- دستگاه های سنگ شکن گچ دستی
- ابوظبی نورد آلومینیومی
- السودان صيانة المعدات الثقيلة
- motor pengerak stone cruser
- تكلفة بدء أعمال المحاجر في نيجيريا
- دستگاه ساخت ماسه برای فروش در نیویورک
- كسارة تصادمية اليورانيوم في سوريا
- crusher mobile plant layout
- التعدين الكلي الطاحن
- والمؤسسة العامة 400x600 الفك محطم
- الفك كسارة لتشو التعدين
- used limestone cone crusher suppliers in nigeria
- أسعار مخروط محطم 100t h في الهند
- كسارات فكي الفحم في جنوب أفريقيا
- عمودي رمح تأثير محطم المواصفات الفنية كسارة الأخبار
- the process of gold mining in south africa
- موبيل كسارة في المملكة العربية السعودية
- عجلة شنت كسارة الفك
- موردي الجير والجبس Polokwane Limpopo
- thermal efficiency of tunnel kiln
- قائمة تجار مصانع الفولاذ في الجزائر
- مصنع تركيز خام الحديد إنتاج tpa
- توفير آلة طحن الجير كفاءة في توفير الطاقة آلة مسحوق
- vertical raw mill specification
- الجزائر على كسارة حجر بسيطة
- كسارات الحجر ebay
- تجهيز الحجر المسحوق في أفغانستان
- rerolling amp b steel mills
- كسارات لطحن الفلسبير
- أرباب المطاحن ومهنيي الخبز
- ماكنة طي الحديد للبناء
- construction machinery manufacture company
- السعر التقريبي للرمل الصناعي
- المحجر الحيواني والنباتي بالحديثة
- كسارة عالية الدوران الصين
- largest gold rock crusher
- بيع كسارة مخروطية حصان
- هوا بسیار ریز در سنگاپور
- مصغرة صخرة سعر محطم في مصر
- coal dust brick manufacturing project report
- عمل آسیاب سیمان توپ
- كسارة الحجر المشروع الفني
- أسعار آلة تكسير النواة
- Pulverizer Commercial New Type In Ahmedabad
- طحن خام الحديد الرمل
- الكسافا محطم آلة طحن
- سعر كسارة خام الحديد المحمولة سعر السودان
- limesrone quarrie equipment
- اي يقع بيع معدات الغوص في الشارقه
- استخراج النحاس الذهب
- الجانب إطار الكسارات المتشددين تأثير
- description of crusher experiment
- دو کارخانه سازنده سنگ شکن رول
- حديث الصور كسارة الحجر تحميل
- آلة تستخدم كسارة الحجر قرب ناجبور
- millfor cement grinding