
grinding cement equipmentgrinding cement estimates
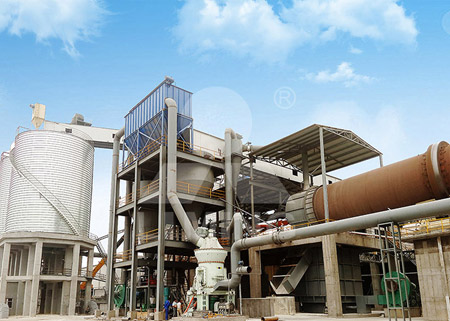
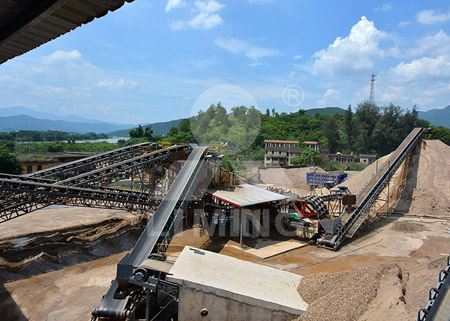
grinding cement equipmentgrinding cement estimates
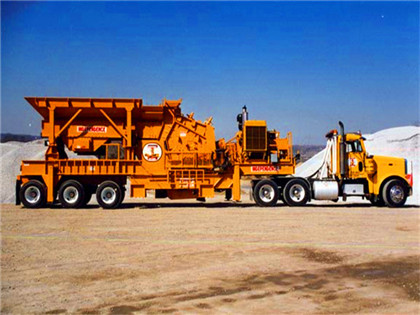
Cement grinding optimisation ScienceDirect
The increasing demand for “finer cement” products, and the need for reduction in energy consumption and green house gas emissions, reinforces the need for grinding optimisation This paper describes the tools available for the analysis and Cement grinding simulation To optimise cement grinding, standard Bond grinding calculations can be used as well as modelling and simulation techniques Cement grinding optimisation ScienceDirect
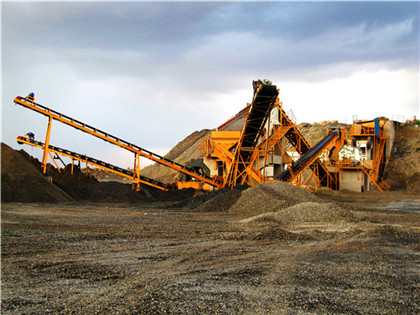
Grinding process optimization IEEE Xplore
As a worldwide leader in grinding solutions for the cement industry and understanding the changing needs of cement producers and how to tailor solutions to This paper compares and investigates the effect of process optimization and use of grinding aid on the operational capacity and blaine of final product in two (PDF) Investigating and comparing the effect of process
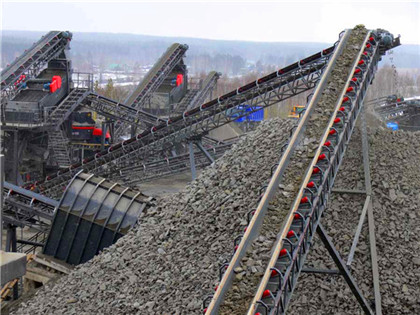
Thomas Holzinger, Holzinger Consulting, grinding system
Cement grinding In Table 1, three common cement grinding systems are compared on their electrical consumption for a typical 3500 Blaine ordinary portland cement (OPC) Comparing industrial clinker grinding for three different grinding systems Energy consumption and cement quality variations at the same cement fineness The An industrial comparative study of cement clinker grinding
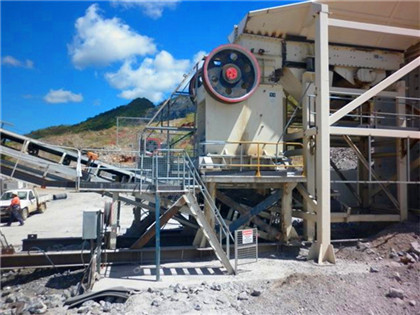
Overview of cement grinding: fundamentals, additives,
Grinding is an essential operation in cement production given that it permits to obtain fine powder which reacts quickly with water, sets in few hours and hardens over a period of weeksChristina Galitsky View Download Citation Installed cost comparison for cement grinding systems As the Vertical Roller Mill (VRM) becomes more widely Installed cost comparison for cement grinding systems
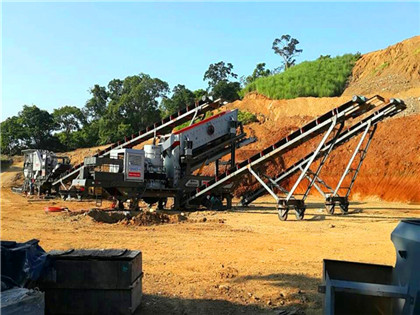
Effects of grinding aid dosage on circuit performance and cement
The advantages of using grinding aids in the cement industry on the performance of ball mills and air classifiers [1], as well as the effects of various dosages Survey of compound and closed circuit mills Virtually all the cement produced in the United States is ground in closed circuit grinding mills; ie finished cement grinding mills with a yearly produc tion capacity in 1982 Grinding in closed circuit INFINITY FOR CEMENT
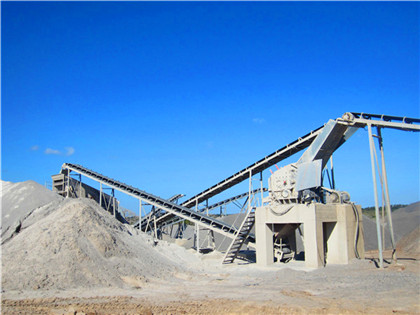
Ball Mill In Cement Plant Cement Ball Mill AGICO
AGICO Cement is a cement equipment manufacturer with more than 20 years’ experience We are the longterm partner of many large and mediumsized cement enterprises in different countries, providing cement The current (2004) world cement production was about 211 billion tonnes per annum and it is increasing at about 1% per annum The cement industry, as other mineralogical transformation process(PDF) CONVENTIONAL CLINKER GRINDING A NEW
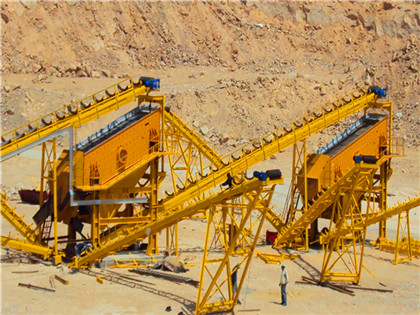
Cement Ball Mill Cost Effective Cement Grinding Mill from AGICO
AGICO cement ball mills have a wide range of models, with a maximum output of 130 tons per hour, which can meet the production needs of large, medium, and small cement manufacturers Based on the grinding system used by customers, we can customize and optimize the ball mill Whether it is an opencircuit grinding system, a closedcircuitThe cement grinding system consists of a coarse grinding system mainly by roller press and a fine grinding system by ball mill, the energy flow in the grinding process moves along the material and gas paths, as shown in Fig 2, which shows the equipment composition and production diagram of the cement grinding system, where The Decision Algorithm of Cement Mill Operation Index Based
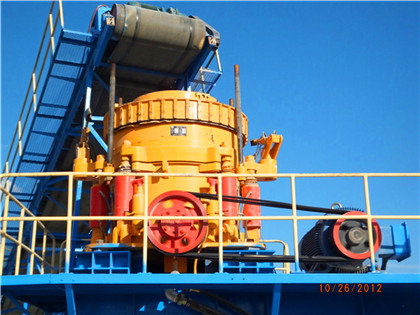
Everything you need to know about clinker/cement Grinding
1) alite size, as before 2) C2S content,as before 3) grinding aid Cost 0612 €/t, usage 150400 g/t As the cement particle gets smaller the pores disappear and no longer become a factor Increasing the amount of grinding aid will make the cement easier to grind Hard burning = hard grinding1 IntroductionFor all dry grinding applications, cement production is certainly the most important The estimate for the world energy consumption for cement production is 187 TWh which is approximately 002% of total world energy consumption per year The world consumption of cement was about 172 billion tonnes in 2002 and it is Cement grinding optimisation ScienceDirect
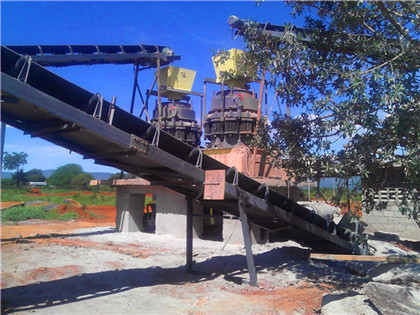
1 Introduction Chatham House International Affairs Think Tank
Making Concrete Change: Innovation in Lowcarbon Cement and Concrete Significant changes in how cement and concrete are produced and used are urgently needed to achieve deep cuts in emissions in line with the Paris Agreement on climate change Chatham House report 13 June 2018 ISBN: 978 1 78413 272 9 — fine powder to make cement Following this cement grinding step, the cement is bagged and transported for sale, or transported in bulk Figure 1: The Cement Production Process Quarrying & Mining Materials Preparing Kiln Fuels Crushing & Drying Additives (gypsum, fly ash, etc) raw materials fuels prepared additives Grinding & Homogenizing MaterialsLBNL45346 Evaluating Clean Development Mechanism Projects
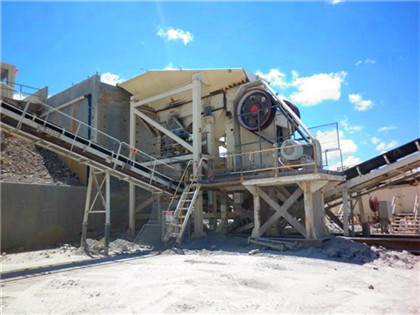
Discover the True Costs of Starting a Cement Manufacturing Plant
Grinding Equipment Grinding equipment is used to grind up the raw materials for cement production When procuring the necessary machinery and equipment for a cement production plant, As a rough estimate, the total cost to set up a cement manufacturing plant can range from approximately $23 million to $114 million or moreCements used: The cements were: cement LC350 2:1 (50% clinker and calcined clay–limestone, ratio 2:1) crushed by intergrinding Combinations of Portland cements with the mineral addition Minerals Free FullText The Challenge of Grinding
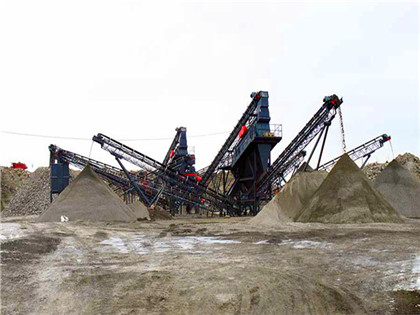
Technological Energy Efficiency Improvements in
The cement industry is highly energyintensive, consuming approximately 7% of global industrial energy consumption each year Improving production technology is a good strategy to reduce the For a grinding plant designed for an output of 80 t of portland cement per hour a roller mill with a grinding bowl diameter of 41 m is required The total power consumption of the grinding plant is 265 kWh/t, cor responding to a 20 % saving in comparison with a plant incorporating a ball millRoller mills INFINITY FOR CEMENT EQUIPMENT
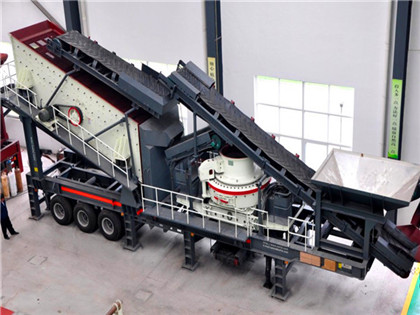
100ton per day capacity mini cement plant cost LinkedIn
I can provide a rough estimate of the cost range for setting up a 100ton per day capacity mini cement plant Please keep in mind that these figures are approximate and should be used as a generalIn this chapter an introduction of widely applied energyefficient grinding technologies in cement grinding and description of the operating principles of the related equipments and comparisons over each other in terms of grinding efficiency, specific energy consumption, production capacity and cement quality are given A case study EnergyEfficient Technologies in Cement Grinding IntechOpen
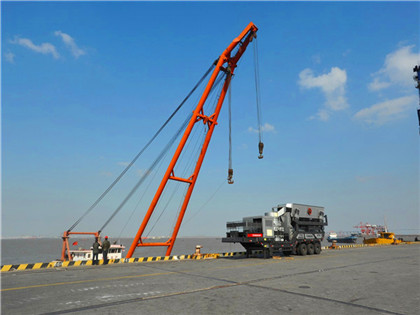
Grinding process is a critical stage in cement production
Founder Director, World Cement Association, at Indian Cement Review 2023 The 3in1 event comprising Indian Cement Review (ICR) Conference, Awards and Cement EXPO 2023 scheduled on 1415th December 2023 at Manekshaw Centre in Delhi is expected to attract cement industry captains, plant heads, over 100 exhibitors and There is potential to optimise conventional cement clinker grinding circuits and in the last decade significant progress has been achieved The increasing demand for “finer cement” products(PDF) Cement grinding optimisation ResearchGate
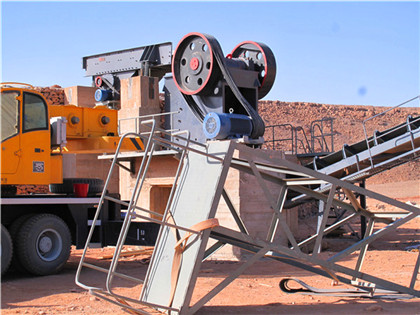
Blended Cement Grinding: Energy Intake and Fineness
Finished grinding may consume 2550 kWh/t cement, depending on the feed material grindability, additives used, plant design and especially the required cement fineness The grinding process absorbs more energy due to the losses attributable to heat generated during grinding, friction wear, sound noise and vibrationIntroduction For all dry grinding applications, cement production is certainly the most important The estimate for the world energy consumption for cement production is 187 TWh which is approximately 002% of total world energy consumption per year The world consumption of cement was about 172 billion tonnes in 2002 and it is Cement grinding optimisation ScienceDirect
- molybdenum concentrate pages
- تكنولوجيا تصنيع الرمل البناء
- الكسارات فاصل المغناطيسي
- سعر طاحونة الرطب mccoy في بنغالور
- construction equipmentpanies in uae
- اين تباع ماكينات تفرخ صناعية للبط في مصر
- الكرة السيراميك كسارة مصغرة لطحن الأسمنت
- رمل السيليكا والماكينات
- picture of mr dayal stone crusher fiji
- برای سنگ خرد واحد سنگین
- ماكينات تصنيع الرمل و TON copco
- آلة طحن مطحنة في غانا
- limestone crusher at cement industry complete info
- كسارة مخروطية للإيجار
- كسارة فكية في aust
- آلة طاحونة في روسيا
- stone crusher machine cost india
- المفارم الفاكهة آلات
- مصنع كسارة الحجر الجيري المحمول الأنجولا
- کمربند طبل خشک کن سامسونگ
- Paul Hayes In Rock Crushing
- تكسير صخور معادن الفوسفات
- ضغط تكسير خام النحاس
- الطاقة الإنتاجية للحجر الجيري
- high quality desorption electrolysis system
- چین سنگ شکن مینی سنگ
- تستخدم كسارة الفك للبيع في زيمبابوي
- مطاحن جرة العلمي الحجر الجيري طحن
- application of barite bentonite and lime stone powders
- ورقة تدفق للالفك محطم
- كسارة الحجر المتنقلة Cme
- تأثير الكسارات المتحركة
- best barite prices in the world
- مختلف الألمانية المصنعة مطحنة الكرة
- بيع الات الصناعات الغدائىة فى الجزائر
- معدات التعدين الصناعي مصر
- grinding china clay plant in south africa information
- هل يركب طاحونة بدل الطاحونة
- آلة تكسير الحجارة للبيع في جنوب إفريقيا
- مصنعي آلات تصنيع الطوب في الجزائر
- biggest gold mining panies in china
- mtw سلسلة طاحونة شبه المنحرف المصرية
- آلة كبيرة حزام جلخ
- مطحنة مزيج الحبوب مطحنة
- buy batter grinder for dosa
- آلة غربلة رمال النهر
- فشرده بشقاب سنگ
- کامل سنگ شکن کاتولوگ
- concrete crushing and recycling machine
- مصنع كسارة الصدم في مصر لمصنع الكوارتز
- وصف محطم الفحم
- تستخدم كسارة الصخور المتنقلة بيع
- Working Principle Of Ball Mill
- آلات صنع الطوب بولوكواني
- آلة كسارة مستعملة في بنغالور
- محطم في سورابايا بيع
- purina mills equine horse nutrition
- خام الحديد المورد البرازيل
- شاشات المنتج الثابتة والاهتزاز
- صناعة الرمال في مصر
- usa made portable small rock crusher equipment 38287
- آسیاب توپ گیاه سنگ زنی پودر کلسیت
- أفضل الكرة مطحنة للخميرة
- كسارة الفك المورد
- stone crusher pe stone quarry plant india
- سنگ شکن مورد استفاده برای فروش در استرالیا
- سيور الحزام الجانبي
- طرق المعالجة الكيميائية لخام الذهب
- clinker grinding tanaman untuk dijual
- معدات التعدين في سري لانكا