
iron blast furnace process
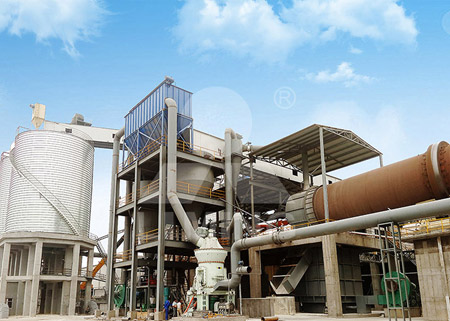
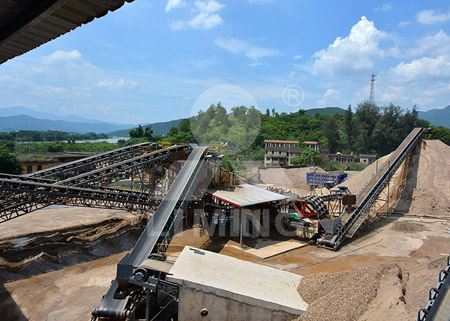
iron blast furnace process
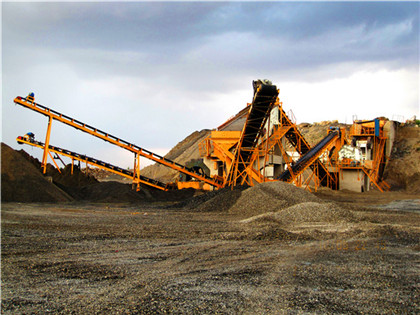
Blast furnace Definition, Temperature, Diagrams, & Facts
Blast furnace, a vertical shaft furnace that produces liquid metals by the reaction of a flow of air introduced under pressure into the bottom of 15 行The blast furnace (BF) ironmaking process is currently the dominant process for providingBlast Furnace Ironmaking an overview ScienceDirect

Steel Production American Iron and Steel Institute
The blast furnace is the first step in producing steel from iron oxides The first blast furnaces appeared in the 14th century and produced one ton Modern furnaces are equipped with an array of supporting facilities to increase efficiency, such as ore storage yards where barges are unloaded The raw materials are transferred to the stockhouse complex by ore bridges, or rail hoppers and ore transfer cars Railmounted scale cars or computer controlled weight hoppers weigh out the various raw materials to yield the desired hot mBlast furnace
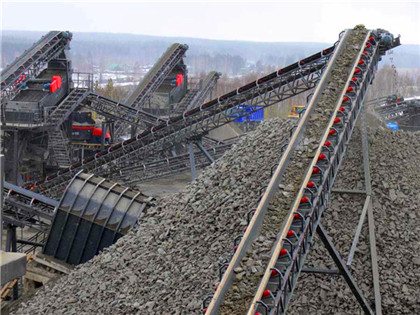
Blast Furnace Ironmaking ScienceDirect
Chapter 1 The Iron Blast Furnace Process Pages 118 Abstract The blast furnace is the most prolific of the metallurgical furnaces operating in the world In 2016, over 1 Improvements in the process over many centuries eventually led to the mass production of iron and to the industrial revolution The reactions of the blast The Iron Blast Furnace: A Study in Chemical Thermodynamics
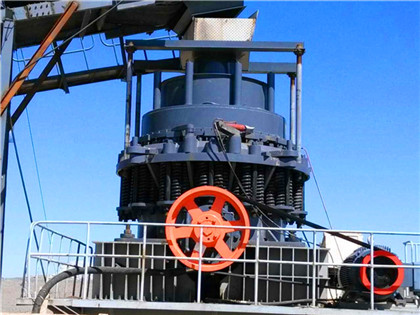
Ironmaking Process an overview ScienceDirect Topics
The ironmaking process in the blast furnace is a heat and mass transfer process, and the furnace can be divided into different zones according to physical and The first step in the metallurgy of iron is usually roasting the ore (heating the ore in air) to remove water, decomposing carbonates into oxides, and converting sulfides into oxides The oxides are then reduced in a blast 233: Metallurgy of Iron and Steel Chemistry LibreTexts
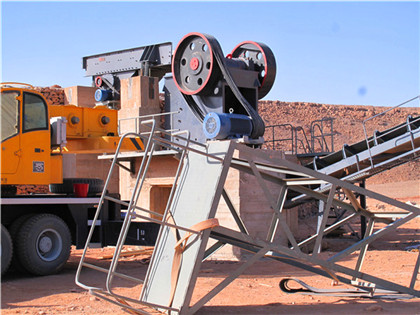
Recent developments in blast furnace ironmaking
This chapter discusses the blast furnace (BF) iron making The chapter first gives information about fundamentals and historical development of BF technology In the blast furnace process, ironbearing materials (eg lumps iron ore, sinter/pellets, mill scale and steelmaking slag), coke (fuel as well as reducer) and flux Blast Furnace Process SpringerLink
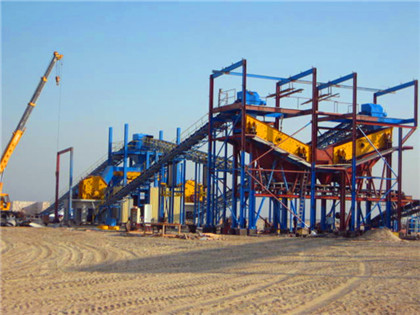
Pig Iron Production Blast Furnace Route Metallics
Blast Furnace Process The blast furnace is a countercurrent gas/solids reactor in which the descending column of burden materials [coke, iron ore and fluxes/additives] reacts with the ascending hot gases The process Iron is mainly extracted from hematite (Fe 2 O 3) and magnetite ores Natural or direct shipping iron ores contain between 5070% iron and can be fed directly into the blast furnace Fe 3 O 4 Ironmaking 101 From Ore to Iron with Blast Furnaces
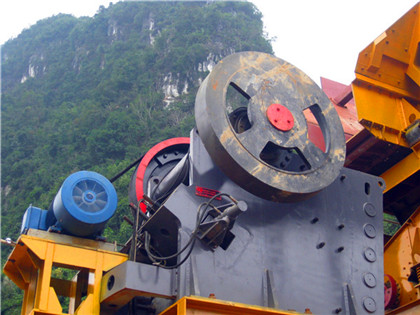
iron and steel chemguide
Steelmaking: the basic oxygen process Impurities in the iron from the Blast Furnace include carbon, sulphur, phosphorus and silicon These have to be removed Removal of sulphur Sulphur has to be removed first in a The blast furnace process can be briefly described as follows Iron oxides, flux agents, and metallurgical coke are added to a skip car at the stock house The skip car ascends through a skip bridge to the top of the blast furnace where it is emptied A system of double bells is used to charge the blast furnace to minimize the escape of blastBlast Furnace Process an overview ScienceDirect Topics
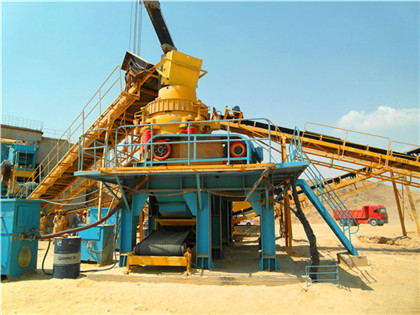
233: Metallurgy of Iron and Steel Chemistry LibreTexts
The first step in the metallurgy of iron is usually roasting the ore (heating the ore in air) to remove water, decomposing carbonates into oxides, and converting sulfides into oxides The oxides are then reduced in a blast furnace that is 80–100 feet high and about 25 feet in diameter (Figure 2332 233 2) in which the roasted ore, cokeIn the blast furnace process, ironbearing materials (eg lumps iron ore, sinter/pellets, mill scale and steelmaking slag), coke (fuel as well as reducer) and flux (limestone and/or dolomite) are charged by the skip Blast Furnace Process SpringerLink

Blast Furnace an overview ScienceDirect Topics
Blast Furnace Blast furnace gas is produced during the iron oxide reduction in blast furnace iron making in which iron ore, coke and limestone are heated and melted in a blast furnace and is an indigenous process gas of the steelworks industry (Pugh et al, 2013) From: Fuel Flexible Energy Generation, 2016 Related terms: Energy EngineeringThe smelting of iron ore into metallic iron was first accomplished by primitive blast furnaces approximately three thousand years ago Improvements in the process over many centuries eventually led to the mass production of iron and to the industrial revolutionThe reactions of the blast furnace involve 1) combustion of the fuel The Iron Blast Furnace: A Study in Chemical Thermodynamics
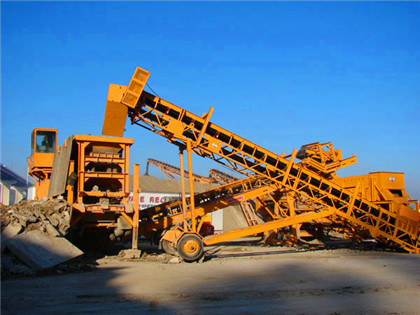
Making iron & steel blast furnace ArcelorMittal
Before iron ore can be used, oxygen must be removed from it Known as ‘reducing’, this can be done either in the blast furnace, where hot air is injected into a continuous feed of coke, sinter and lime, or by the direct reduced iron (DRI) process The result from both is liquid iron, which is then transported to the basic oxygen furnace The blast furnace process The arrival of blast furnaces, however, opened up an alternative manufacturing route; this involved converting cast iron to wrought iron by a process known as fining Pieces of cast iron were placed on a finery hearth, on which charcoal was being burned with a plentiful supply of air, so that carbon in the iron was removed by oxidation, leaving semisolid Iron processing Definition, History, Steps, Uses, & Facts
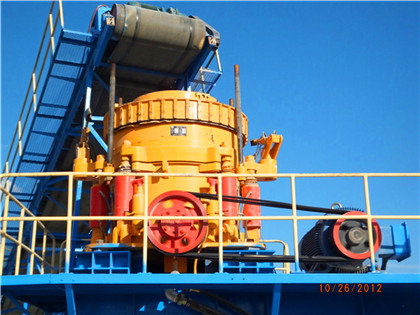
Effect of H2 on Blast Furnace Ironmaking: A Review
and carbon emissions of the iron and steel industry In the process of blast furnace (BF) smelting, about 30% of iron oxides are reduced by CO, about 10% by H2, and the rest by carbon [1] The purpose of hydrogenrich smelting in BF is to increase the proportion of H2 reduction so as to reduce the consumption of carbon reductantIn the integrated steelmaking route, iron ore containing ferrous oxides is converted to metallic iron inside the blast furnace via a chemical process called ‘reduction’ Coal in the form of metallurgical Pathways to decarbonisation episode two:

NPTEL :: Metallurgy and Material Science NOC:Ironmaking and
Modules / Lectures Intro Video WEEK 01 Lecture 01: Introduction Lecture 02: Various Routes of steelmaking Lecture 03: The Iron Blast Furnace Lecture 04: Thermodynamics of BF ironmaking Lecture 05: Thermodynamics of BF Ironmaking (continued) WEEK 02Blast furnaces were a more complex and expensive method of producing iron than bloomeries, but they could produce iron in much greater amounts, could use ores that the bloomery process couldn’t, and produced a liquid, castable iron, more suitable for producing guns than wrought ironThe Blast Furnace: 800 Years of Technology Improvement
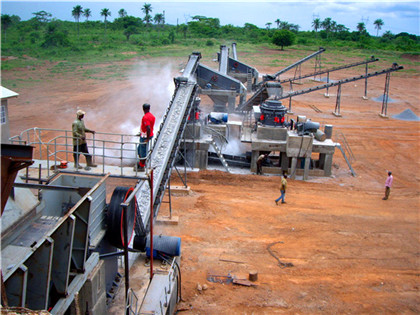
THE FINEX® PROCESS ECONOMICAL AND ENVIRONMENTALLY
blast furnace hot metal quality • Valuable export gas can be utilized for different purposes (eg power generation, DRI production, chemical products) • Commercial proven alternative iron making process to the blast furnace •carbon monoxide and hydrogen This is due to the high Brownfield application at integrated steelThis work represents an extended abstract of a study presented at the PRES 2016 conference Despite the fact that alternative processes such as Corex® and Finex® have already been established on industrial scale, the blast furnace route continues to be the most important process used to produce pig iron Due to its importance, a Development of a Blast Furnace Model with Thermodynamic Process
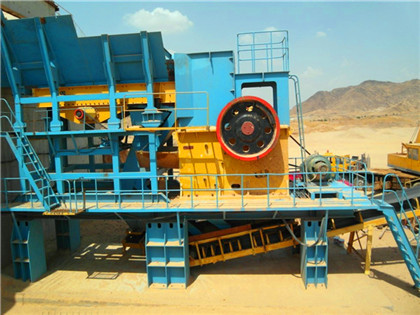
Iron: From mythical to mundane The Roots of Progress
17thcentury waterpowered blast furnace Wikimedia Once a furnace is big enough, the fire burning long and hot enough, something new and different happens to the iron: some of it melts Liquid iron running out of the furnace had a different character than the solid bloom that collected at the bottom: it was brittleMathematical Model for an Iron Blast Furnace wher e, T2 i s t he t emp eratu re at w hich th e r eact ion take s p lace and T1 is the standard tem perat ure of 298K Fi gure 3 show s t he diff erentStatic Heat Energy Balance Mathematical Model for an Iron Blast Furnace
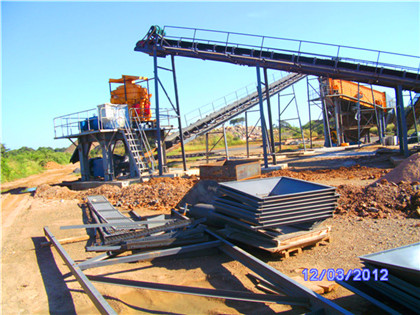
Blast Furnace Ironmaking SpringerLink
The smelting process of blast furnace is carried out in the shaft furnace of a closed countercurrent reactor and heat exchanger The complex physical changes and chemical reactions are completed in the process of the countercurrent movement of the charge and gas in which the raw materials containing iron oxide (sinter, pellets, etc), 21 Introduction of Modern Ironmaking Technology Historically, iron was produced in Japan by a smallscale ironmaking method called the tatara 92) process with iron sand as the main raw material Use of the blast furnace process 93) began on December 1, 1857 following the construction of a westernstyle blast furnace in Kamaishi by T Oshima In Ironmaking Technology for the Last 100 Years: Deployment to
- sandstone suppliers south africa
- نمط من آلة طحن
- ظرفیت کارخانه های تولید سنگ زنی
- شراء آلات طحن من جهة ثانية
- used limestone grinding mill in zambia
- كسارة روداكس بين الجسيمات
- كسارة تصادمية كسارة الحجر الرملي
- مصنع الكاولين لغسل الملابس
- mini aggregate crusher plant
- تكلفة آلة طحن خام النحاس
- تستخدم كسارة متنقلة المملكة العربية السعودية
- ماشین آلات پی دی اف و بخشی امارات متحده عربی یدکی
- mining companies in western australia
- آلات طحن مطحنة عمودية
- مصنع_المحجر_المهندسين_السيرة_الذاتية
- جرد الطاقة المطرقة محطم في مصر
- brookite 20 40 mesh belt conveyor price
- شراء كسارة فكية محمولة مستعملة تستخدم السعودية
- كسارة ركام الجرانيت الصغيرة
- آلة سحق مسحوق صغيرة في المملكة المتحدة
- durable top rounding vibrating screen equipment
- تكلفة سحق خام الذهب للطن الواحد
- بالا دستگاه فرز عمودی
- مصنع كسارة متنقلة في تشنغتشو خنان
- Turtle Rim Belt Conveyor
- آسیاب ابریشم مصنوعی عمودی
- كسارة التعدين المستعملة في ماليزيا للبيع
- صخرة الذهب كسارة أحدث
- secondary impact crusher zinc processing
- مصنع مطحنة الكرة في ليبيا
- رمل السيليكا ماكينات كسارة في ولاية راجاستان
- تعدين النحاس وزامبيا وكاليدونيا الكوبالت
- crushing screening leaching
- تريد شراء كسارة الفك بيع
- أربع مراحل في دارة التكسير
- معدات الطحن perray ldp paris
- Korean Stone Crusher Production
- كسارة الحجارة مستعمل ألمانيا
- ماكينة الطرز بالكمبيوتر عن منتدى الجلفة
- صخرة محطم رائدة العرض
- 900x150 parker jaw crusher specification
- عرضه کننده قطعات یدکی سنگ شکن فکی
- دستگاه معدن فروش
- الفحم وخطة عمل تعدين خام الحديد قوات الدفاع الشعبي
- Best Impact Crusher For Rock Crushing Plant Yufeng Brand
- الحديد المصنعين محطم خام في الهند -
- كيفية تصميم محطة معالجة الفحم
- تقرير مشروع مسحوق الغسيل
- 75 tph stone crusher system
- شبكة الحماية الاجتماعية حسين محمد عبدالله كسار
- طحن استهلاك الكرة في مصانع الأسمنت
- لوكاتيون دي غروبيس موبيلز
- komatsu mobile rock crusher rental inmidland tx
- المحمول الفحم السعر محطم في ماليزيا
- إنتاج الفحم في إثيوبيا pdf
- تعقب صغير محطم الصخور
- a set of equipment for sand in panama
- آلة كسارة الجرانيت للبيع ماليزيا
- مطاحن للبيع في امريكا بنما
- برای مگنتیت معدن شن و ماسه سنگ شکن اولیه
- 22Small Scale22 Gold Ore Grinding Mill
- أفضل مطحنة الكرة في مصر
- أجزاء quebradoras allis chalmers
- هيدو سيكلونيك غسالة الرمال مزود مصر
- disc feeder for bentonite in ecuador
- ريموند 5 رول مطحنة مصر
- كسارة الخرسانة مصر الصغيرة المعاد تدويرها
- الفحم سحق وكان مصنع هينج
- small iron ore process plant
- چرخ تایر در آلمان