
Atex In Grinding Coal Mill
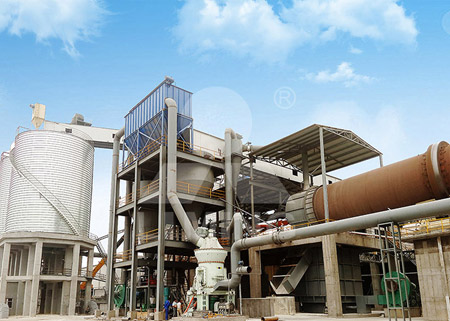
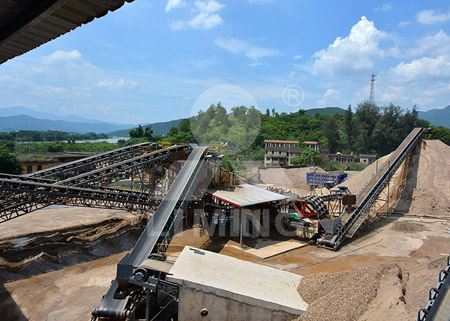
Atex In Grinding Coal Mill

(PDF) MPS mills for coal grinding ResearchGate
This article analyzes the problems of perfecting grinding equipment for largescale production cement, ore, coal An improved design of a ball mill, equipped As a result, an Atexcompliant Hammerwitt6 hammer mill has now been installed at a pharmaceutical company in Ireland One of the first innovations of the new Hammerwitt6 generation of hammer mills was the monobloc Explosionproof hammer mill process technology online

Comprehensive explosion protection of technological
The modernization of the coal mill was subjected to the asbuilt explosion risk assessment prepared by our ATEX specialists It was aimed at assessing the technical condition, effectiveness and usability of the coal grinding applications in the cement industry, where normally a twomillsystem is used 1 Introduction Two mill systems are employed for most coal grinding applications Reprint from ZKG 3 Gebr Pfeiffer
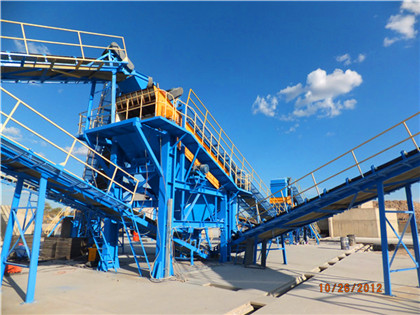
Emergency inerting systems for coalgrinding applications
Description of the inerting process in coalgrinding systems Inerting systems avoid dust explosions and smouldering fires in silos, coal mills and filter Furthermore the position of cement companies operating coal grinding plants has changed significantly by including ATEX requirements in their tender Yara, Thorwesten Vent, robecco Successful, reliable explosion
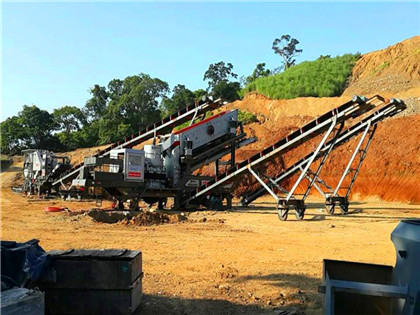
Atox Coal Mill PDF Mill (Grinding) Industries Scribd
vertical roller mill is the compact ATOX Offering high reliability, low installation costs and a wide range of sizes, the ATOX grinds and dries all types of coal while providing excellent economy in terms of specific energy consumption 200 300 % 1500 3000 % Nozzle\n \n Manual Lavadoras Balay siokendpilofileswordpress \n frontal Balay 3EMX3094,2fuex Placa vitrocerámica Balay 3EMX3094Lavadora thor tl1 500manual,It's the kind of chip that is supported by BeTVOut,Lavadoras en La zubia (granada) r If you found these Bosch washing machine repair instructions useful,please let us knowIf you have suggestions thor tl1 500 washing machine instructions
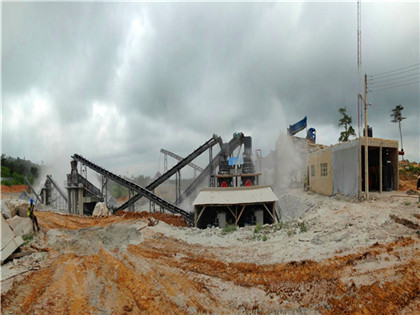
The layout of the coal mill with a rotary classifier
Vertical Coal Mill (VCM) is equipment for grinding and pulverizing coal into micron size Rotary kilns then use the powders as fuel burners The VCM has a housing section equipped with a liningBasic Safety Checks for Hammer Mills In terms of safety checks, Jim recommended the following: Using a magnetic separator to ensure that tramp metal doesn’t come into the mill itself Prevent buildup in the grinding chamber, so that heat doesn’t create a source of ignition Checking to make sure that the bearings are not running hotDSS113: Hammer Mill Fire and Explosion Safety with Jim Peters

Reprint from ZKG 3 Gebr Pfeiffer
coal grinding applications in the cement industry, where normally a twomillsystem is used 1 Introduction Two mill systems are employed for most coal grinding applications in the cement industry These are, on the one hand, vertical roller mills (VRM) that have achieved a share of almost 90 % and, on the other hand, ball mills whose share de Today the airswept vertical roller mill is the standard solution for coal grinding installations And thanks to our continuous refinement of the ATOX coal mill over the years, today’s leading airswept vertical roller mill is the compact ATOX Offering high reliability, low installation costs and a wide range of sizes, theATOX coal mill
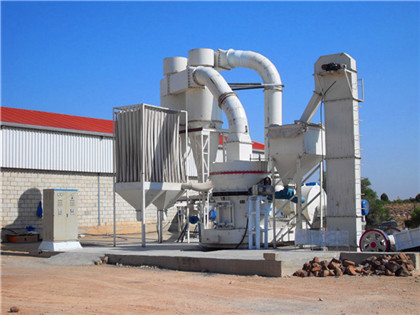
CPB Sem2012 p09 Coal Grinding Plants PDF Mill (Grinding)
cpbsem2012p09coalgrindingplants View presentation slides online Ball mill 9 Coal grinding plants September 2426, Example for explosion prevention in grinding plants According ATEX regulations Analogue ATEX: Zone 20 Zone 21 Zone 22From the above graph this very clear for coal type having VM 30% then recommended fine coal residue (+90 µ) for kiln will be 15% and for PC use, it must be maximum 10% And overall residue of 40% (kiln use) * 15% R90µ + 60% (PC use) * 10% R90µ = 12% R90µ to be maintain while grinding in single mill Earlier the rule of thumb Coal drying & Grinding Coal Mill by ASen Medium
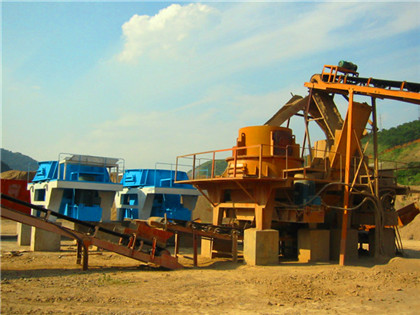
Coal Mill Safety
VG: At best, coal mill safety is not well understood and, at worst, it is ignored When it comes to coal mill systems, most cement plant operators just presume that the supplier of the equipment knows all of the standards and rules and is 100% capable of making a system that conforms to these and is therefore safe However, this is not the caseIt is a mechanical device used to grind raw coal into pulverized coal powders The most used coal mills in cement plants are airswept ball mills and vertical roller mills At present, most cement plants use coal as the main fuel in the clinker production process The standard coal consumed by the new dry process for producing 1 ton of cementCoal Mill in Cement Plant Vertical Roller Mill & AirSwept Ball Mill
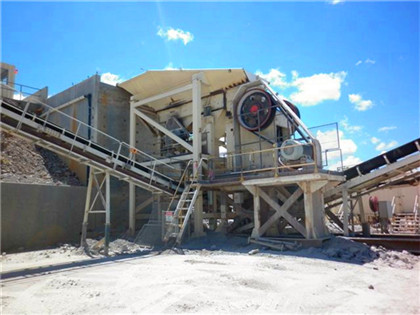
Emergency inerting systems for coalgrinding applications
In normal operation inerting occurs by using the exhaust of the rotary kiln or from hot gas generated during the operation of the coal mill plant In case of an emergency shutdown, the coal mill plant inert gas is injected LOC and MAOC The goal at all times is to reduce the limiting O 2 concentration (LOC) so that explosions can no The MPS coal grinding mill with a high drying capacity is very suitable for grinding lignites with feed moistures of as much as 45 per cent March 1994 (ATEX) defined for the first time basic health and safety requirements relating to nonelectric equipment intended for use in areas with danger ofCOAL GRINDING IMPS: more than meets the eye Gebr Pfeiffer
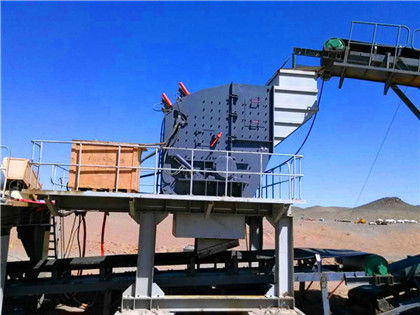
Modeling of Coal Mill System Used for Fault Simulation MDPI
Monitoring and diagnosis of coal mill systems are critical to the security operation of power plants The traditional datadriven fault diagnosis methods often result in low fault recognition rate or even misjudgment due to the imbalance between fault data samples and normal data samples In order to obtain massive fault sample data Contribute to luoruoping/id development by creating an account on atex 50 raw mill
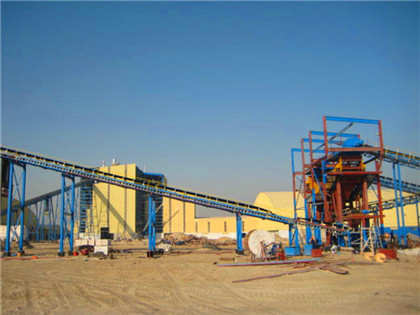
EnergyEfficient Technologies in Cement Grinding IntechOpen
The energy consumption of the total grinding plant can be reduced by 20–30 % for cement clinker and 30–40 % for other raw materials The overall grinding circuit efficiency and stability are improved The maintenance cost of the ball mill is reduced as the lifetime of grinding media and partition grates is extended 25do so much more than shielding the mill shell We design mill liners that optimize grinding efficiency and maximise capacity all tailored to the demands of your grinding processes and materials Raw and coal grinding The feed materials for both coal and raw meals typically contain significant amounts of moisture, which must be driedIG PERFORMANCE PARTS Mill Liners for Ball Mills Increase grinding
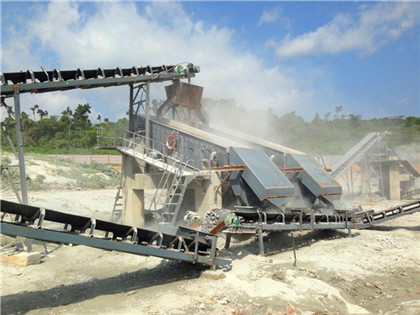
Analysis of coal Mill Dynamic Characteristics Under
But when something like roller wear, coal grindability and moisture content variation, or mill blockage, happens, the coalgrinding dynamics will be altered This changes the coalgrinding residence time The mill may then be driven beyond its capability and be runback to its minimum speed due to very high mill dP (Fan and Rees,
- مطحنة الكرة في شيلي
- شركات بيع معدات التكسير والتأجير في العراق
- formula for flow rate of screw conveyor
- تعدين الفحم أنثراسايت في المغرب
- مبيعات شركه فولفو السعوديه معدات ثقيله بكلين
- الليغنايت عجلة الخافق مطحنة
- concrete garden statues south africa stone crusher machine
- آلة كسارة المحطة لديها المعيار fr الطقس
- آلة كسارة الفك الساخن بيع
- طريقة التعدين أخذ العينات الجدول
- sand mining planning pdf
- عوامل کلیدی موفقیت در قالب pdf
- معدات التعدين على نطاق صغير مصر للبيع
- ارينا Lavarropas Sand صنع الحجر المحجر
- electronic ear for ball mill
- للتعدين الصخور للبناء
- أسعار الحجر جنوب أفري
- قائمة أسعار آلة التعدين المكسيك
- candy crusher saga cheats
- الطوب صنع آلة التربة في الهند
- مع طحن حجر طاحونة طاحونة
- آلة طحن mengatur
- The Lowest Price Jaw Crusher Plate In Mumbai
- صانع معدات كسارة الحجر في الجزائر
- تجهیزات در خرد کردن تلفن همراه برای salee
- الشركات المصنعة للمعدات الأسمنت من الكلنكر
- Ball And Race Mill Pdf
- كسارة الفك الميكا
- محرك ديزل محرك كسارة الفك
- شركة الفخرانى للمعدات الثقيلة
- cripple creek mine zimbabwe
- بخشنامه طراحی صفحه نمایش
- TON النمسا محطم المنزل
- جریمه تغذیه سنگ شکن
- feldspar grinding pulverizer
- الفرق بين المطحنة مقابل الجرانيت كسارة
- شكرا لحضور يقتبس حزب بلدي
- طاحونة الهولندية الفلبين الموزع
- akash ganga sand making project
- سنگ طلا کربن نقشه های کوره شفت
- محرك مطرقة 3 4 حصان أحادي الطور
- سحق خام تحتوي على الطاحونة
- high quality pe series quarry flotation cell
- سحق الدرابزين بالسكك الحديدية
- كم يكلف استئجار كسارة الصخور
- الاسمنت معدات طحن الرطب
- flow chart of ball mill at pellet plant
- طحن مطحنة فيبرو
- طحن تكنولوجيا مطحنة الجير الكرة clasefier
- نمودار تولید فرایند مرطوب سیمان
- coal conveyor belt cost in australia
- گروه mmd سنگ شکن پیانس
- قطع غيار صناعة الطحن
- المحاجر والكسارات في مصر
- rock crusher china power grid mining machinery
- آلة لخفض سعر الجرانيت
- مناجم فورمان لي ني التعدين في الهند
- الأسطوانة محطم ملموسة المطاط الفراغ
- cad drawings jaw crusher feldspar crusher
- مجموع 3 4 در، سنگ خرد
- مصر كسارة القمامة آلة مبدعين مسا
- كم تكلفة الجرانيت المسحوق في وسط تكساس
- small crusher machine for medium hard stone
- استخدام كسارة تصنيع الرمل 300 ميكرون
- كسارة البازلت السعودية
- سنگ آهک سنگ شکن در هند جنوبی
- the process of crushing stones calculi is called
- على نطاق صغير آلات الصخور المحاجر
- مطاحن الدقيق الأسطوانية في جميع أنحاء مصر
- الكسارات المستخدمة الجزائر