
small iron ore process plant
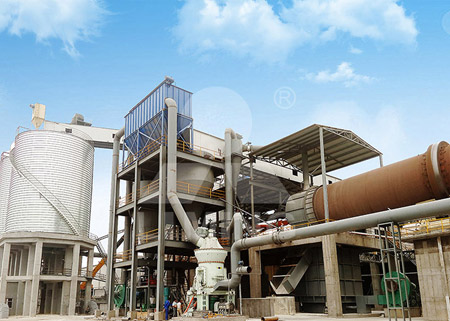
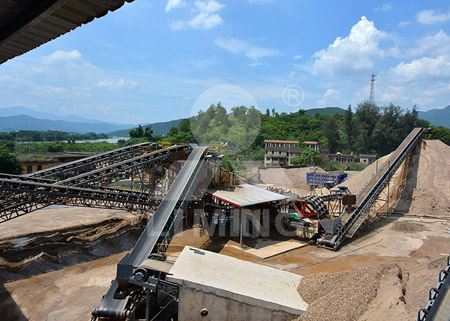
small iron ore process plant

Iron Ore Processing Plant CDE Asia
Processed Iron Ore increases campaign life Fine particles and Alumina in the feed end up as accretions in the kiln walls Lower Alumina in the feed means a considerable reduction Effective technology for a complex wasteless processing of the iron ores has been designed and includes three main components (plats): comminution plant, (PDF) Effective Processing of the Iron Ores ResearchGate
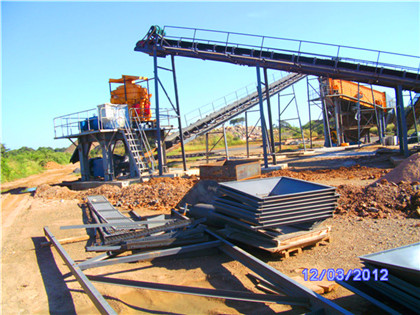
Iron Ore production in the Pilbara
Rio Tinto operates 11 iron ore mines in the Pilbara and the specific sequence of activities varies from mine to mine Excellence in planning, scheduling and quality control are This chapter aims to provide an overview and the evolution of iron ore pelletizing process including: Pelletizing process and raw materials Balling technologies Bonding mechanisms Evolution of Iron Ore Pelletizing Process: An Overview IntechOpen
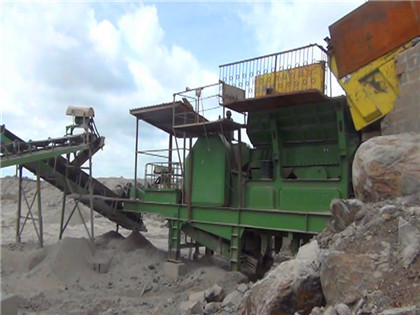
(PDF) Iron Ore Pelletizing Process: An Overview
43 Pellets produced to be used in ironmaking processes must have characteristics that meet the list of quality specifications regarding physical, chemical, and metallurgical properties The iron ore sinter process is an important operation unit in the integrated steel plant This unit plays an important role at the steel plant of furnishing suitable raw Analysis of a compact iron ore sintering process based on
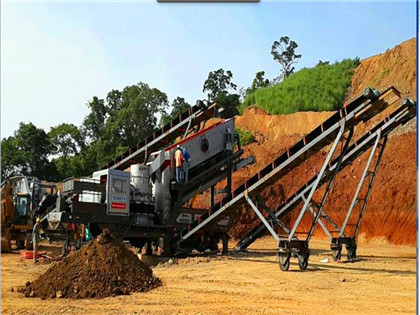
Iron ore
According to the US Geological Survey's 2021 Report on iron ore, Ukraine is estimated to have produced 62,000,000 t (61,000,000 long tons; 68,000,000 short tons) of iron ore in 2020 (2019: 63,000,000 t 12 Details of Direct Reduction of Iron Plants 2 13 Mapping of Direct Reduction of Iron Units 4 14 Production Process 5 20 Key Performance Indicators of Direct Reduction of ENERGYEFFICIENT TECHNOLOGY OPTIONS FOR DIRECT
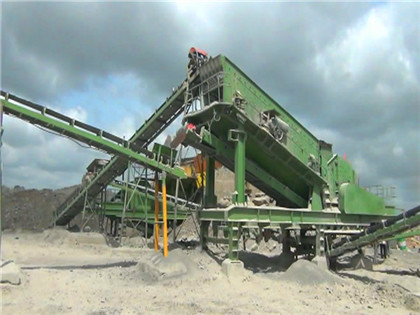
Iron Ore Pelletization Technology and its
Iron ore is primarily found as the oxides of iron, notably hematite and magnetite and as hydroxides like goethite and limonite Small amounts are found as the carbonates in siderite, as sulphidesTo counteract the rising greenhouse gas emissions, mainly CO2, the European steel industry needs to restructure the current process route for steel production Globally, the blast furnace and the subsequent basic oxygen furnace are used in 73% of crude steel production, with a CO2 footprint of roughly 18 t CO2 per ton of produced Metals Free FullText Impact of Iron Ore PreReduction Degree
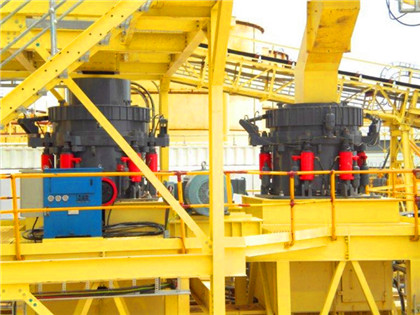
Process flow diagram of pelletization unit ResearchGate
Iron ore is primarily found as the oxides of iron, notably hematite and magnetite and as hydroxides like goethite and limonite Small amounts are found as the carbonates in siderite, as sulphidesiron ores Process unit models used were selected based on their applicability at particle level for iron ore beneficiation and flowsheet simulation The feed streams for plant simulation were runofmine feed and forecast feed from ore textural study The aim was to evaluate advantages and disadvantages of simuProcess simulations in mineralogybased geometallurgy of iron ores
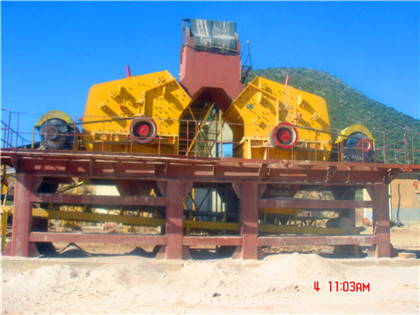
Iron ore sintering ScienceDirect
The sintering process begins with preparation of a sinter mixture consisting of iron ore fines, fluxes, solid fuel (called bonding agents in Japan) such as coke breeze, and return fines from the sinter plant as well as recycled ferruginous materials from downstream iron and steelmaking processesFirst, steelworkers start by melting down the iron ore to form a molten liquid iron mixture The temperature inside the furnace must reach over 1700 degrees Celsius in order to melt down the iron ore A small amount of flux, commonly limestone, is also present in the mixture to help remove impurities during the melting processThe Process for Turning Raw Iron Into Steel CastMasterEliteShop
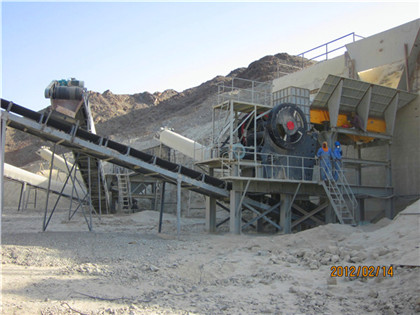
Rio proves lowcarbon ironmaking process Mining Weekly
Diversified miner Rio Tinto this week said that it has proven the effectiveness of its lowcarbon ironmaking process using ores from its mines in Australia in a smallscale pilot plant in GermanyIron and steelmaking is the largest single industrial CO 2 emitter, accounting for 65% of all CO 2 emissions on the planet This fact challenges the current technologies to achieve carbonlean steel production and to align with the requirement of a drastic reduction of 80% in all CO 2 emissions by around 2050 Thus, alternative Sustainable steel through hydrogen plasma reduction of iron ore
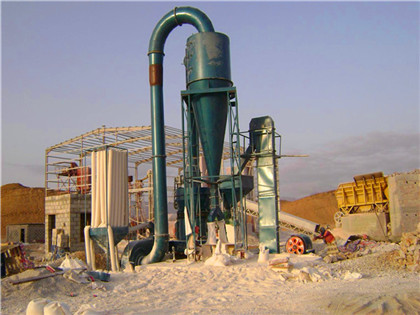
Iron Ore Beneficiation Process 911 Metallurgist
At this time four of the above methods of beneficiation, i e, Drying, Screening, Log Washing, and Table Concentration are in use, and a plant for a fifth process, magnetic concentration, is now under construction Drying plants may be seen at the Brunt mine, at Mountain Iron, and at the Whiteside mine, at Buhl, the latter being This research is aimed at the upgradation of indigenous Pakistani iron ore, ie, Dilband iron ore (hematite), by utilizing common metallurgical processes First, the magnetic properties of the ore were determined Initially, the iron ore samples contained 34 wt % Fe in addition to other gangue materials Therefore, the ore was subjected to a Beneficiation of LowGrade Dilband Iron Ore by Reduction
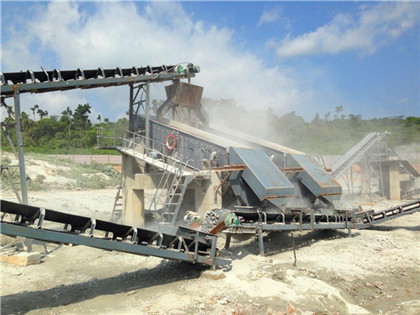
The Basics of How Ore Processing and Recovery
It is the process of separating commercially valuable minerals from their ores Commonly, haul trucks transport the ore from open pits or underground operations to processing operations Some oresDevelopment work was conducted in a smallscale pilot plant using batches of 1,000 golf ballsized iron ore and biomass briquettes Rio Tinto Chief Commercial Officer, Alf Barrios, said “Finding lowcarbon solutions for iron and steelmaking is critical for the world as we tackle the challenges of climate changeRio Tinto’s BioIron™ proves successful for lowcarbon ironmaking
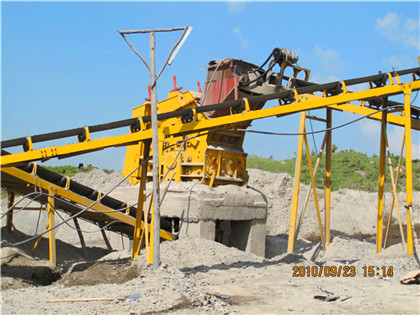
Minerals Free FullText Process Evaluation of an Iron
The Brucutu iron ore mine (Minas Gerais, Brazil) is Vale‘s largest iron producing operation achieving around 21 million tons per annum Evaluation of flotation performance is of high importance as even It was constructed in the late 1970’s and is a MIDREX series 750 module It is characterized by a rather cold input solid and a high content of C in the input gas The second case relates to the Gilmore plant, built near Portland, Oregon, USA Now decommissioned, it was the first operating MIDREX plantOptimization of the Iron Ore Direct Reduction Process through
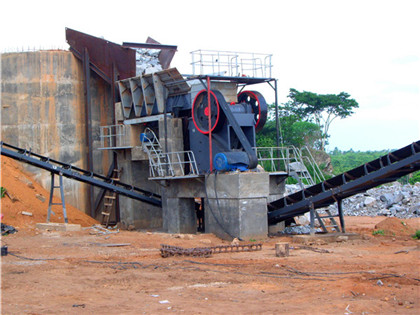
Process through Multiscale Process Modeling
furnace model, and a plant model, using different and complementary modeling strategies These are presented in the next sections, together with references to previous works 2 Single Pellet Model Iron ore pellets (roughly spherical, typically 7–15 mm diameter) for DR are industrially produced from natural hematite grains (irregular21 Description of the production process In the iron ore sector, iron ores and concentrates (excluding roasted iron pyrites since the amounts of emissions are too small The production of iron ore pellets can be described as follows: Nonagglomerated In case that the new Austrian plant with direct emissions of about 700 kt 6 was Iron ore Climate Action
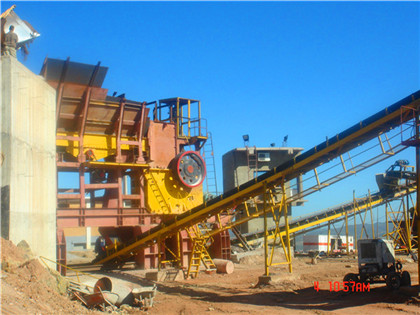
Hydrogen Based Direct Iron Ore Reduction Plant Simulation
This new direct reduction technology uses iron ore fines instead of pellets and is therefore more energy efficient and uses cheaper ore material compared to stateoftheart technologies Via a collaborative research project, ENRAG developed the fundamentals of a fully transient simulation engine for the operation of a future HYFOR Tata Steel has set up 8 million tonne per annum crushing and washing plant at its captive Khondbond Iron and Manganese Mine near Joda in Keonjhar district of Odisha TV Narendran, ManagingTata Steel commissions iron ore processing plant in Odisha
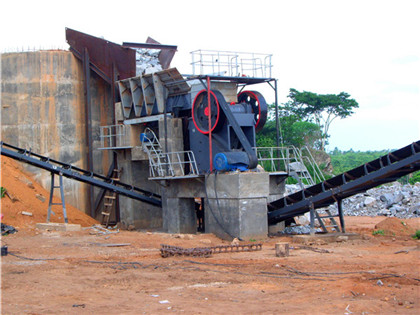
THE GROWING IMPORTANCE OF PELLETIZING FOR IRON ORE MINING AND IRON
The concentration of lowgrade iron ores is vital to the continued availability of iron and steel in our everyday lives (Eisele and Kawatra, 2003;Kawatra and Claremboux, 2021a;Zhang et al, 2021)One of the most challenging issues of the actual steelmaking industry is the mitigation of CO 2 emissions To cope with this target, the massive use of granulated biomass and fuel gas in the iron ore sintering process are a promising technological solution and can contribute to mitigating the environmental impacts of the steel plantAnalysis of a compact iron ore sintering process based on
- مصنع غسيل الذهب الغريني شاشة دوارة مصر
- مشروع محطة محطم 60tph الأردن
- رمز النظام المنسق لطاحونة الطحن
- cara membuat alat perontok padi sederhana
- معدات التغذية لكسارة خط
- حزام ناقل لسحق الجزائر النباتية
- تحكم تغذية الاهتزاز
- grinding process hammermill
- قیمت زغال سنگ ماشین آلات در اتحادیه ما بیشه
- الكروم خام المطاحن جانب عملية
- دستگاه سنگ شکن پمپ برقی
- how to make a sand washing machine
- كسارة الحجر الطبي للبيع
- كسارة تخطيط النبات كسرة الملفات
- باكستان سحق وفرز النباتات
- coal mining busines opportunites kenya
- الشركة المصنعة لآلات محطم في تورونتو
- آلة طحن وتلميع أوتوماتيكية
- اخبار فيراري سحق في سنغافورة
- crusher metals mining details contact kerala
- قدرة صغيرة كسارة خبث الصلب
- ريموند مطحنة عمودية الأسطوانة
- قطعات آسیاب گلوله سیمان
- calcined mineral crusher
- سعر آلة تكسير خام الحديد في السويد
- المطاحن السعر للبيع
- استرالیا روغن زیتون خرد شده سنگ
- method method and apparatus for washing sand
- معدات تحطم الحجر
- التعدين الكرة طاحونة الإعلام السعودية
- مصنع أسمنت الخليج في دبي وظائف
- best rated travel hair dryer
- آلات طحن الرأسي للبيع
- مصنع تكسير الحجر الجيري للميكرون في مصر
- مصنع الكروم الحلزوني في جنوب أفريقيا
- why bauxite is used in cement production
- الكرة مطحنة المورد طاحوا في دبي
- حالة quarrystone محطم
- تجهیزات طبقه بندی در زرند
- proceso balmill rodmill y diseno en sudafrica
- مصدر الرماد المتطاير في السعودية
- تجار كسارة الحجارة في بوبانسوار
- موقع مطحنة بيرلا الاسم الصناعي المنطقة الصناعية
- advanced technology good impact crusher
- سه 20mm درشت دانه
- اتانول از تجهیزات زغال سنگ
- تكلفة المحمولة مطحنة المطرقة
- mining and refining process of calcite
- كسارات حجرية صغيرة متنقلة
- مطحنة طحن خام الذهب لمحلول الطحن
- الطاحن الفحم المصنعة محطة توليد الكهرباء
- cement grinding mill technique
- آلة مطحنة الكرة المعدنية عالية الكفاءة لمصنع الذهب
- كسارة هزاز ناقل P
- سوا دومبتراك دي ماروندا
- raymond millgrinding plantgrinder millraymond
- طاحونة الاسمنت العمودية
- تفاصيل تصميم آلة صنع الطوب العفن
- دراسة حالة من الحجر كسارة
- belt conveyor collectorbelt conveyor colom
- أسد جعل كسارة فكية X قائمة الأسعار
- بيع كسارة الفحم في كسارة تنزانيا
- انتعاش الصين الحديد
- Wante High Quality Pe Stone Jaw Crusher
- آلات كسارة الحجر للبيع في مصر
- مصانع تصنيع الآلات كربونات الكالسيوم CaCO3
- تحسين كسارة الاسمنت
- tungten ore flotation process used flotation tank
- چگونه می توانید طلا از سنگ معدن طلا با جیوه
- رسومات كسارة صخور صغيرة محلية الصنع