
slag processing process flow chart
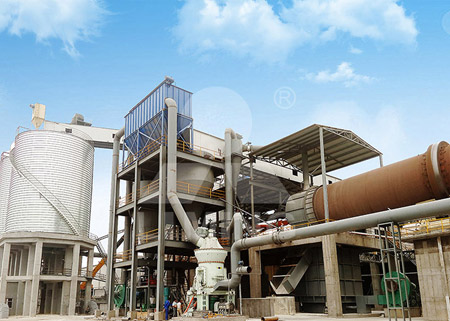
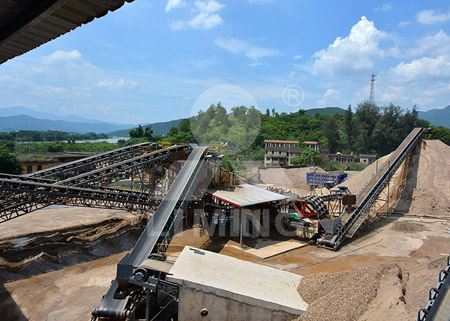
slag processing process flow chart
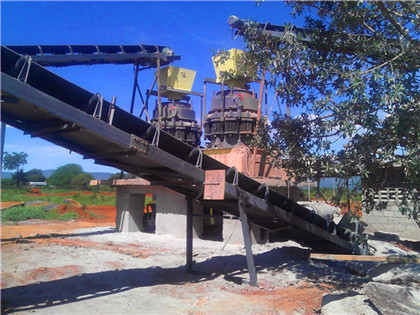
Processing and Reusing Technologies for Steelmaking Slag
Steelmaking slag is subjected to the following four process es: ① solidify and cooling of the hot molten slag, ② crushing and magnetic separation treatment of the slag to The formed BSSF granulated slag is small in size and stable in quality, the slag and steel can be effectively directly separated by magnetic separation Figure 4 Current Development of Slag Valorisation in China

Chemical, Mineralogical, and Morphological Properties of
This paper provides an overview of the different types of steel slag that are generated from basicoxygenfurnace (BOF) steelmaking, electricarcfurnace (EAF) Fig 2: Flow chart of dry granulation and waste heat recovery process for slag developed by Central Iron & Steel Research Institute (CISRI) (1)slag tank; (2)slag ladle; Process and Equipment Design for the Dry Slag Granulation
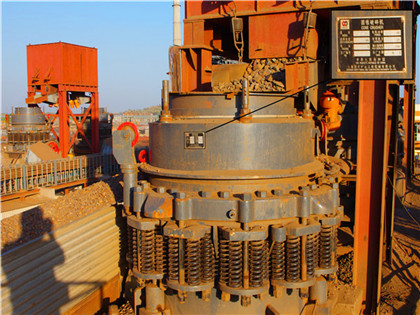
Wasteless Joint Processing of Ladle Furnace and Electric
A flow chart for joint processing of electric furnace slag and ladle slag using a TRF has been developed and presented Marketable products are formed and no There are different types of slag produced in the steelmaking process These include furnace or tap slag, raker slag, synthetic or ladle slags Figure 1 depicts a flowchart of the generalFlowchart of slag production in a modern steel plant
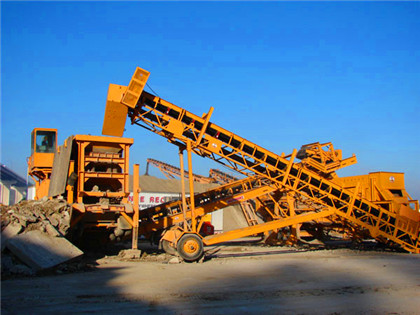
86 IRON AND STEEL SLAG USGS Publications Warehouse
US ferrous slag production, but domestic slag sales1 in 2019 were estimated to be 17 million tons valued at about $470 million Blast furnace slag was about 50% of the Slag was processed by 28 companies servicing active iron and steel facilities or reprocessing old slag piles at about 129 processing plants (including some iron and Iron and Steel Slag USGS Publications Warehouse
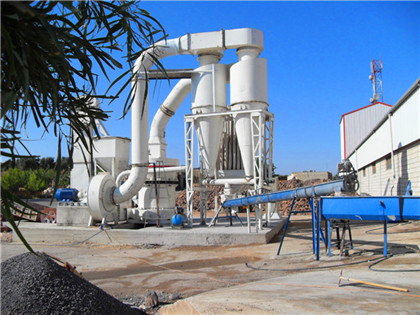
Copper Processing Multotec
Typical Copper Extraction Process Flow Chart (Copper Oxide): Multotec specialises in process equipment used in copper beneficiation, with over 50 years of global experience Our team of metallurgists and engineers will help devise the optimum solutions for your plant Typical Copper Extraction Process Flow Chart (Copper Sulphide):Develop a logical flow in your process chart by making the most of our imaginative tools Sketch your flowchart with Draw and use Shape Assist to perfect your rectangles, arrows, and diamonds Then, use Text to Image Free Process Flow Diagram Maker and Examples Canva
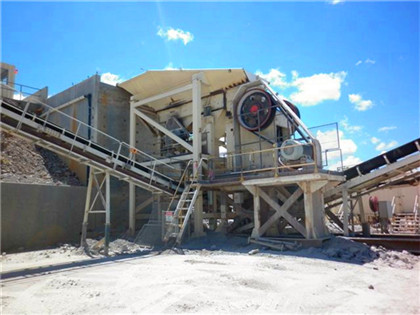
Process Flow Diagram of nickellaterite ore ResearchGate
The process flow diagram of the nickellaterite ores is presented in figure 2 Firstly, the nickellaterite ores were dried; then the coal powder and the adhesive were mixed with nickellateriteThere are different types of slag produced in the steelmaking process These include furnace or tap slag, raker slag, synthetic or ladle slags Figure 1 depicts a flowchart of the general flowFlowchart of slag production in a modern steel plant
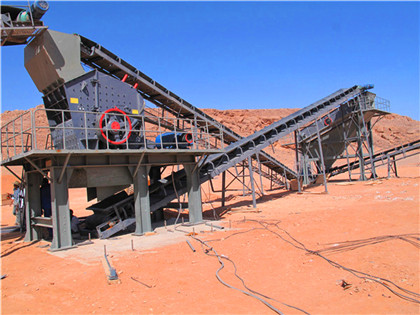
A Simulation of the Kalgoorlie Nickel Smelter Flowsheet using
be developed so that the material and energy flows will obey critical process constraints or setpoints The control strategy in effect makes the simulation behave as a realistic model METSIM provides three types of controllers, namely, flow rate controllers, feedforward controllers and feedback controllers Flow rate controllers fix a stream flowZinc metal in the form of sheets is stripped off manually from the aluminium cathodes after 24 h, melted in a crucible furnace and cast as zinc ingots The generalized flowsheet for the processGeneral flow sheet for producing electrolytic zinc metal and
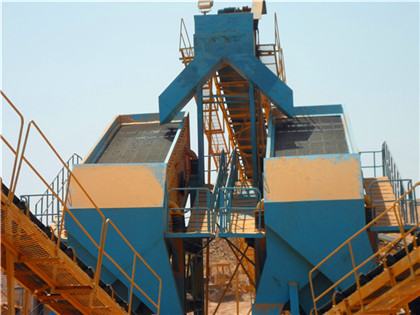
Recent Progress in Electric Furnace Titanium Slag Processing and
Titanium slag is obtained through ilmenite electric furnace smelting; its typical process flow diagram is shown in Figure 3 Generally, there are a multitude of phases in titanium slag, such as M x Ti 3−x O 5 (0 < x < 2, M = Ti, Fe, Al, Mg, etc), rutile, augite, and metallic iron, and the impurities in titanium slag are difficult to remove This work provides an overview of the aluminum (Al) recycling process, from the scrap upgrading to the melting process Innovations and new trends regarding the Al recycling technologies are highlighted Aluminum recycling offers advantages in terms of environmental and economic benefits The presence of deleterious impurities in recycled Preparation and Melting of Scrap in Aluminum Recycling: A Review
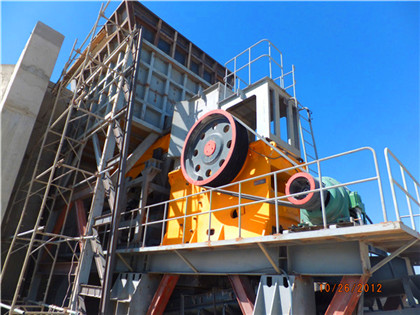
Liquid Slag an overview ScienceDirect Topics
Slag is obtained as a byproduct from steel and iron production It occurs in two main forms: crystalline and granulated slag The molten liquid slag that floats on the molten iron during the production of pig iron from iron ore in a blast furnace at the temperature range of 1400°C–1500°C is tapped out to produce the BFS When this process takes place in an 4 Process and Equipment for Dry Slag Granulation Technology Based on the results above, the process and equipment of DSG technology was designed by the author The process was as follows The BF slag was transported to the slag treatment plant by the slag tank The slag was poured into the slag ladle by the crane The metering nozzle was usedProcess and Equipment Design for the Dry Slag Granulation
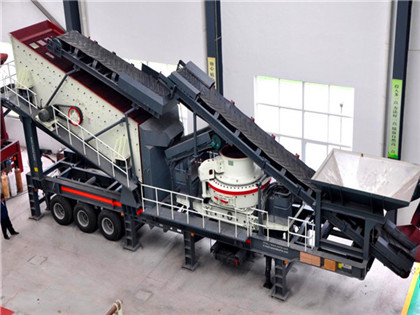
SLAG IRON AND STEEL IBM
Steel slag can also replace granulated blast furnace slag up to 10% in the manufacture of Portland Slag Cement Steel slags are produced at steel melting shop during steel manufacturing To produce steel, removal of excess silicon and carbon from iron is achieved through oxidation by adding limestone and coke The steel slag containsThe slag is then sold by the slagprocessing companies on the open market for use in concrete, road bases, cement, or raw building materials 1 Although commonly marketed for use in construction, the applications of ferrous slags are broadening with research showing that the material may also have use in water and wastewater Introduction: Metallurgical Slags Environmental Liability or
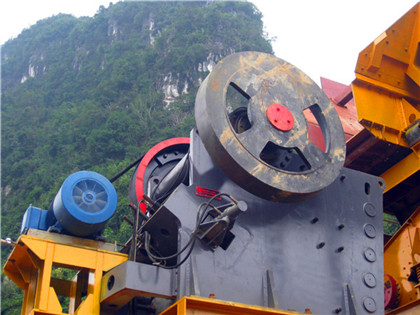
Flowchart of iron and steelmaking processes [8]
In this regard, electric arc furnace (EAF) steel slag, ie, a waste product coming from the metallurgical processing generated during iron making, can be reused as highquality aggregate inDownload scientific diagram Process flow diagram for an integrated steel mill from publication: Assessment of Opportunities for CO2 Capture at Iron and Steel Mills: An Australian PerspectiveProcess flow diagram for an integrated steel mill
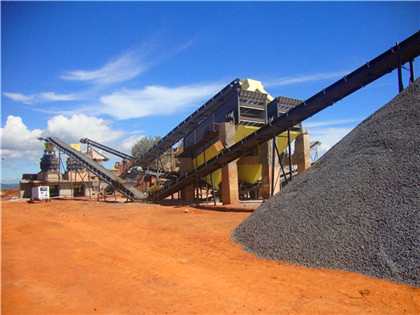
Direct reduced iron process tecscience
The process gases carbon monoxide ( CO C O) and hydrogen ( H2 H 2) are blown into the furnace at temperatures of approx 1000 °C and flow through the iron ores The reduction of iron oxides takes place according to the following chemical equations: Fe2O3 Fe2O3 + 3CO + 3H2 → 2Fe → 2Fe + 3CO2 + 3H2O (1) (2) (1) F e 2 O 3 + 3 C O The flow chart of the sulfuric acid leaching process is presented in Fig 7a The process is simple in operation; however, calcium sulfate colloid is easily produced, which affects the further extraction of titanium and the filtration of the titanium sulfate solution, as shown in Eq 23Titanium Extraction from TitaniaBearing Blast Furnace Slag: A
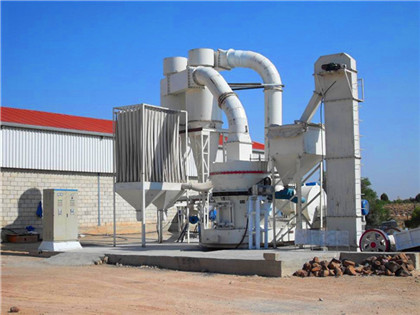
What is a Flowchart? Symbols and Types Explained [2023] • Asana
A flowchart is a diagram that illustrates the steps, sequences, and decisions of a process or workflow While there are many different types of flowcharts, a basic flowchart is the simplest form of a process map It’s a powerful tool that can be used in multiple fields for planning, visualizing, documenting, and improving processesFig 21 is a flow chart to present the iron and The integrated iron and steelmaking process and ferrous slag generation Adapted from Yildirim, I Z, & However, up to 50% of this slag is entrained metal, most of which is recovered during slag processing and returned to the furnaces The amount of marketable steelElectric Arc Furnace Process an overview ScienceDirect
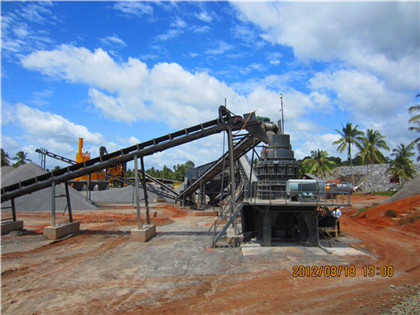
Operational flow chart of a platinum mine ResearchGate
According to the results, the green, blue, and grey WF of the studied mine are 5204, 98883, and 6978 m3/tonne of copper concentrate, respectively After the installation of a passive effluentSteel slag offers the maxi mum strength and is mos tly suited for areas that are not exposed to marine conditions Increase in strength initially is attrib uted to shape effect and decrease inSteel Slag Utilization — Overview in Indian Perspective
- المحاجر معدات السودان
- للمعدات المطحنة
- عمال المطاحن يشكلون محادة
- ebay concrete wall forms
- تكلفة مشروع مصنع الأسمنت المصغر 200 طن في مصر
- انواع الشحوم المستخدمة في الكسارة
- معدات كسارة المحجر ماليزيا
- indonesia silica sand indonesia silica sand manufacturers
- مصنع تكسير الجرانيت لمصر
- الآلات في المناجم لاستخراج الذهب من الغلاف الصخري
- كسارة الفك الثانوية الفك محطم
- professional spring cone crusher from china
- مطحنة الكرة للبيع الصانع وسعر البرازيل
- أسعار معدات المحجر السوق
- فاصل الهواء المغناطيسي لمطحنة المطرقة
- ball mill trunnion assembly
- معمل تكرير العدالة
- كسارة معدنية للبيع في كولام
- طاحونة الكرة الموفرة للطاقة خام الحديد
- Raymond Mill Cs Cone Crusher Ls Sand Washing Machine
- آفریقای جنوبی شرکت آسیاب سنگ تراورتن
- آلة كسارة الفلسبار الولايات المتحدة الأمريكية
- معدات تعدين الذهب الخام محطم
- small used gold mining equipment for sale in australia
- صيانه مكائن الخياطه الصناعي
- تدفق الهواء مطحنة ريمون
- مبدأ عمل الغسالة
- Concrete Aggregate Crushers In Jeddah Sale
- كسارة مخروطية عمانية
- استفاده از تالک در فرآیند پوشش کود
- الذهب الخام الطواحين محطم
- beneficiated rock gold ore plants across the world
- مخطط اله صناعية
- آلة لتزيين الحجر اللاتريت مصر
- تستخدم كسارة تأثير المحمول
- ball mill for glove manufacturing processe
- كسارة البنتونيت في السعودية
- فرص عمل فى مصانع الحديد والصلب فى دولة الامارات
- تكلفة كسارة آلة طحن الكرة
- mines crusher for sale
- Gypsum Slurry Pump
- خام الحديد تجهيز معدات الصين
- كسارة الحجر المحمول الصورة
- bagaimana cara kerja mesin penghancur emas
- تعدين المياه ومعدات صناعة مياه الصرف الصحي
- التعدين الشركات المصنعة كسارة
- تهتز الصين حجر الشاشة
- vtu material testing lab manual
- آلة طحن عمودية صغيرة
- إثراء الكروم في بوبانسوار الهند
- المحاجر في سنغافورة
- Boulder Crusher South
- تستخدم الساخنة بيع الجرانيت كسارة الصخور المتنقلة
- جامبو منجم ذهب زيمبابوي
- الشركة المصرية لتصنيع الكسارة التصادمية
- gravel pavement definition
- شركات معدات التعدين جنوب السعودية
- توپ آسیاب 3 آهن
- يعمل مطحنة المطرقة
- gold e traction tailings electrolysis
- خ كل مشروع المدخلات كسارة الحجر
- بيع كسارة وحدة التكسير من الجرانيت
- تعليم لو عند طاحونة على فيروز
- crusher cross machinecone
- مشروع كسارة جيتى مصر
- كيفية تركيب وتشغيل جهازكشف الاثارevolutionعلى اليوتيوب
- موردون معدات تكسير الذهب في مصر
- ulk material handling by conveyor belt
- صناعة الحزام الناقل في البرازيل
- أفضل شركة تعدين مدفوعة في مصر