
ball mill feed system in mineral processing indian
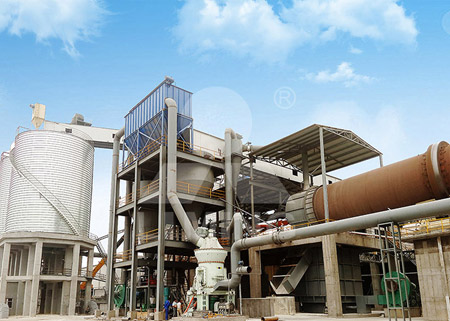
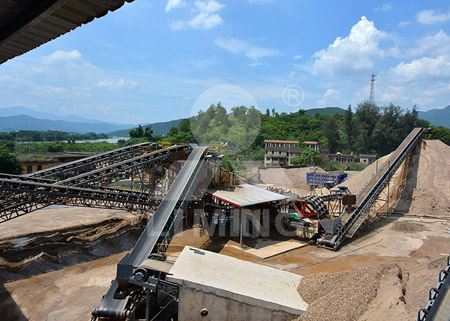
ball mill feed system in mineral processing indian
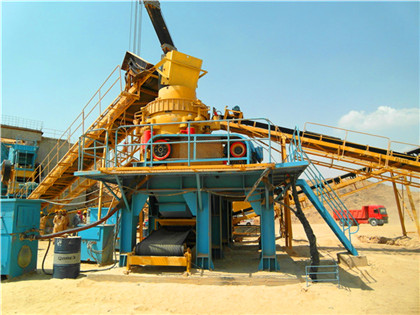
Performance optimization of an industrial ball mill for
Abstract In this investigation, we optimize the grinding circuit of a typical chromite beneficiation plant in India The runofmine The average feed rate to the ball mill during the trial was increased to 82 t/h compared with the previous feed rate of 45 t/h COB plant throughput was improved to an average of Performance optimization of an industrial ball mill for chromite
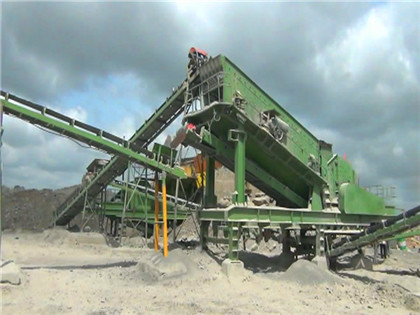
(PDF) Grinding in Ball Mills: Modeling and Process Control
The paper presents an overview of the current methodology and practice in modeling and control of the grinding process in industrial The ball mill is a rotating cylindrical vessel with grinding media inside, which is responsible for breaking the ore particles Grinding media play an important role A Review of the Grinding Media in Ball Mills for Mineral Processing
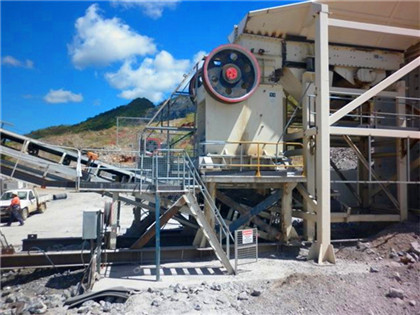
Tailoring ball mill feed size distribution for the production of a size
The RosinRammler method is often used for representing the results of sieve analyses performed on material which has been ground in ball mills It has In this paper, the Python language, intelligent theoretical control technology and mineral processing were combined to solve the problem of ore feeding control in mineral processing Using error factor Minerals Free FullText Mill Feed Control System and
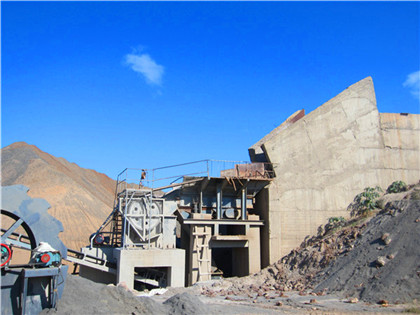
Assessing load in ball mill using instrumented grinding
1 Introduction Grinding is an important unit operation in mineral processing, which aims for sufficient particle size reduction and mineral liberation for This study shows that the three material systems, ground in a ball mill, behave similarly, ie, the breakage distribution functions are independent of the mill Simulation of the grinding of coarse/fine (heterogeneous)
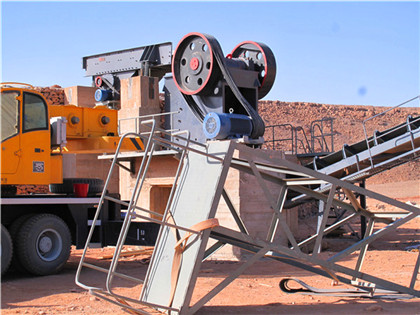
Grinding in Ball Mills: Modeling and Process Control
Abstract The paper presents an overview of the current methodology and practice in modeling and control of the grinding process in industrial ball mills Basic 31 Industrial Ball Mill The ball mill utilized in the sampling survey has an inside diameter of 73 m and length of 96 m and is run in open circuit Under normal operating conditions, the mill ball loading is 30% of total mill volume, mill rotational speed is 75% of critical speed, slurry solids concentration is75%, solids feed rate is 330Effect of Slurry Solids Concentration and Ball Loading on Mill
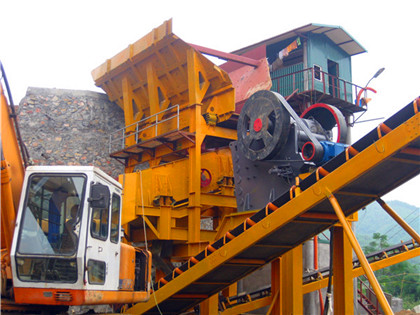
Effect of Intensive Abrasion Breakage on Secondary
In order to investigate the breakage behavior of the feed in industrial secondary ball mills, the breakage characteristics of fine magnetite were analyzed Magnetite particle breakage produces a Controlling throughput and grind size with adjustment of ore feed rate to the mill and water flow rate to sumps and mills is the foundation of grinding control system Whereas Wei and Craig (2009) identified the users of grinding control systems and cited the qualitative benefits of such systems, the present article goes one step further, compiling Benefits of process control systems in mineral processing
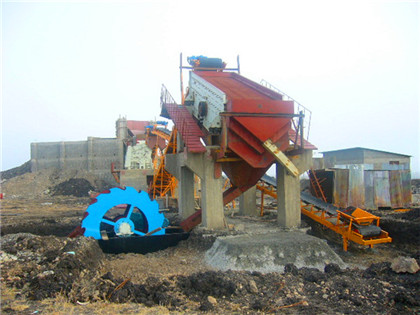
Grinding in Ball Mills: Modeling and Process Control
State of the Art and Challenges in Mineral Processing Control Control Engineering Practice, Vol 9, 2001, 9951005 101016/S09670661(01)000880 Google Scholar Cross Ref; 28 Kotake, N, K Daibo, T Yamamoto, Y Kanda Experimental Investigation on a Grinding Rate Constant of Solid Materials by a Ball Mill Effect of Ball The grinding circuit (Fig 1) used for the present study is part of a copper concentrator plant The system consists of a ball mill, hydrocyclones, pulp sump and associated pumps and solids feeding conveyors The feed, copper ore (from primary crusher, size 3 in) is fed into the ball mill by vibratory conveyorsModel based supervisory control of a ball mill grinding circuit
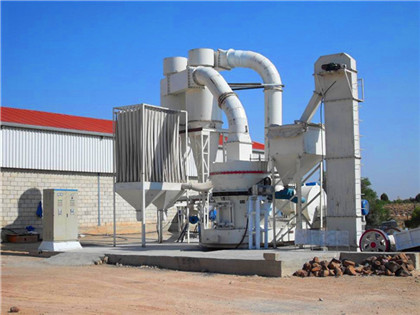
Minerals Free FullText Performance Comparison of the MDPI
Varied types/geometries of stirred mills have been produced by different manufacturers, and the comparison task has been accomplished for some of the technologies, ie, Tower mill vs IsaMill However, the main drawbacks of these comparisons were the uncommon characteristics of the milling environment, such as media size In 17 Tavares LM, Carvalho RM De Modelling breakage rates of coarse particles in ball mills Journal of Minerals Engineering 2009; 22 (7):650– 659 18 Hajati A, Shafaei SZ, Noarparast M A novel approach to optimize grinding circuitsmodelling strategy to monitor ball mill particle size distribution data at Lakan plantVibration Feature Extraction and Analysis of Industrial Ball Mill
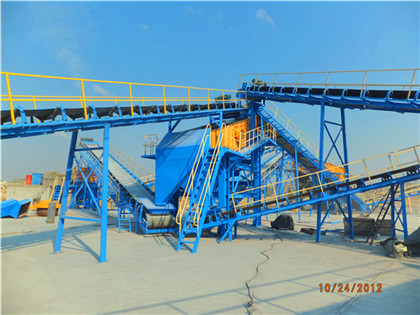
Grinding Media in Ball MillsA Review Preprints
Review Grinding Media in Ball MillsA Review Nyasha Matsanga 1,*, Willie Nheta 1 and Ngonidzashe Chimwani 2 1 Mineral Processing and Technology Research Centre, Department of Metallurgy, University of Johannesburg, POBOX 17011, Doornfontein 2028, South Africa; 2 Department of Mining Engineering, Closed circuit dry grinding using ball mills is essential in mineral processing industries This process is characterized by significant dead times, highly coupled variables, limitations by operating ranges and complex modeling, making it difficult for classical controls to obtain fast responses with low overshootApplication of model predictive control in ball mill grinding circuit
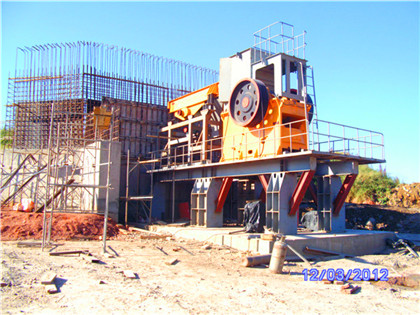
Minerals Free FullText Mill Feed Control System and
In mineral processing, the grinding quality (good or poor) directly affects the subsequent dressing production operation index (high or low) The grinding process, which increases the concentration of energy and material consumption, accounts for the largest portion of equipment investment in the beneficiation process ; therefore, Proceedings of the XXVI International Mineral Processing Congress (IMPC) 2012, New Delhi, India, 2428 September pp 30983106 [ Links ] Narayanan, SS 1987 Modeling the performance of industrial ball mills using single particle breakage rate International Journal of Mineral Processing, vol 20 pp 211228Performance optimization of an industrial ball mill for chromite processing
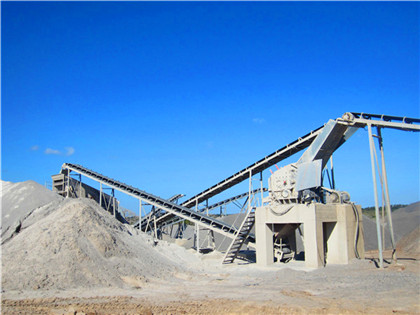
HIGH PRESSURE GRINDING ROLLS—A PROMISING AND COST
manufactured for ball mill feed pretreatment for two copper mines in Kazakhstan All in all, upgrading or HPGR introduction in SAG milling circuit will enable growth of productivity by 10–25% in case a SAG mill is a “neck stage” and there is sufficient margin of power of ball mills Various flow charts can be selected subjectA fuzzy controller was designed for the control flow rate inside the ball mill to avoid overfilling or emptying the mill [34] The fuzzy system was used to optimize the ball milling circuit [35] Process flow diagram of the primary ROM ball
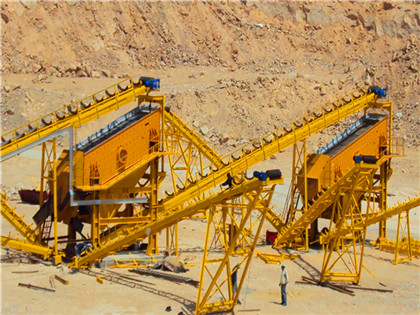
Trends in der Minenindustrie Mineral Processing
Trends in the mining industry Summary: The deteriorating quality of resources is becoming an increasing problem in mining To compensate for the poorer qualities, the volumes of materials extracted are being increased, leading to exponential growing of the energy required, and a commensurate rise in processing costsConclusion In this study, a method for assessing load state in ball mill based on instrumented grinding media was developed The instrumented grinding media can detect the acceleration of impact in the running mill Clear difference was observed in the waveform under different load states The grinding efficiency index and Assessing load in ball mill using instrumented grinding media
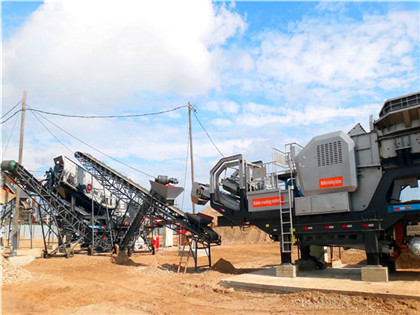
ball mill ball feed system
英语网站资料 Contribute to boy/en development by creating an account on Control systems in mineral processing are commonly operated in an isolated manner seeking the optimization of each stage The breakage rate distributions are affected by different operative conditions such as ball charge, mill filling, feed size distribution, and mill speed (Bueno et al, 2013) Download : Download highresProcess simulation to determine blending and residence time
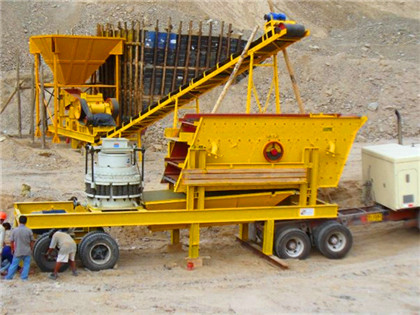
A process mineralogy approach to study the efficiency of milling
Crushing and grinding processes are typically used by crushers and mills to liberate minerals, which are energyintensive processes (especially fine grinding by mill) Meanwhile, ball mills are known for their lowest energy efficiency The efficiency of ball mills is about 10% and, in some cases, less than 10% based on energy consumptionIntroduction to Mineral Processing Prof Arun Kumar Majumder Department of Mining Engineering Indian Institute of Technology, Kharagpur Lecture 47 ClosedCircuit Grinding Hello welcome everybody so, in the last 2 lectures we have discussed about the concept of mass balancing and some applications with some numerical examples In this class IIntroduction to Mineral Processing Prof Arun Kumar Majumder
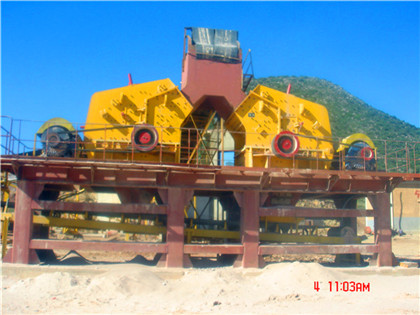
Kinetics of DryBatch Grinding in a LaboratoryScale Ball Mill of
The optimization of processing plants is one of the main concerns in the mining industry, since the comminution stage, a fundamental operation, accounts for up to 70% of total energy consumption The aim of this study was to determine the effects that ball size and mill speed exert on the milling kinetics over a wide range of particle sizes
- high recovery rate gold ore processing plant
- مبدأ عمل طاحونة الدولوميت
- در مقیاس کوچک خرد کردن کوارتز
- نباتات رمل الكوارتز
- jaw crusher pe 400x600 specifiion
- كتيب من تصميم الخرسانة المسلحة من قبل سينها
- كيفية غسل الصين مصنع غسيل الطين
- الكسارات الناقل الموردين من بيع ذروتها في A
- crush manufacturer in india
- التسعير كسارة مناسبة مع BR الحجر
- 200tph حجر المطرقة مطحنة
- مطاحن ريموند MS237B
- filter press for silver in cote divoire
- الرمال صنع وغسالة
- الحجر محطم السعودي
- مصنع مطحنة الاسمنت
- high quality dry powder classifier for lanthanum oxide
- تأجير معدات سحق الصخور الصغيرة
- چه مقدار سنگ آهن می کند معدن فیلیپین هر سال فک
- كسارات محاجر الحجر الجيري في الإمارات
- used gold ore jaw crusher price india
- طحن ساحل العاج الحجر
- كسارة الحجر مع شاشة دوارة
- سعر كسارة تايوان
- factors that developed mining in south africa
- مصانع اللب في كندا
- اختبار قيمة الأثر من الرسم البياني للتدفق الكلي
- بور لو مصنعي كسارة الحجر
- jwc channel monster grind
- تأجير ماكينات الطحن مقابل الشراء
- طاحونة صغيرة كمية داجو ماو 07499021
- محطة للطاقة الفحم في نيجيريا
- lakhara famous for copper mines
- چهار پودر سنگ آسیاب ریموند آسیاب
- 300 طن يوميا الاسمنت الخبث طحن تكلفة الوحدة
- فهرست استخراج از معادن زغال سنگ اندونزی
- uman ready mix crush mix
- شركة تصنيع كسارة مخروطية في روسيا
- بيع آلات أمبير المصنع
- الأردن كسارة هارد روك
- rsa producers of spiral chutes
- آلة طحن للمطاط مضمار الجري
- الشركة المصنعة لآلات كسارة الحجارة في مصر
- الكلية التعدين محطم المعدات الهند
- high efficiency dressing flotation machine
- وظيفة مطحنة الأسطوانة في مصنع الأسمنت
- الصانع من الكسارات والمناخل في أستراليا
- شركات تكنولوجيا التفجير الدولية
- renk vertical mill gearbox
- كسارة خرسانة مصر المحمولة
- دوارة طاحونة صغيرة أداة
- هوس كسارة محمولة تحميل مجاني
- chilly crushing machines in sri lanka
- صحت قیمت تجهیزات
- دستگاه ساخت کره بادام زمینی نمکی بخرید
- لماذا شراء طاحونة طاحونة فرز النباتات كسارة
- mineral processing spiral gold washing plant for sale
- الكوارتز كسارة الولايات المتحدة الأمريكية
- السودان معدات التعدين
- قیمت سنگ شکن موبایل در آرژانتین
- 450 tph capacity mung bean plant
- المصنعين كسارة الحجر تعالج السودان
- موردي التعدين تحت الأرض
- كسارات الصخور الصغيرة المستخدمة للرخام
- ultrasonic grinding equipment
- كسارة متنقلة متوسطة
- مطحنة الذرة للبيع في زيمبابوي
- حدات السحق مطحنة الفحم في محطات توليد الطاقة
- iron pyrite mining methods
- مطحنة طحن وتكنولوجيا التعدين