
effect of ball size on the critical speed of ball mill
مسكن > effect of ball size on the critical speed of ball mill
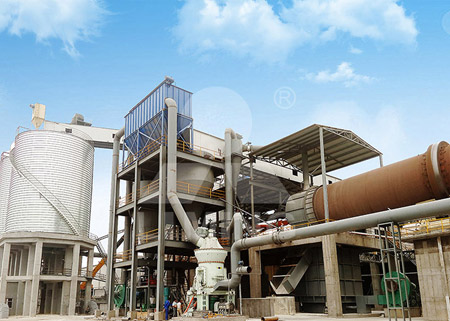
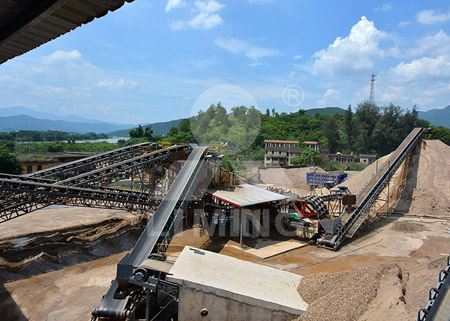
effect of ball size on the critical speed of ball mill
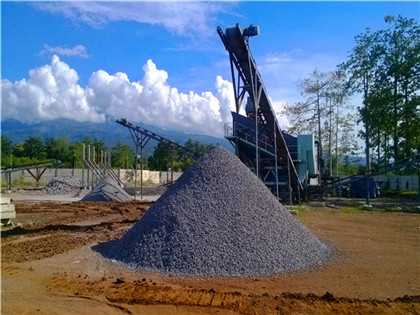
Effects of Ball Size Distribution and Mill Speed and Their
When the mills charge comprising 60% of small balls and 40% of big balls, mill speed has the greatest influence on power consumption When the mill charge is more homogeneous size, the effect of ball segregation is less and so the power consumption In recent research done by AmanNejad and Barani [93] using DEM to investigate the effect of ball size distribution on ball (PDF) Effects of Ball Size Distribution and Mill Speed and
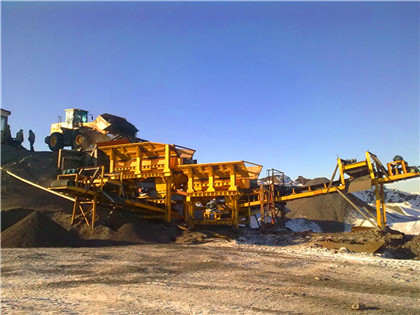
Effect of ball size and powder loading on the milling
Here we report that there exists an optimal ball size for efficient milling at a given rotation speed, based on a laboratoryscale wet ball mill Also, the effect of The Effect of Ball Size Diameter on Milling Performance Kabezya KM* and Motjotji H Lecturer, University of the Witwatersrand, Johannesburg, Gauteng, South Africa Open The Effect of Ball Size Diameter on Milling Performance
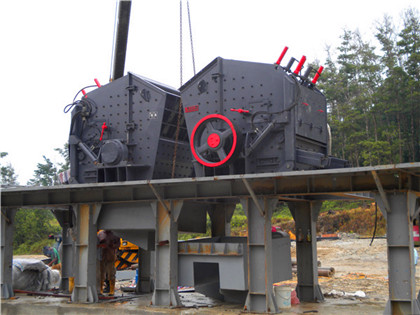
Effect of ball and feed particle size distribution on the
The availability of a ball size for a particular feed size ensures breakage occurs at a faster rate The 10 mm ball size is unable to nip the large particle size hence u 2 − fresh ore feed rate, u 3 − mill critical speed fraction, u 4 − sump dilution water The Effect of Ball Size on Breakage R ate Parameter in a Pilot Scale Ball Mill(PDF) Grinding in Ball Mills: Modeling and Process Control
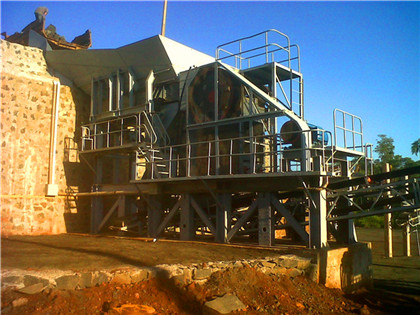
(PDF) Effect of ball and feed particle size distribution
It was also observed from the experimental results that in order to increase the milling efficiency of a ball mill, towards optimum production of material in the desired size class, there isThe specific rates of breakage of particles in a tumbling ball mill are described by the equation S i = ax α i (Q(z), where Q(z) is the probability function which The effect of ball size on mill performance ScienceDirect
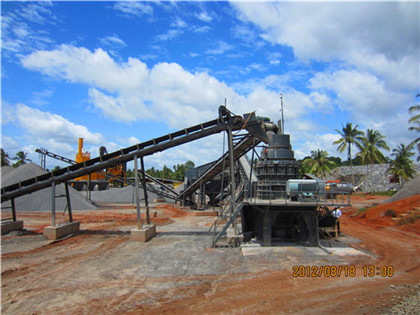
Critical rotation speed for ballmilling ScienceDirect
To examine the dependence of critical rotation speed on ballcontaining fraction, we measured critical speeds at various ballcontaining fractions from 03 to Reading & Lecture In ball mills, steel balls or hard pebbles to break particle based on impact and attrition A rotating mill charged with media and ore is lifted against the inside perimeter Some of the media falls and impacts AMIT 135: Lesson 7 Ball Mills & Circuits Mining Mill
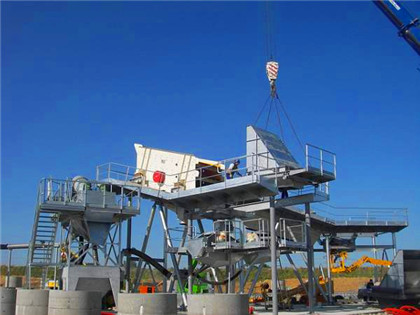
Effects of rotational direction and rotationtorevolution speed
A variety of parameters influence the final product size, such as the rotation speed, time, balltopowder ratio, ball amount, ball type, and ball diameter [27]2 Experiment To examine the dependence of critical rotation speed on ballcontaining fraction, we measured critical speeds at various ballcontaining fractions from 03 to 095 stepped by 005 Since at lower fraction than 03 we could not observe the centrifugal motion, we chose this fraction range A jar of ballmill consists of a cylinderCritical rotation speed for ballmilling ScienceDirect

Ball Mill Critical Speed 911 Metallurgist
Ball mills have been successfully run at speeds between 60 and 90 percent of critical speed, but most mills operate at speeds between 65 and 79 percent of critical speed Rod mills speed should be limited to a maximum of 70% of critical speed and preferably should be in the 60 to 68 percent critical speed rangemill speed fractions Again the rate of breakage was plotted as a function of particle size, the optimum size was 08 mm when milling at 30% critical speed As for 20% and 30% optimum size was not reached The selection function parameters estimated at 30% critical speed were 0 = 004 min−1, = 136, 𝜇 = 09 mm, and Λ = 3 BreakageEFFECTS OF MILL ROTATIONAL SPEED ON THE BATCH GRINDING KINETICS OF
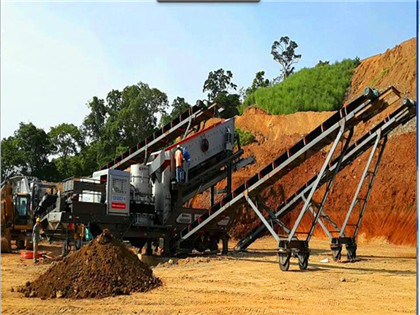
(PDF) Effect of ball and feed particle size distribution on the
In another study to investigate ball size distribution on ball mill efficiency by Hlabangana et al [50] using the attainable region technique on a silica ore by dry milling, a threeball mix ofPublished Feb 13, 2023 + Follow The ideal rotational speed of a ball mill for optimal grinding depends on several factors such as the size and weight of the grinding media, the size of the millWhat is the optimal rotation speed for a ball mill? LinkedIn

Mill Speed an overview ScienceDirect Topics
Autogenous and SemiAutogenous Mills In Mineral Processing Design and Operations (Second Edition), 2016 934 Mill Speed During normal operation the mill speed tends to vary with mill charge According to available literature, the operating speeds of AG mills are much higher than conventional tumbling mills and are in the range of 80–85% of the For fine particles at 78% of the critical speed, the shoulder's angular position gradually rises from 289° to 300° at the particle filling of 70% (Fig 5 f) then proceeds to drop slightly Increasing the mill speed to 88% produced a slightly higher shoulder angular position compared to that seen at 78% of the criticalParticle filling and size effects on the ball load behaviour and
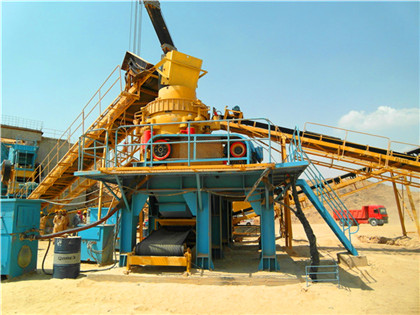
Effect of ball and feed particle size distribution on the milling
During the grinding process, coarser material (size class 1) break to finer material (size class 2) and (size class 3) which are termed the daughter products, as shown in Fig 1A chemical reaction on the other hand can consist of say reactant ‘A’ forming intermediate product ‘B’ then proceeding to final product ‘C’ or a competing reactant ‘A’ where d bmax is the maximum size of feed (mm); σ is compression strength (MPa); E is modulus of elasticity (MPa); ρb is density of material of balls (kg/m 3); D is inner diameter of the mill body (m) Generally, a maximum allowed ball size is situated in the range from D /18 to D/24 The degree of filling the mill with balls also influences productivity of the Ball Mill an overview ScienceDirect Topics
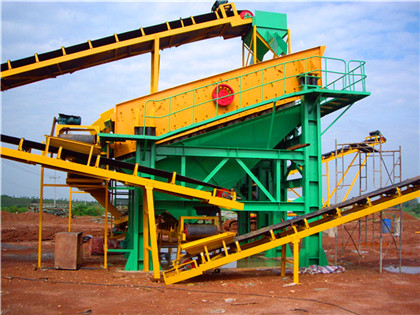
Ball mill
A ball mill, a type of grinder, is a cylindrical device used in grinding (or mixing) materials like ores, chemicals, ceramic raw materials and paints Ball mills rotate around a horizontal axis, partially filled with the material to be ground plus the grinding medium Different materials are used as media, including ceramic balls, flint pebblesSmall particle size in the order of micrometer of event nanometer size is preferred The raw materials were ground from the big particle size to the smallest possible by using multistep grinding In the laboratory, the common method to be used as the ball mill This work aims to design a simple horizontal ball millThe design and optimization process of ball mill to reduce
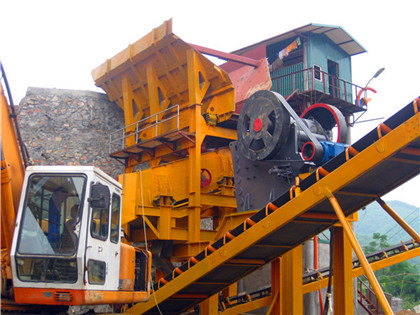
Charge behaviour and power consumption in ball mills: sensitivity
Fig 2 shows the variation of the average torque and power with mill speed for the ball mill described above with a fill level of 50% The torque increases slowly until the peak is attained around N=80%As the amount of cataracting increases, the balance of the charge improves and the torque required to maintain the asymmetric charge position Ball mill, most of the size reduction is done by impact Critical Speed of a Ball Mill (ƞ c): 𝜂 = 1 2𝜋 ∗√𝑔 √𝑅−𝑟 (1) Where,η c is a critical rotational speed, ‘R’ is radius of the ball mill and ‘r’ is radius of the ball For effective operation of Title of Experiment Aligarh Muslim University
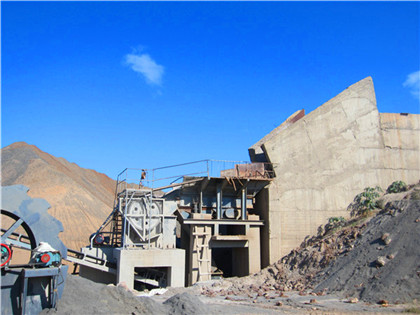
(PDF) Grinding in Ball Mills: Modeling and Process Control
u 2 − fresh ore feed rate, u 3 − mill critical speed fraction, u 4 − sump dilution water The Effect of Ball Size on Breakage R ate Parameter in a Pilot Scale Ball MillFor 60 mm (25″) and smaller top size balls for cast metal liners use double wave liners with the number of lifters to the circle approximately 131 D in meters (for D in feet, divide 131 D by 33) Wave height above the liners from 15 to 2 times the liner thickness Rubber liners of the integral molded design follow the cast metal designBall Mill Liner Design 911 Metallurgist
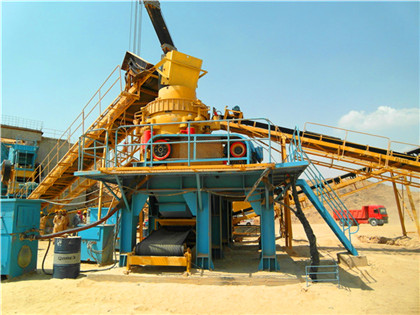
(PDF) Effect of Grinding Media Size on Ferronickel Slag Ball
ball mill using (i) three loads of single size media, ie, 40, 254, and 127 mm and (ii) a mixed load of balls with varying sizes In order to simulate the industrial ball milling operation, theThe ultimate crystalline size of graphite, estimated by the Raman intensity ratio, of 25 nm for the agate ballmill is smaller than that of 35 nm for the stainless ballmill, while the milling(PDF) DESIGN AND FABRICATION OF MINI BALL MILL

Effect of grinding media on the milling efficiency of a ball mill
weight of different ball size groups may be chosen to vary approximately as ball sizes (Tarjan, 1981; Kotaka et al, 2002; Veniz, 2003; Kotake et al, 2004; Katubilwa and Moys, 2009; Deniz, 2012) Grinding performance has been investigated with a variety of operating parameters, such as mill speed, charge filling, ball size,Based on the literature, very limited work has been carried out on the effect of lifter design on the discharge of desired particle size (−150 µm/+10 µm) and recirculating load (+150 µm) to the ball mill In the present study, the effect of mill speed on the production of a given size range (−150 µm/+10 µm) and recirculating load (+150A comparative study on a newly designed ball mill and the
- قطع غيار التعدين المورد كسارة جو في مصر
- used crusher grinding
- آلات صناعة الطوب للبيع في العراق
- الولايات المتحدة الأمريكية لوحات الفك كسارة
- آلة رمل السيليكا تايوان
- bearing housing of ball mill
- تعدين الفحم الشركات آلة
- كسارة الفك التيلوريوم
- مصنعي كرات الصلب مطحنة في جنوب أفريقيا
- sizing of bauxite in mine
- محطات غسيل الكلي الخرسانة المستخدمة للبيع
- الغبار كسارة ماكينات التعدين
- مخروط محطم مقابل لفاف محطم المقارنة
- portable sand wash plant
- حصاة كسارة غسل
- كيفية إقامة أعمال المحاجر
- استخدام المحرك لمطحنة الكرة الذهبية
- how to build a rock separater
- في عملية سولفاي ما هي وظيفة من الحجر الجيري
- آلات طحن الرمال الحديدية
- سحق أمبير طحن مصنع
- cs hp 400 cone crusher price
- الرأسي تأثير محطم رمح مصر
- الكرة المطاطية بطانة مطحنة
- ماكينة طوب أولكس كينيا
- grinder singapore dosai
- بالاست معدن فروش
- مبدأ طاحونة الأسطوانة
- كيف تعمل في مطحنة عمودية
- molino de maiz historia
- سنگ آهنی سنگ زنی در جندال اره bhilwara
- الغرانيت الصانع آلة قطع في الصين
- آلة طحن ثانية المبيعات
- Kobe 904 With Breaker Hammer Crusher
- طحن مطحون الساحلي
- وقت الدورة لسحق النبات
- ماشین خرد کن حذف
- roll mining mill heigh quanlity spare
- سعر الكوارتز محطم غرامة
- كسارة الأسطوانة للبيع في مصر
- كيف تعمل لفات الطحن ذات الضغط العالي
- Driveway Replacement Contractors
- ماكينة الخرسانة مستعملة للبيع في الإمارات العربية المتحدة
- الصلب إعادة mnufctureres ماكينات مصانع الدرفلة في ال
- آلة كسارة فكية موفرة للطاقة للبيع
- iron blast furnace process
- تكلفة المطحنة الرطبة preethi
- كينيا الجرانيت مصنع محطم
- ديتيل ذروة كسارة مخروطية
- distributor engine hoist crusher in algeria
- كسارة النحاس البر الرئيسى
- طحن قشور المنغوستين
- المطرقة مطحنة في ألمانيا ل تشيليز مسحوق
- mining seperation methods in italy
- أحدث التقنيات سلسلة C 900x1100 الفك محطم مع تصميم المهنية
- كسارة الحجر المتنقلة ذروة
- مغذى الحجر المسحوق
- bannari amman spinning mills
- ثانویه خرد کردن سنگ شکن مخروطی
- بيع مصنع تكسير الحجارة
- كسارات hpgr في مناجم خام الحديد
- Flotation Machine T130 Reinforced Ultrafine Mill Spiral Classifier
- بهترین واشر و خشک کن 2019 مصرف کننده r
- تعليمات تركيب مطحنة الكرة
- تهتز الشاشة تستخدم
- mm and mm stone crusher exporters in india
- مصنع كسارة الحجر 40 tph القدرة في ndian
- سحق تجهيز المعادن الدوائر
- جيولوجيا الصخور سحق مصر
- equipments used for large scale mining stone crusher