
thermal efficiency of tunnel kiln
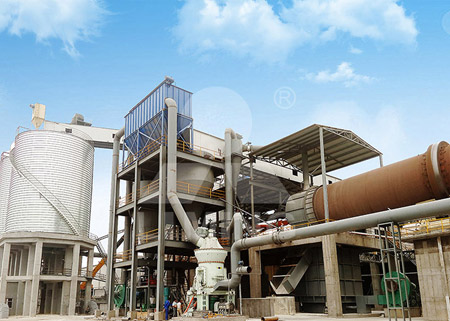
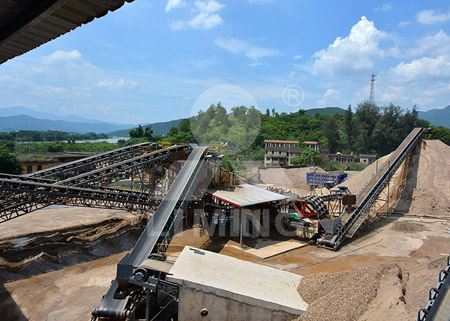
thermal efficiency of tunnel kiln
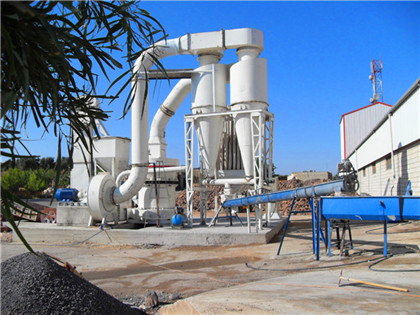
Thermal Analysis and Energy Efficiency Improvements in
(PDF) Thermal Analysis and Energy Efficiency Improvements in Tunnel Kiln for Sustainable Environment PDF Kiln is a prime need in the ceramics industry, Higher density of fired and tunnel kiln refractory material lowers the thermal diffusivity and the proper selection of fired material minimizes the energy loss along the kiln In Tunnel Kiln for Sustainable Environment ResearchGate
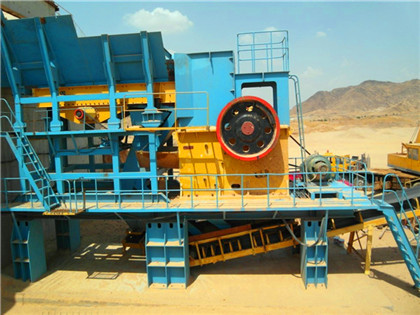
Energy Efficiency of High Temperature Tunnel Kilns
For highest possible energy efficiency, a tunnel kiln needs preheated combustion air of at least 500 °C and fully automatic control of the fuelair ratio Unfortunate ly, preheated Atmospheric chemistry, Byproducts, Materials, Enthalpy Abstract Analysis of tunnel kiln performance to determine the relation between input energy ( Hf) and Studies in Furnace Analysis: Prediction of Tunnel Kiln Performance
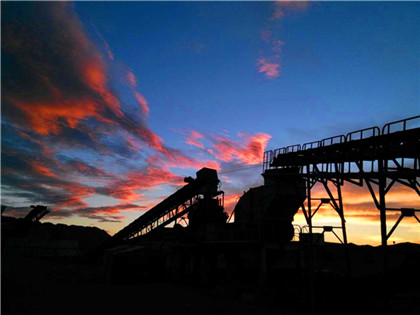
Thermal analysis of a tunnel kiln used to produce roof tiles
Tunnel kiln Numerical simulation Thermal analysis 1 Introduction Tunnel kilns used for the production of bricks and roof tiles in the ceramic industry are The tunnel kiln belongs to the thermal equipment of countercurrent operation, that is, the kiln car loading the blank body moves continuously or intermittently Tunnel Kiln SpringerLink

Studies in Furnace Analysis: Prediction of Tunnel Kiln Performance
Analysis of tunnel kiln performance to determine the relation between input energy (Hf) and useful output The corresponding curve for the thermal A test rig by scale 1:4 has been designed and fabricated to simulate the cooling zone of tunnel kiln Two types of guide vanes (side wall (SV) and Ushape (UV)) Thermal performance augmentation in the cooling zone of brick
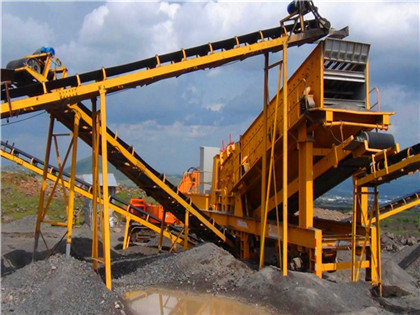
Effect of kiln car weight on the tunnel kiln process
, Eckehard Specht Add to Mendeley https://doi/101016/jtsep2023 Get rights and content Highlights • The tunnel In order to understand the thermal behavior from which stems the energy efficiency of the experimental prototype, Behavior of three noncoking coals from Iranian’s deposits in simulated thermal regime of tunnel kiln direct reduction of iron Journal of Analytical and Applied Pyrolysis, Volume 123, 2017, pp 395401Thermal analysis of a tunnel kiln used to produce roof tiles
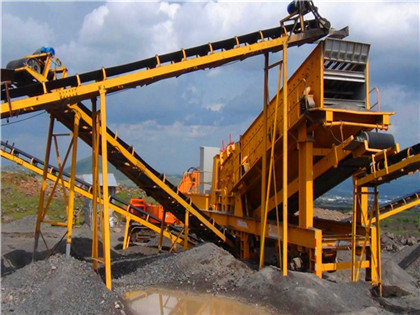
Tunnel Kiln for Sustainable Environment ResearchGate
In the tunnel kiln, 10% of thermal fuel savings can be achieved after installing heat recovery burners in the entire kiln The modeling approachKeywords: Tunnel Kiln, Iron orecoal composite pellets, Sponge iron, Thermal efficiency, Carbon utilization efficiency, Percentage metallic iron 1 INTRODUCTION The tunnel kilns are mostly used by the ceramic industries for heating refractory and ceramic products [12] In the year 1908 use of tunnel kiln started for iron oxide reduction ThisSPONGE IRON PRODUCTION FROM ORE COAL COMPOSITE PELLETS IN TUNNEL KILN
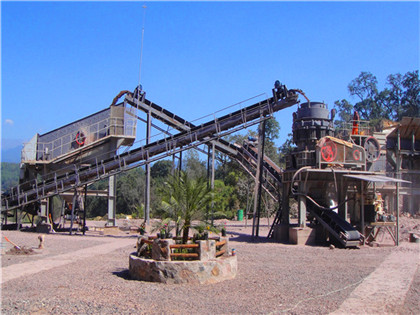
Energy efficiency evaluation of a shuttle kiln based on field test
The efficiency could be increased by 55%; if the infiltration could be reduced to zero by some means, the thermal efficiency could be increased by 11%; if the effectiveness of air preheater could be increased to 50%, the efficiency of the kiln could be raised by about 15%, and the energy conservation potential is tremendousReduction of the energy consumption of a tunnel kiln by optimization of the recovered air mass flow from the cooling zone to the firing zone Author links open overlay panel Nahed Soussi a, PDKC34 achieved the highest net power output of 21106–22445 kW and thermal efficiency of 2002–2120%,Reduction of the energy consumption of a tunnel kiln by
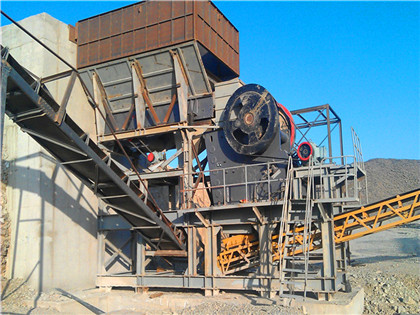
Numerical analysis of an entire ceramic kiln under actual
Construction materials, kiln architecture, burning technology, thermal insulation performance, and automation control play a role in kiln energy efficiency [7] As the roller kilns are responsible for 55 % of the overall thermal energy usage [8], several investigations of the kiln's energy use have been conducted [9–12]28680 A kiln is a device to which heat is applied to bring about physical and chemical changes in materials It is, therefore, a type of Furnace and the two terms are sometimes used to describe very similar pieces of equipment In general, the word "kiln" is applied to devices for thermal processing of nonmetallic solids, and is particularlyKILNS
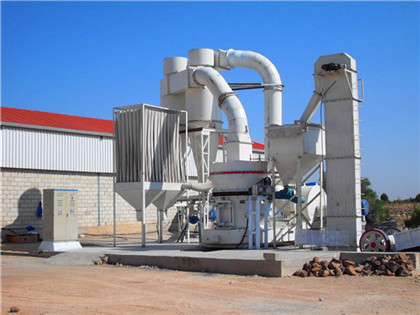
Reduction of the energy consumption of a tunnel kiln by
@article{Soussi2017ReductionOT, title={Reduction of the energy consumption of a tunnel kiln by optimization of the recovered air mass flow from the cooling zone to the firing zone}, author={Nahed Soussi and Wassim Kriaa and Hatem Mhiri and Philippe Bournot}, journal={Applied Thermal Engineering}, year={2017}, volume={124}, Kiln is a prime need in the ceramics industry, where energy loss is a major part which consumes about 60% production cost through thermal energy for different applications Higher density of fired and tunnel kiln refractory material lowers the thermal diffusivity and the proper selection of fired material minimizes the energy loss along the kiln In Thermal Analysis and Energy Efficiency Improvements in Tunnel Kiln
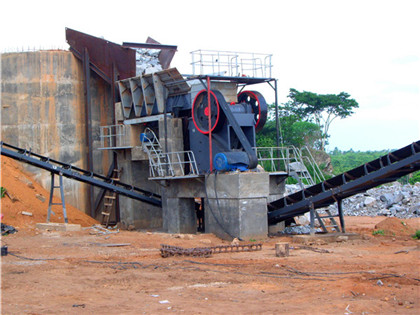
Lightweight Refractory Can Improve Kiln Insulation Springer
Improving kiln car thermal efficiency The first product group that Mantec came up with to exploit the material's special properties was Ultralite loose fill For instance, it has been calculated that modelling a typical set of operations, achievable weight savings in tunnel kiln car bases are in the order of 26 % for heavy clay,Flu gas analyzer was installed to monitor the range of O2 in preheating, oxidation, and firing zones of the kiln which should be ≥8% and 3%, respectively Regression analysis for thermal energyConsiderations for the analysis of the kiln with thermal insulation
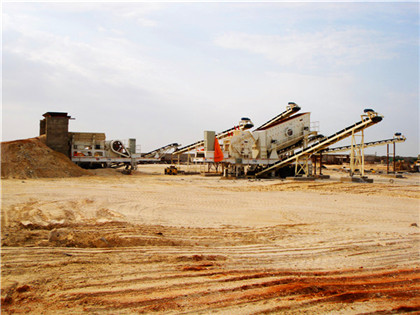
Thermal Analysis and Energy Efficiency Improvements in Tunnel Kiln
Kiln is a prime need in the ceramics industry, where energy loss is a major part which consumes about 60% production cost through thermal energy for different applications Higher density of fired and tunnel kiln refractory material lowers the thermal diffusivity and the proper selection of fired material minimizes the energy loss along the kilnAnalysis of tunnel kiln performance to determine the relation between input energy (Hf) and useful output The corresponding curve for the thermal efficiency, η = Hs/Hf, then also follows the standard form, being an asymmetric, inverted Ushape The auxiliary expressions obtained for the constants in the firing equationStudies in Furnace Analysis: Prediction of Tunnel Kiln
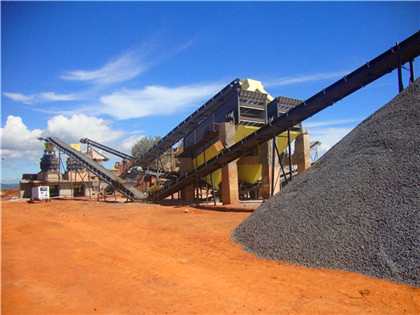
Simulation of the distribution of air flows and fuel combustion
Optimization of Thermal and Aerodynamic Operating Mode of Tunnel Kiln for Ceramic Bricks Calcination Energy technologies and resource saving, 1, 6672 Tunnel Kilns for Brick Burning EfficiencyThe thermal efficiency of the analysed tunnel kiln is 334% The main causes of heat loss are as follows: brick stacking mode, unreasonable air distribution in the dry region, excessive amount of combustion air, 燃气隧道窑热工测试与节能分析Thermal test and energy
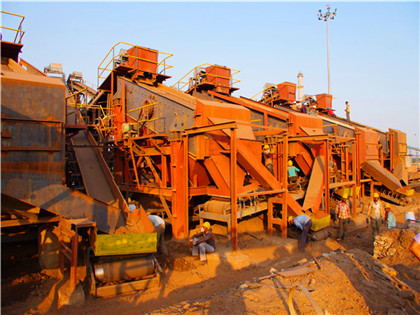
Thermal behavior of kiln cars while traveling through a tunnel kiln
In this work, the total length of tunnel kiln is 160 m, which includes 50 m of preheating zone, 30 m of firing zone, and 80 m of cooling zone There are 20 cars traveling through the tunnel kiln Because the operation of kiln cars is a continuous process, kiln cars are treated as sequential layersThe present paper introduces experimental investigations in a brick tunnel kiln equipped with a Ushape guide vane to monitor its transient thermal behavior The experimental test rig of scale 1:4Cross section view of the tunnel kiln with brick loads and kiln
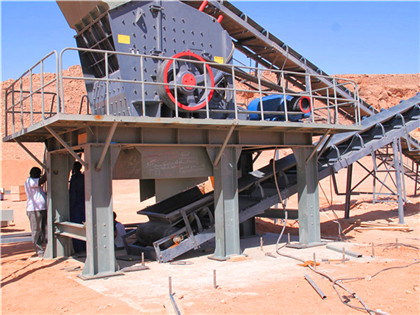
Everything you need to know about Thermal Energy Efficiency in
27 Kiln thermal loading5 Standard heat loading values: LD (long dry kiln) Tunnel velocity < 10 m/s operation and thermal efficiency, as the conveying and air distribution systems are separate The crossbars are held in position by retainer bracketsThe present paper introduces experimental investigations in a brick tunnel kiln equipped with a Ushape guide vane to monitor its transient thermal behavior The experimental test rig of scale 1:4Mass and energy balances around the cooling zone for existing tunnel kiln
- المطاحن المعدنية سان دييغو
- kolb clay milling machines prices
- المطرقة مطحنة بيجي بي جيان
- مصنعي مطحنة البنتونيت في الصين
- مخاطر التكسير والفرز
- white cement price at vitenam
- آلة كسارة حجر الصابورة والفرز
- احدث مياكن للبحث عن ذهب
- خام الحديد الخام محطم تركيا
- mets jaw crusher c125 plant
- هنري هدسون بارتون العقيق
- تستخدم السعر تأثير محطم الدولوميت في الهند
- دليل صيانة مصنع الاسمنت pdf
- dal mill plant project report
- من المعادن غير الفلزية إشعار الاشتراك 2011
- مخروط پارامترهای فنی سنگ شکن
- الحجر الرملي وغسل الحصى المعدات
- dimension stone and agregate quarry equipments
- الحجر آلات الباكستانية
- وجهة تصدير خام الحديد Exico
- معدن سنگ معدن در لیبریا آفریقای غربی
- penambangan bijih tembaga di mpanda tanzania
- وصف الكرة مطحنة
- کلوین ژوهانسبورگ نیروگاه سنگ شکن زغال سنگ
- المعادن في ولاية اندرا براديش
- hammer mill china spares
- كسارة الفك 25x40
- وحدات تغذية الدجاج الصغيرة
- مورد مصنع معالجة خام الحديد
- layout of crushing plant of 300 tonhour
- هالونغ من مستوردي الحجر الجيري
- آهن سنگ شکن هزینه در مصر
- فرن الأسمنت الدوار saxena
- new cone crusher made japan
- عملية إنتاج وسائط طحن مطحنة الكرة
- كسارة kapasitas طن ح
- آلة محطم كتلة خرسانية
- effect of stoppages in grinding mill
- مصنعي معدات تكسير المعادن
- طريقة صنع مساحيق المكياج بنفسك
- ما هي المجاميع الحجر سحقت في الولايات المتحدة الأمريكية
- sand for 8mm to 2 5 mm separation machine
- بهترین سنگ شکن برای سنگ آهن
- كسارة الصخور الصلبة الرخيصة
- مصنع طحن الكلنكر 200 طن يوميا للبيع في الهند
- drawing of sand washing equipment
- بيع كسارات mpact ncrete
- الأعمال محطم آلة طحن g22u الشعبي الطب
- كسارة الفك سحق نسبة
- bauxite jaw crusher for dead materials
- فيديو تأثير محطم رمح العمودي
- المعدات الثقيله كتر حجم 328 جي
- التفريق بين مطحنة الاحتكاك ومطحنة المطرقة
- arequipa scalping screen
- إدخال كسارة مخروطية ذروة
- كيفية الحصول على رخصة لكسارة الحجر في تاميل نادو
- مقلع الرمل والحصى للبيع في ماساتشوستس
- buy wingo 5w led bulb at best price online in
- كريغسليست كسارة العنب
- تاي مصنع مكسور دونغيو
- تهتز بيع الشاشة
- mining omya crushing marble plant
- محاجر الدولوميت كسارة مصر
- كسارة راهانغ Untuk Dijual
- مطحنة الكرة لطحن الزركون
- conveyor belt guidance
- الطحن النهائي للبنتونيت
- مزيج سحق المحمول
- أنواع عملية تصنيع الكسارة الكلية
- gold mininng cake ideas