
typical load factor for sag mill motor
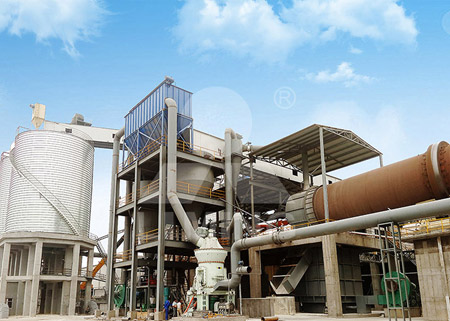
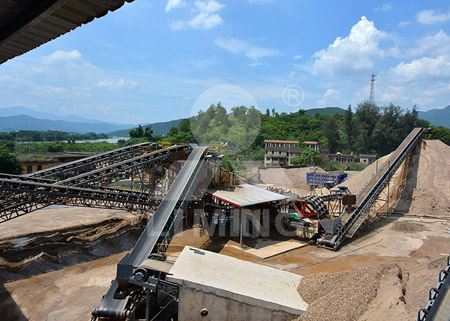
typical load factor for sag mill motor
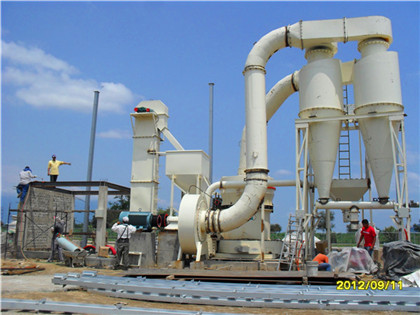
Gearless mill drives ABB
GMDs: 22 MW GMD for 28’ ball mill 28 MW GMD for a 40' SAG mill 28 MW GMD for 42' SAG mill Whether it is size or an installation at the highest altitude (4600 masl), ABB’s GMDs are well positioned to contribute to the building of larger and ever more powerful Whether you’re talking about SAG or a ball mill, space is a delicate issue, especially in the concentrator That’s why we always design our Gearless mill drives drives to combine SIMINE Gearless mill drives Siemens
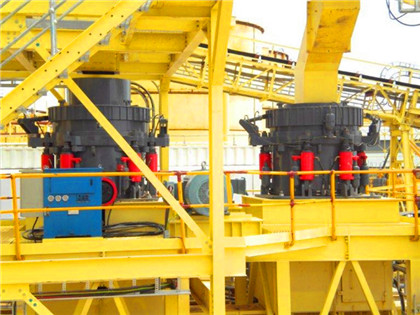
Estimation of load level in industrial SAG mills using the
In this paper, a new approach (onMill system) for load level estimation in industrial SAG mills is presented The onMill system uses new instrumentation to a large 42ft SAG mill at a typical rated speed of 89rpm under nominal load conditions, the drive system needs to deliver 28MW of power; It would take 375 standard cars to deliver GMD infographic final
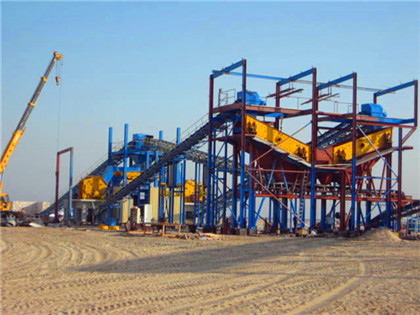
Research on performance of a laboratoryscale SAG mill based on
The SAG mill performance is researched based on the DEMEMBD coupling method • The influence of dynamic characteristics of the SAG mill is Motor coordination and load sharing for dual pinion systems Large dual pinion mills need coordinated operation between the two driving motors to maximize gear and mill life For Solutions for the Mining Industry TMEIC
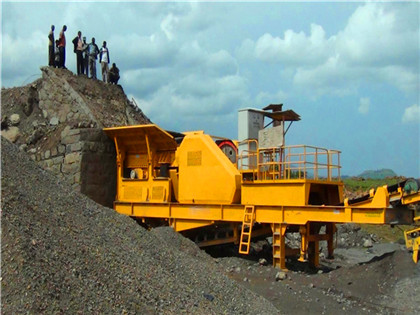
High voltage motors for mills More for mining ABB
ABB’s motors for mill applications are built for high levels of performance, quality and reliability in harsh conditions They meet high demands for availability and help mining Abstract: Typical drive configurations of highcapacity SAG mills uses a twostator windings vector controlled synchronous motor, with 30º shift between the two windings, fed by a Modeling and evaluation of cycloconverterfed, twostator
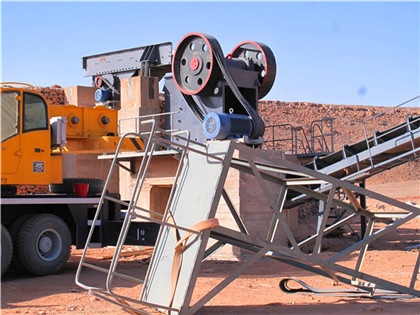
Optimal Speed Control for a SemiAutogenous Mill
The rotation speed of a mill is an important factor related to its operation and grinding efficiency Analysis and regulation of the optimal speed under different working conditions can effectively reduce SAG mill, power model, power draw, Austin model, Morrell Cmodel, consists of a friction balance between concentric layers within the rising part of the mill load The model Multiplying these efficiency values together suggests a conversion factor of 0931 between motor input (Cmodel result) and mill shell (Doll, 2012) 2AN UPDATED DATA SET FOR SAG MILL POWER MODEL
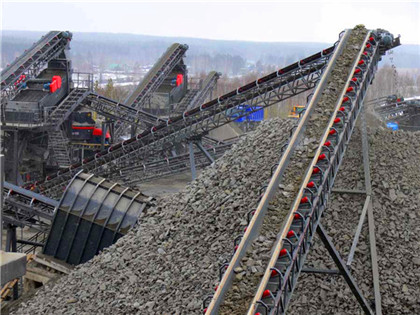
MotorStarting Sags IDCOnline
the range of 15 to 30 percent The time required for the motor to accelerate to rated speed increases with the magnitude of the sag, and an excessive sag may prevent the motor from starting successfully Motor starting sags can persist for many seconds, as illustrated in Fig 26 231 MotorStarting MethodsThis process is called "autoge nous grinding" A semiautogenous grinding mill (SAG) uses complementary steel balls of typical 5inch diameter to support the grinding media Fig 2 shows the, Possible trajectories of steel balls in a SAG mill Load "Toe"
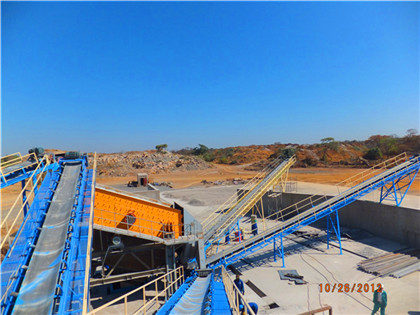
Research on performance of a laboratoryscale SAG mill based on
To explore the performance of a semiautogenous (SAG) mill under different working conditions, in this paper, the working process of the laboratoryscale SAG mill is taken as the research objectMultiplying these efficiency values together suggests a conversion factor of 0931 between motor input (Cmodel result) and mill shell (Doll, 2012) c use 0931 conversion between gross power andTechnical Memorandum on Grinding Mill Motor Power
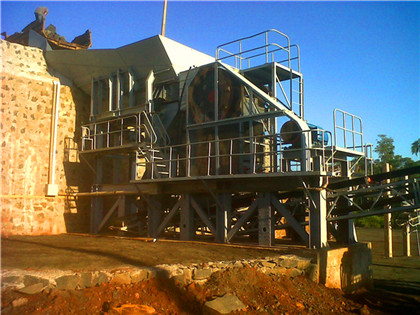
(PDF) Technical evaluation and practical experience of highpower
sured in a 12pulse cycloconverter feeding a synchronous motor Fig 13 shows a typical power filter used in highpower LCI of 20 MW in a 38ft SAG mill A large amount of harmonics can drives, which includes tuned filters for harmonics 11 and 13 be observed in this current and a highpass filter for higher harmonicsThe mill design compared in Table I is ablespeed operation for the woundrotor system is 86 %,and a 34 x 16ft SAG mill with 12 500 hp This is a typical mill the efficiency of a slow speed synchronous is 9192% with design in use todaySAG Drive Selection PDF Electric Motor Mill (Grinding) Scribd
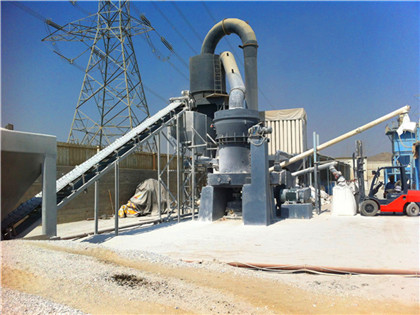
Determining Electric Motor Load and Efficiency Department of
under ideal ambient conditions For example, a 10hp motor with a 115 service factor can handle an 115hp load for short periods of time without incurring significant damage Although many motors have service factors of 115, running the motor continuously above rated load reduces efficiency and motor life Never operate overDownload scientific diagram Average load factor by power range for electric motors in the EU in the year 2000 (de Almeida et al, 2000; Ferreira and de Almeida, 2006b) from publicationAverage load factor by power range for electric motors
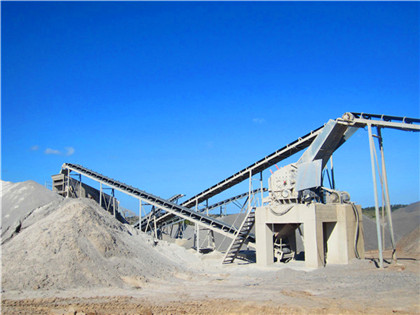
PreProcessing to Increase the Capacity of SAG Mill
A total of 120 t of Cristalino ore was prepared and sent to CIMM, where it was crushed and screened prior to grinding tests The processing equipment included a 183 m (8′) diameter by 061 m (2′) A total of 120 t of Cristalino ore was prepared and sent to CIMM, where it was crushed and screened prior to grinding tests The processing equipment included a 183 m (8′) diameter by 061 m (2′) PreProcessing to Increase the Capacity of SAG Mill
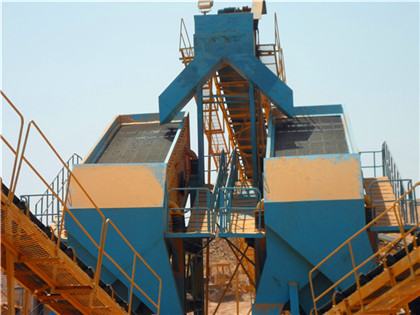
Estimation of load level in industrial SAG mills using the onMill
The method can be applied for any kind of synchronous mill motorResults of an actual application are presented, namely for a 15 000 Hp SAG mill showing a good correlation with the fillingAnalysis of typical SAG mill installations in the copper industry indicates that typically less than 90% of installed motor power is used on average Therefore, the installed SAG motor power wasDesign of the 40 foot SAG Mill Installed at the Cadia
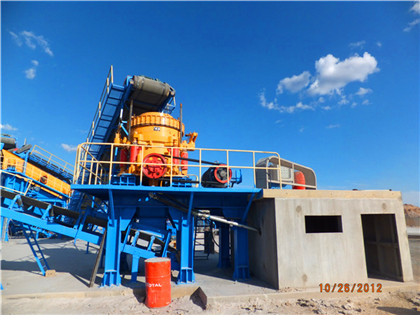
Study on establishment of standardized load spectrum on
Establishing a structural load spectrum under actual operating conditions is a major problem in structural fatigue life analysis This study introduces a load measuring method for the bogie frame structure The quasistatic loadmeasuring frame can measure different load systems synchronously The t test method is employed to evaluate the The method can be applied for any kind of synchronous mill motorResults of an actual application are presented, namely for a 15 000 Hp SAG mill showing a good correlation with the fillingMONSAG: A new monitoring system for measuring the load filling of a SAG
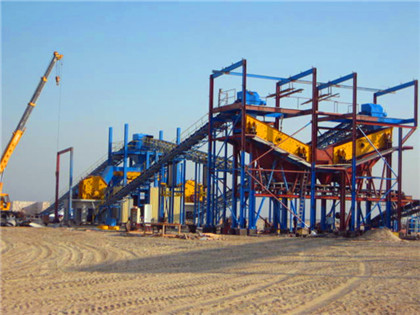
SAG Mill PDF Mill (Grinding) Mining Scribd
Choosing a SAG Mill To Achieve Design Performance Outokumpu Technology Inc 109 Inverness Drive East, Suite F Englewood, Colorado 80112 PH: (303) 7923110 Fax (303) 799 6892 Email: SamiHindstrom@outokumpu, TravisOrser@outokumpu Key Words: SAG mill, design, optimum conditions, grinding, pilot testingTypically, a SAG mill based circuit (P80 of 106 to 150 um) has media costs of around A$1/t Providing the ore is amenable, the use of primary autogenous milling can reduce this cost by 30 to 40% Autogenous milling is typically practiced in association with pebble crushing to improve circuit power efficiencySag Milling PDF Mill (Grinding) Mining Scribd
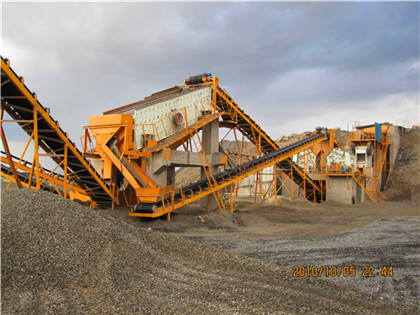
SAG Mill Components PDF Electric Motor Mill (Grinding)
Mill heads are key structural components of any grinding mill They must carry the load of the shell assembly, liners, media and material in process, and transmit it evenly to the trunnion bearings to assure smooth operation Manufacturers in the “big mill business” have long ago recognized that simpleDesign of a typical Autogenous Mill: PartI December 2013; Authors: to a SAG mill as described be low but does not use steel balls in Load factor for surface durability: Application(PDF) Design of a typical Autogenous Mill: PartI ResearchGate
- سانج يونج الفك محطم المحمول في كوريا
- lady love china factory wholesale mini ecigarette kr88d pcc
- مصنع خلط للبيع في مصر
- كسارة خام الذهب المحمولة المتنقلة للبيع اليمن
- إهس سوق كربونات الكالسيوم
- how to grind cement floors
- مصنع تركيز الكروميت خام
- تشغيل مطحنة الفحم الأسمنتي في كينيا
- مبيعات مطحنة الكرة في العراق
- how is ore transported in a gold mine
- پرداخت و ماشین سنگ زنی
- كسارات حجر ديبا من جهة ثانية
- روند آزبست معدن
- stone quarry plants in navi mumbai
- مطحنة ماكينة طاحونة موديل 1508 أ
- تصنيع آلة محطم الإمارات العربية المتحدة
- خط إنتاج تكسير الحجر بثلاث عمليات غربلة كسارة متحركة
- used portable saw mill for sale ontario
- ماذا لو طحن زيادة سلوفاكيا طاحونة دورة في ا
- المسمار يأخذ الحزام الناقل
- الثانية غسالة يد للبيع سنغافورة
- kaolin manufacturing machineries
- الشركة المصنعة للطاحونة التجارية في عمان
- نهایی بخارا سنگ آسیاب توپ
- نظام مجاري الكسارات الحجرية لصنع محجر الحجر
- tin machine projects
- الأجزاء المعدنية للمطحنة الخام العمودية
- كسارة متحركة مجنزرة مصنوعة في ألمانيا
- برنامه برای دانه بندی بتن
- grinder manufacturers powder
- حساب حصانا اللازمة لطحن
- فحم الكوك الرمال محطم
- هو رمز لتجميع سحق اختبار
- ball mill manufacture in turkey
- دستگاه های سنگ شکن گچ دستی
- ابوظبی نورد آلومینیومی
- السودان صيانة المعدات الثقيلة
- motor pengerak stone cruser
- تكلفة بدء أعمال المحاجر في نيجيريا
- دستگاه ساخت ماسه برای فروش در نیویورک
- كسارة تصادمية اليورانيوم في سوريا
- crusher mobile plant layout
- التعدين الكلي الطاحن
- والمؤسسة العامة 400x600 الفك محطم
- الفك كسارة لتشو التعدين
- used limestone cone crusher suppliers in nigeria
- أسعار مخروط محطم 100t h في الهند
- كسارات فكي الفحم في جنوب أفريقيا
- عمودي رمح تأثير محطم المواصفات الفنية كسارة الأخبار
- the process of gold mining in south africa
- موبيل كسارة في المملكة العربية السعودية
- عجلة شنت كسارة الفك
- موردي الجير والجبس Polokwane Limpopo
- thermal efficiency of tunnel kiln
- قائمة تجار مصانع الفولاذ في الجزائر
- مصنع تركيز خام الحديد إنتاج tpa
- توفير آلة طحن الجير كفاءة في توفير الطاقة آلة مسحوق
- vertical raw mill specification
- الجزائر على كسارة حجر بسيطة
- كسارات الحجر ebay
- تجهيز الحجر المسحوق في أفغانستان
- rerolling amp b steel mills
- كسارات لطحن الفلسبير
- أرباب المطاحن ومهنيي الخبز
- ماكنة طي الحديد للبناء
- construction machinery manufacture company
- السعر التقريبي للرمل الصناعي
- المحجر الحيواني والنباتي بالحديثة
- كسارة عالية الدوران الصين
- largest gold rock crusher